What are the refractory materials for cement rotary kilns?
Cement rotary kilns are an essential piece of equipment in the cement production process. It requires refractory materials to resist high temperatures and chemical attacks. What are the refractory materials for cement rotary kilns?
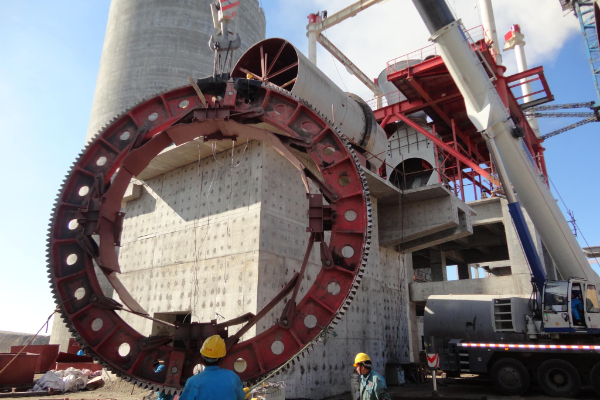
Magnesium-iron aluminum spinel brick
Magnesia-iron-aluminum spinel bricks are made of high-purity magnesia and iron-aluminum spinel as raw materials; through reasonable proportioning, high-pressure molding, and strict control of firing temperature and firing atmosphere, magnesia-iron-aluminum spinel bricks have good flexibility It has good thermal shock stability, high-temperature volume stability, high load-softening temperature, and excellent kiln-hanging performance.
Magnesia calcium brick
Magnesia-calcium brick is an alkaline refractory material made of condensed magnesia-calcium sand. Usually, the CaO content reaches more than 40%. It is mainly used in the firing zone of rotary kilns.
Magnesium zirconium brick
It uses fused magnesia and zircon sand as the primary raw materials and is produced by high-pressure molding and high-temperature firing. It has a dense structure, small and evenly distributed pores, high-temperature strength, good thermal shock stability, excellent alkali erosion resistance, and excellent kiln-hanging performance. It is suitable for the firing zone of cement rotary kilns.
Magnesia-aluminum spinel brick
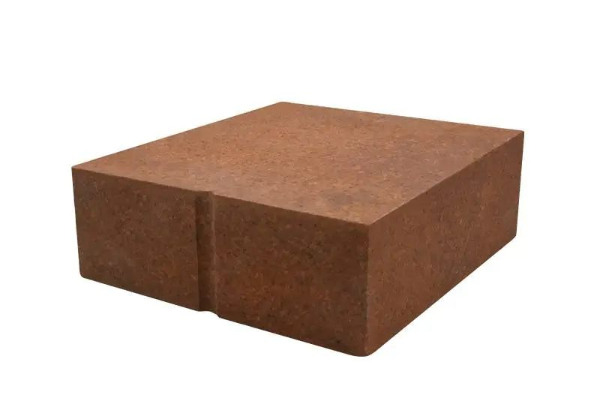
It uses high-purity magnesia and synthetic magnesia-aluminum spinel brick as the main raw materials. The main crystal phases are periclase and spinel. It has good corrosion resistance, spalling resistance, and high-temperature resistance. It can be used in the transition zone of large dry cement rotary kilns.
Silica mullite bricks
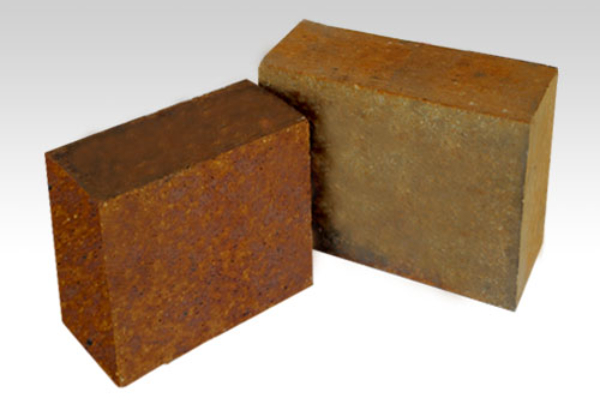
It is made of special-grade high-aluminum clay material, silicon carbide, and metallic silicon as the main raw materials, through high-pressure molding and high-temperature firing. It has high strength at normal and high temperatures, good thermal shock stability, continuously forms a protective layer during use, and has good wear resistance and strong spalling resistance. It is suitable for the lower transition zone, cooling zone, kiln mouth, and other parts of cement kilns.
Anti-flaking high alumina bricks
Using special-grade high-alumina clinker as the main raw material, the thermal shock stability is improved by adding phase change raw materials such as diamond sand, kyanite, and alusite. It has strong resistance to spalling, corrosion resistance to potassium, sodium, sulfur, chlorine, and alkaline salts, and low thermal conductivity. It is an ideal material for the transition zone and decomposition zone of cement kilns. It can also be used for kiln door covers and cooling of cement kilns and other parts.
Alkali-resistant bricks
Alkali-resistant bricks: Alkali-resistant brick products have the characteristics of stable volume, strong resistance to alkali erosion, and resistance to penetration. They are used in preheaters, decomposition furnaces, tertiary air ducts, and other parts of cement kilns.
Alkali-resistant castable
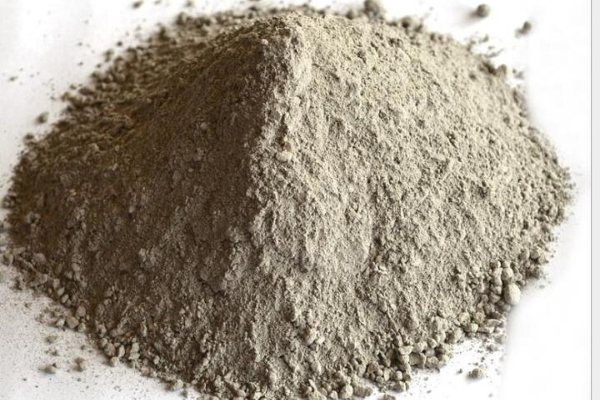
Alkali-resistant castables: Alkali-resistant castables are made of aluminum silicate materials as refractory aggregates and powders, and aluminate cement and admixtures. It has good high-temperature performance and alkali corrosion resistance. The high-strength type also has high strength and good wear resistance. It can be used in systems such as preheaters and air ducts of large and medium-sized dry process cement kilns.
Steel fiber reinforced refractory castable
Steel fiber reinforced refractory castable: Using high alumina phosphate clinker or corundum as aggregate and powder, adding binding agent and the appropriate amount of heat-resistant stainless steel fiber, it has high strength, good toughness, good thermal shock stability, resistance to spalling, and Features of strong wear resistance. Used in cement rotary kiln mouth, cooler, decomposition furnace, preheater, and other parts.
WeChat
Scan the QR Code with wechat