Selection of molten iron ladle refractories
A molten iron ladle is a container for the storage and transportation of molten iron (that is, molten iron in the process of ironmaking and casting). It is usually constructed of refractory materials and is used to carry and maintain the stability of hot molten iron.
Introduction of molten iron ladle
The molten iron ladle is the equipment used for transporting molten iron and pouring molten iron. The tonnage varies, and ironworks generally use 30 tons to 300 tons. The molten iron ladle used for castings is more in the range of 1 ton to 2 tons, and there are transfer ladles and ladles. And the thickness of the lining also varies.

The 60-ton iron ladle is generally lined with aluminum silicon carbide castables, and the construction thickness is about 200mm. If it is a casting, the thickness of the lining of the transfer ladle is about 170mm, while the thickness of the ladle is generally 100mm.
Regardless of the size of the molten iron ladle, the degree of high temperature, thermal shock, and mechanical wear on the lining of the ladle is the same when the molten iron is shipped, but the tonnage of the molten steel is different. When the molten iron is poured out from the ladle, the erosion caused by the impact of the molten iron on the lining is more serious.
Selection of molten iron ladle refractories
The selection of refractory materials for ladles is based on the working environment of the ladles. The selection of inner linings is nothing more than using universal arc bricks or aluminum silicon carbide castables as a whole. The difference is different from the construction method.
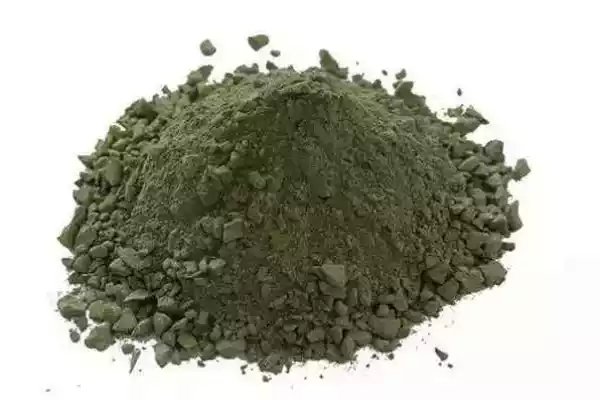
The materials used for building refractory bricks include مٹی کی اینٹوں, اعلی ایلومینا اینٹوں, impregnated bricks, میگنیشیا کاربن اینٹوں, and silicon-alumina bricks. Fireclay of the same material is used for building bricks, and steel bricks are used for integral casting. The mold is cast with aluminum silicon carbide castable to a thickness of 100-200mm, and it must be baked with a special baker before it can be put into use.
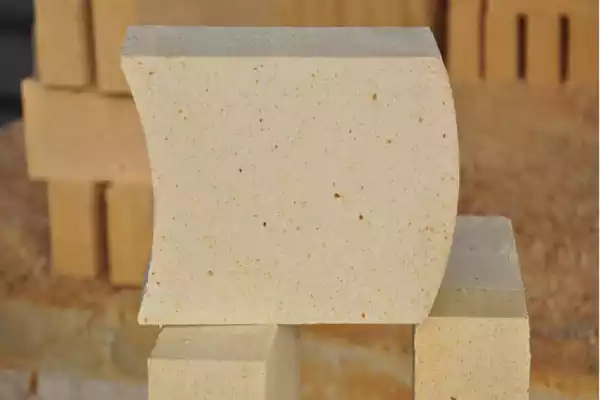
Different ladles use different refractory materials
The refractory bricks used for ladles with different tonnages are also made of different materials. There are more clay bricks for small ladles because of low cost, while aluminum silicon carbide bricks or zircon series silicon carbide bricks are used for large tonnage ladles. High alumina bricks are also used for masonry.
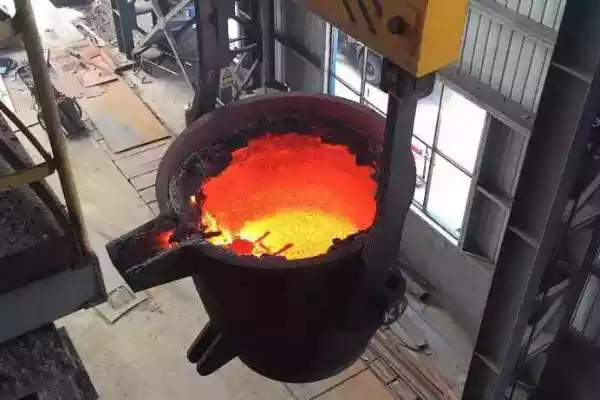
Regardless of whether refractory bricks or castables are used, the effect of use can only be determined by the number of packages used. Brick masonry needs to be baked, and pouring with castables also needs to be baked, but the method and cycle of baking are different, and the number of packages used is also different. The selection of the two should be based on usage habits and usage conditions.
What properties should ladle refractory materials have?
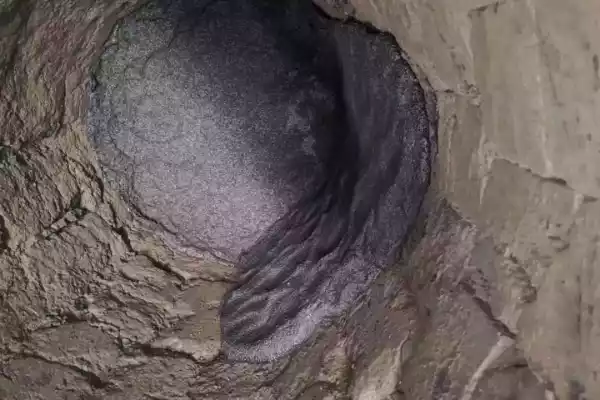
- Temperature resistance of refractory materials: The temperature of molten iron in the ladle is usually very high, so refractory materials need to have good high-temperature resistance. When choosing a refractory material, it should be ensured that it can maintain stable physical and chemical properties in a high-temperature environment to avoid problems such as melting, cracking, or deformation.
- The corrosion resistance of refractories: molten iron contains certain corrosive substances, such as iron slag and metal oxides. اس لیے, refractory materials need to have good corrosion resistance and be able to resist chemical attacks in molten iron. Choosing a refractory material with strong corrosion resistance can prolong the service life of the ladle.
- Thermal shock stability of refractory materials: During the cooling and heating cycle, the ladle will experience a sharp change in temperature, which may cause thermal shock cracking of the refractory material. اس لیے, it is very important to choose a refractory material with good thermal shock stability, which can withstand the stress caused by temperature changes and reduce the risk of thermal shock damage.
WeChat
وی چیٹ کے ساتھ کیو آر کوڈ اسکین کریں۔