Performance and characteristics of zirconium corundum bricks
Zirconia corundum bricks are refractory bricks made of industrial alumina and zircon sand. Zirconia corundum bricks can be divided into fused zirconium corundum bricks and sintered zirconium corundum bricks according to the manufacturing process. Fused zirconium corundum bricks are commonly known as white iron bricks, also known as corundum-badgeolith bricks. The main chemical composition is Al2O3 50% ~ 70%, ZrO2 20% ~ 40%, and the rest is SiO2. The main mineral components are baddeleyite (ZrO2), korindon (-Al2O3) and glass phase. Baddeleyite crystals constitute the skeleton of the brick, and ZrO2 has a high melting point (2715), good chemical stability and strong corrosion resistance to acidic and alkaline media, especially molten glass.
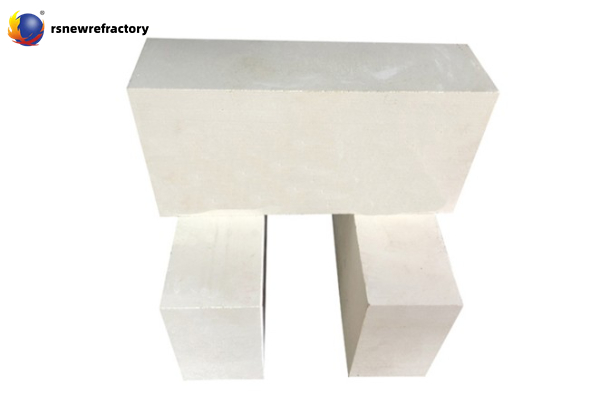
Erimiş zirkonya korindon tuğlası
Fused chromium zirconium corundum brick is also called AZCS brick, which are cast using a shrinkage-free casting process. The surface and interior of the bricks are dark green. The fused bricks contain 4.5% shrinkage pores and no connecting pores. They are used in industrial furnaces such as glass melting furnaces, where they are used to lay the upper pool wall, small furnace flat arch, small furnace chimney, tongue arch and breast wall. Colored glass furnaces can use AZCS bricks containing Cr2O3 to build the pool wall, which improves the corrosion resistance of the pool wall.
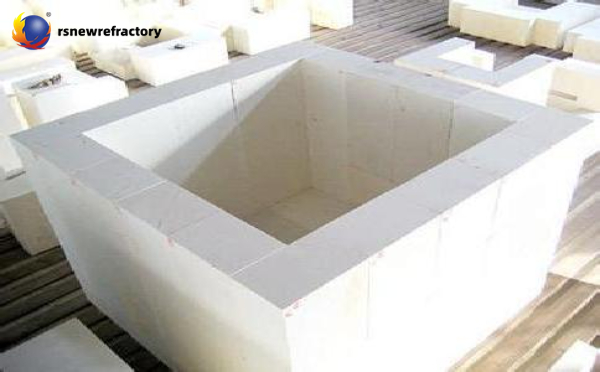
The following issues should be noted when using fused zirconium corundum bricks:
- Irregular changes in thermal expansion. The expansion curve of fused zirconium corundum bricks is abnormal at around 1000, and the Zr02 crystals inside undergo a reversible crystal transformation with a large volume change. Öyleyse, bricks containing ZrO2 should not be used in places with drastic temperature fluctuations around 1000. When entering the kiln for baking, the temperature change from 900 ile 1150 should not be too large, generally not exceeding 15/h, and a steady temperature rise is required. Some parts should be protected from cold wind, and bricks should be used to prevent cracking.
- Shrinkage. During the pouring process, shrinkage holes often appear at the water inlet. The bricks here have more pores, resulting in poor density. Öyleyse, when building the wall of the glass melting pool, the shrinkage holes are all facing the kiln. If the pouring port faces outward, when the brick body is eroded to a very thin degree, it will cause a glass liquid leakage accident. When used in the flame space above the pool kiln, the service life is very long and there will be no problem of glass liquid leakage. Öyleyse, the nozzle is used outward to extend the service life.
- Eutectic, when fused zirconium corundum brick is laid in contact with clay brick, eutectic phenomenon will occur at 1300. Öyleyse, when selecting refractory materials, refractory materials with serious eutectic phenomenon should be avoided. Örneğin, if silica brick is under fused zirconium corundum brick, it is easily corroded by fused zirconium corundum brick.
Sinterlenmiş zirkonyum korindon tuğlaları
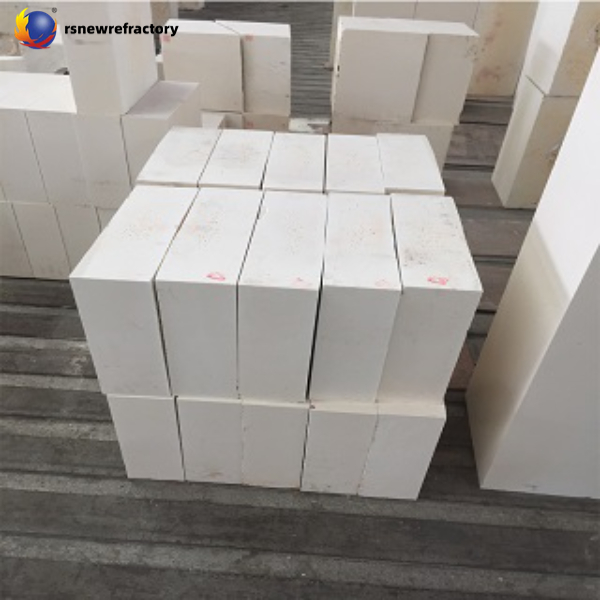
Sinterlenmiş zirkonyum korindon tuğlaları are also called ceramic bonded aluminum silicon zirconium bricks. İle karşılaştırıldığında fused zirconium corundum brickS, sintered zirconium corundum brick has similar chemical composition, but have the advantages of no carbon, low glass phase content, uniform structure, no shrinkage, good thermal shock stability and corrosion resistance.
WeChat
QR Kodunu wechat ile tarayın