Zircon refractory bricks for glass kiln
Zircon refractory products are acidic materials, which are made from natural zircon sand (ZrSiO4). Zircon refractory bricks have good slag resistance, a small thermal expansion rate, thermal conductivity that decreases with the increase of temperature, อุณหภูมิอ่อนตัวสูงภายใต้ภาระ, ทนต่อการสึกหรอสูง, และทนต่อแรงกระแทกจากความร้อนได้ดี, and have become important in the industrial field. high-temperature material.
What factors are considered in the selection of glass kiln materials?
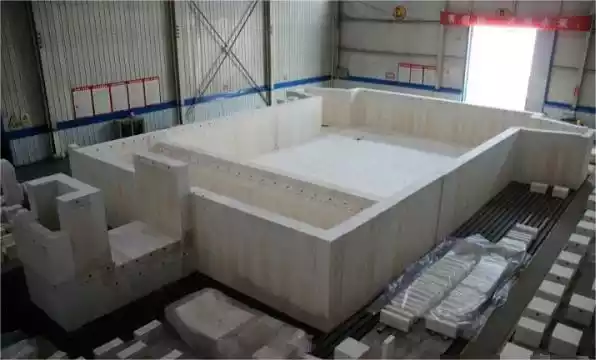
The molten glass and flame-flying materials in the glass-melting furnace will cause certain erosion and damage to the refractory material, which in turn affects the service life of the glass-melting furnace. นอกจากนี้, it is necessary to avoid and reduce the pollution of the molten glass. ดังนั้น, the selection of refractory materials also has a great relationship with the life of the glass furnace and the quality of the glass.
How are zircon refractory bricks produced?
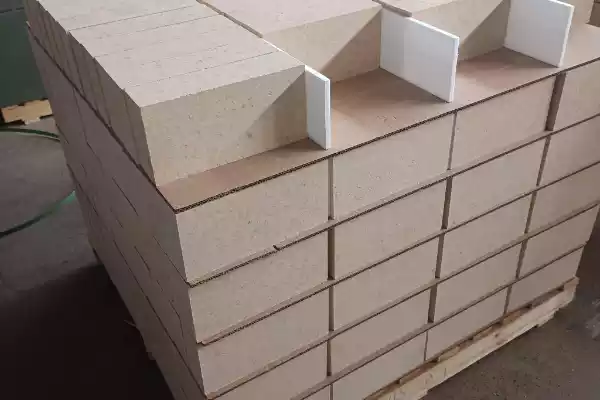
Zircon bricks for glass kilns are made of zircon as the main raw material, adding binders and additives, equipped in proportion, and fired at high temperatures after stirring, kneading, การปั้น, and drying. Zircon refractory bricks are produced according to the production process and the physical and chemical indicators are divided into high-density type and dense type.
Where is the dense zircon brick for glass kilns mainly used?
Zircon refractory bricks are used in the working layer of glass kiln pool walls, which have a high density and a strong ability to resist the erosion of glass liquid as a working layer of the pool wall.
Properties of zircon refractory bricks for glass kiln
- High refractoriness and high softening temperature.
- Strong resistance to slag liquid erosion and strong acid resistance.
- กำลังอัดสูง.
- ทนต่อแรงกระแทกจากความร้อนได้ดี.
Method for improving slag resistance of zircon bricks
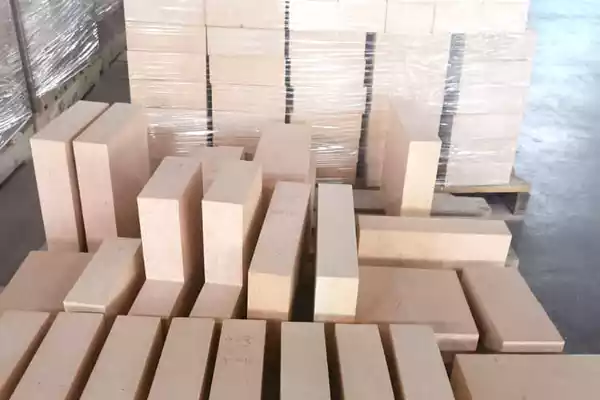
- Products with low porosity and air permeability can be produced by adjusting the particle composition and changing the molding method, but at the same time, it will lead to a decrease in thermal shock stability
- Add additives to improve the viscosity of the brick and slag interaction product
วีแชต
สแกน QR Code ด้วย wechat