Silicon nitride bricks for ceramic industry
Silicon nitride bricks, as an important refractory material in the ceramic industry, have excellent wear resistance, corrosion resistance and high temperature stability.
In the ceramic industry, silicon nitride bricks are widely used in high-temperature working environments such as kilns and furnaces. Their stable performance ensures the long-term stable operation of the equipment.
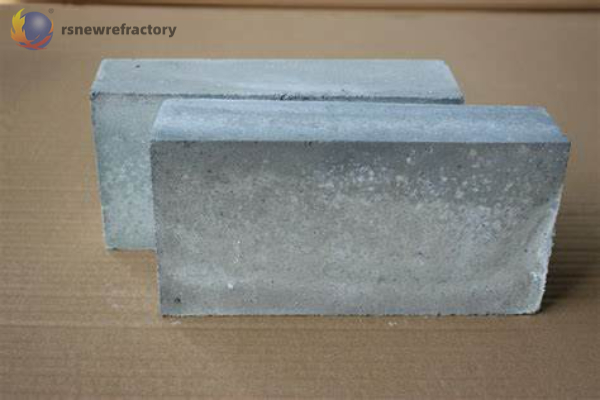
Why does the ceramic industry choose silicon nitride bricks?
During the firing process of ceramic products, the kiln must withstand high temperature, thermal shock and chemical erosion for a long time. Silicon nitride bricks are particularly suitable for the following key use scenarios in the ceramic industry due to their excellent performance:
- Roller kiln load-bearing system
In roller kilns, silicon nitride bricks are often used to support kiln cars or as roller support structural materials. It has high thermal strength and excellent thermal shock resistance, and can bear the operating load for a long time without deformation. - Kiln furnace lining
The excellent corrosion resistance of silicon nitride bricks makes it an ideal choice for the lining of the high-temperature zone of the furnace, especially in the high-temperature atmosphere during the sintering of ceramics, which can effectively resist oxidation and alkaline gas erosion. - Wear-resistant and erosion-resistant parts
The burner mouth, kiln car support and other parts are subjected to material impact and airflow erosion for a long time. The high hardness and density of silicon nitride bricks ensure that they are stable and durable and not easy to break.
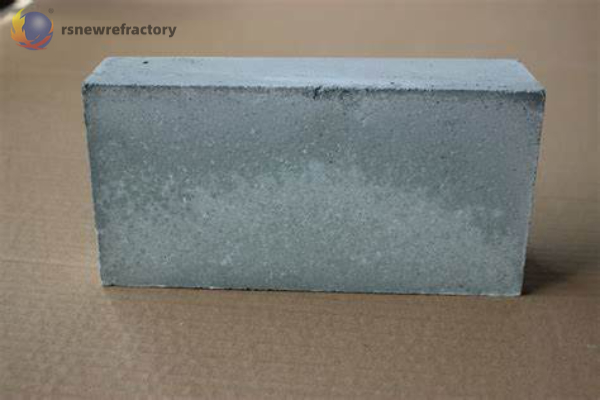
Characteristics of silicon nitride bricks
- Excellent high temperature strength: can maintain good mechanical properties above 1400℃;
- Excellent thermal shock resistance: no cracking or peeling under rapid temperature rise and fall conditions;
- Excellent oxidation resistance and corrosion resistance: adapt to various atmospheres and dust environments in ceramic kilns;
- Low thermal expansion coefficient: reduces structural damage caused by thermal expansion and contraction;
- Long service life: can significantly extend the kiln operation cycle and reduce maintenance frequency compared to traditional materials.
WeChat
وی چیٹ کے ساتھ کیو آر کوڈ اسکین کریں۔