Pyrophyllite brick is mainly made of pyrophyllite as the main raw material, with a small amount of sintering aid added and combined with clay.
Pyrophyllite brick appearance
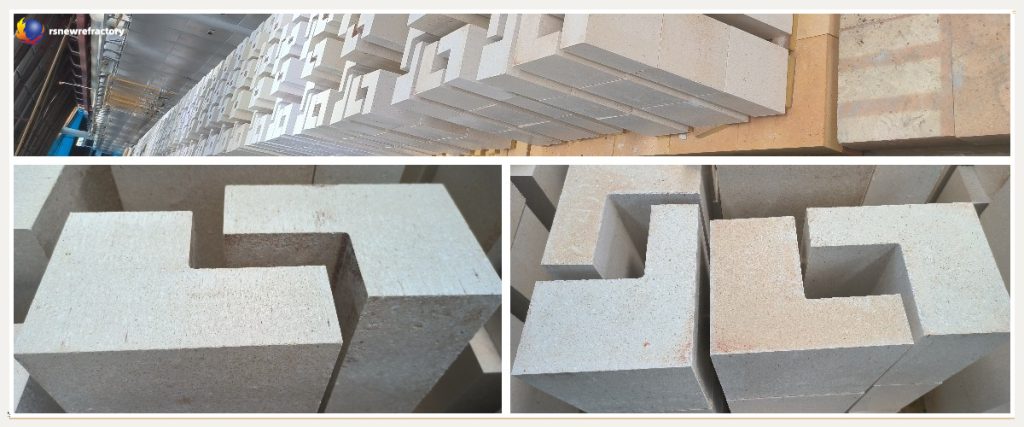
The appearance of phyllite bricks is not much different from refractory clay bricks, which are white or grayish-white. The color of refractory bricks with additives varies depending on the additives. Örneğin, refractory bricks with alumina are light brown; those with zircon are brownish red; and those with graphite are black. Pyrophyllite bricks expand slightly, and their expansion rate is about 0.7~0.9%.
Characteristics of pyrophyllite bricks
- Yüksek refrakterlik; mükemmel termal stabilite
- Low thermal expansion
- The softening temperature under load of 20N/cm2 is 1320℃;
- The apparent porosity is <18%;
- The compressive strength at room temperature is 30-40MPa.
- Pyrophyllite bricks can resist corrosion and degradation by chemicals
- It has strong mechanical strength and can withstand wear and tear under harsh industrial conditions.
Physical and chemical indicators of pyrophyllite brick
Mülk | Birim | Value | |
Density | g/cc | ≥2.0 | |
Görünür Gözeneklilik | % | ≤20.0 | |
Soğuk Kırma Dayanımı | MPa | ≥40.0 | |
Eğilme Dayanımı | MPa | 7 | |
Refractoriness Under Load | At 0.2MPa (t0.5) | ℃ | ≥1330 |
Thermal Expansion | at 1000℃ | % | ≤0,55 |
at 1400℃ | ≤0.57 | ||
Termal iletkenlik | at 400℃ | W/MK | ≤1.2 |
1000℃ | ≤1,4 | ||
Kalıcı Doğrusal Değişim | at 1300℃/2h | % | ±0,2 |
SiO2 | wt % | ≥70 | |
Al2O3 | wt % | ≤23 | |
Fe2O3 | wt % | ≤2,0 | |
TiO2 | wt % | ≤1,5 | |
Alkalis (Na2O+K2O) | wt % | ≤3,0 |
Application of pyrophyllite raw materials in the refractory industry
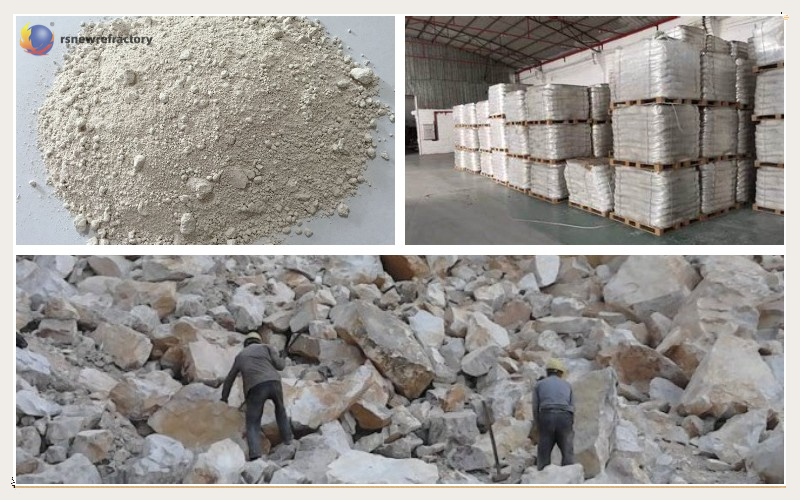
Since pyrophyllite expands in volume at a certain temperature, it can be added to amorphous refractory materials to prevent cracks and peeling, thereby extending the service life of the refractory materials; it can also be added to shaped refractory bricks to ensure good volume stability during use.
Ek olarak, pyrophyllite sprays refractory materials. Using pyrophyllite as raw material to produce refractory materials and other products can not only improve the performance of the products and extend their service life; it can also replace some high-priced raw materials and reduce costs.
Application of pyrophyllite brick
Because of its strong slag resistance, wax stone bricks can prevent cracking caused by high-temperature expansion, can form a whole during use, and the brick seams are very small, so it has a wide range of uses. It has always been the main raw material for producing refractory materials, and its products are widely used in steel ladle lining bricks, iron furnace lining, steel pouring bricks, various kiln bottoms and flues, tin smelting reverberatory furnace hearth, and iron mixing tank level.
How can we improve the quality of pyrophyllite brick?
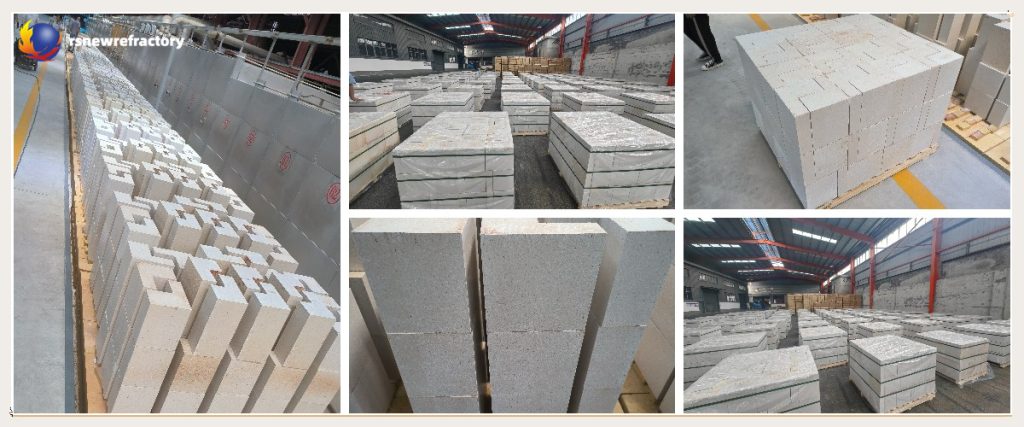
- Select raw materials with high Al2O3 content. From a mineralogical point of view, selecting phyllite with the highest Al2O3 content is one of the ways to improve the quality of phyllite bricks. The higher the Al2O3 content, the better its thermal stability and the better the use effect.
- Strictly control the alkali content. A certain alkali content can promote the sintering of refractory bricks, reduce porosity, and make the aggregate and matrix become one. Fakat, an alkali content that is too high is not good either, as it will deteriorate the refractoriness, load softening point, and thermal stability of refractory bricks, directly affecting the use effect.
- Improve the process and change the microstructure. Mix evenly and increase the molding pressure; use an appropriate firing temperature (controlled between 1320-1350℃).
- To improve the corrosion resistance of refractory bricks, in addition to reducing the porosity of the bricks and increasing the density, the matrix should be strengthened, such as adding alumina, zirconium co-stone, and graphite.
WeChat
QR Kodunu wechat ile tarayın