Application of refractories in the side-blowing furnace for blister copper smelting
The side-blowing furnace is a device for producing blister copper smelting. Oxygen-enriched air is blown into the furnace through the primary tuyeres in the slag line area and reacts under the action of high temperature. The blister copper sinks below the molten pool and is discharged to the electric furnace. Gathered in the upper part of the molten pool, it is discharged to the electric furnace through the overflow, and the corresponding flue gas is discharged from the flue to the boiler gas.
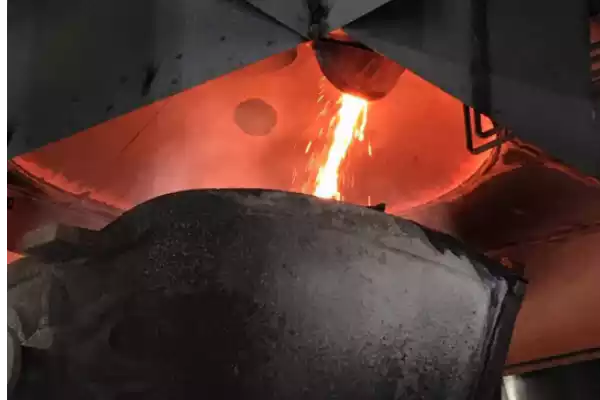
Blister copper smelting side blowing furnace structure
The body structure of the side-blowing furnace adopts a fixed rectangular furnace type, which is composed of a copper water jacket, วัสดุทนไฟ, and steel structure. The furnace body is divided into four parts from bottom to top: เตาไฟ, ตัวเตา, furnace roof, and flue. The hearth used to store the blister copper and slag produced by the reaction is made of refractory bricks, and a slag chamber is set at the end of the hearth to separate the copper slag.
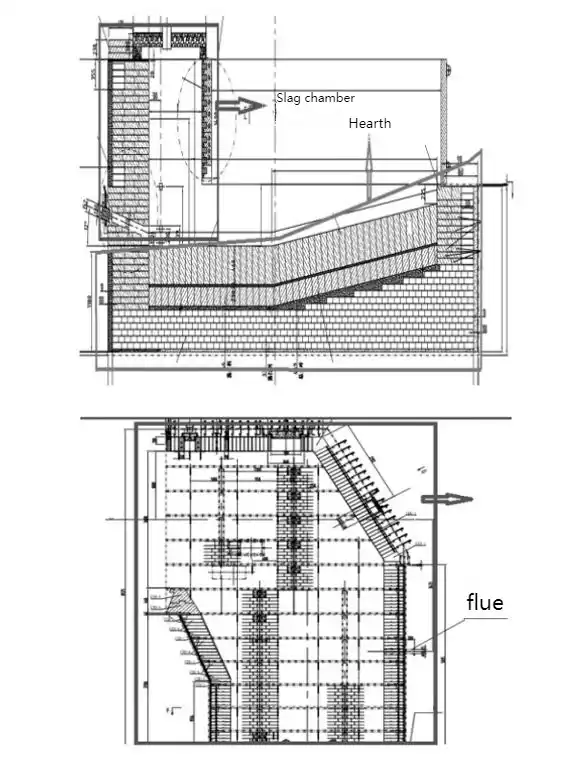
The furnace body is divided into a reaction zone and a flue gas zone. The reaction zone is composed of a copper water jacket and primary tuyere, and the flue gas zone is composed of a slotted copper water jacket and a secondary tuyere for slag-hanging protection. The reaction flue gas is discharged from the flue gas outlet formed by the water jacket and enters the flue. The size of the flue space is calculated according to the flue gas flow rate to ensure that the flue gas stays in the flue for more than 2s. The main reaction area of the side-blown furnace belongs to the protection position of the copper water jacket, and the refractory materials are mainly used in the hearth, slag chamber, and flue.
Selection of refractory composition for side-blowing furnace
From the working principle of the side-blowing furnace, it can be seen that the hearth and slag chamber of the side-blowing furnace will be eroded and washed by the melt, and the flue will be eroded by a small amount of molten slag spray and washed by dusty flue gas. Under normal furnace conditions, the temperature in these three areas is 1100~1300°C; but in the case of unstable furnace conditions, the temperature in these three areas can reach above 1400°C. In the actual production process, the side-blowing furnace needs to be supplied with oxygen-enriched primary air and secondary air, and forms a strong oxidizing atmosphere locally, so the side-blowing furnace should choose refractory bricks that are not easily oxidized.
The main components of slag are FeO, SiO₂, แคลเซียมโอ, AI₂O₃, high alumina refractory materials and silica refractory materials will participate in slagging, which is not suitable for side-blowing furnaces. ดังนั้น, the refractory materials for side-blown furnaces need to have the characteristics of high-temperature resistance, strong thermal stability, high load deformation temperature, แรงอัดสูง, ความต้านทานออกซิเดชัน, and not participating in slagging. Combined with the characteristics of refractory materials, magnesia refractory materials should be selected for side-blowing furnaces. The increase of Cr₂O₃ content in magnesia refractories can improve the slag erosion resistance of materials, so the refractory bricks of side blowing furnace hearth, slag chamber, and flue should choose magnesia chromium refractories with higher Cr₂O₃ content.
How to choose magnesia chrome refractories?
ชื่อ | Direct binding | Half recombination | Electrofusion recombination |
Fused magnesia chrome sand | few | join more | a lot |
มีความพรุนอย่างเห็นได้ชัด | ปานกลาง | lower | very low |
ความหนาแน่นเป็นกลุ่ม | ปานกลาง | higher | very high |
ความแข็งแรงที่อุณหภูมิสูง | ปานกลาง | higher | very high |
ความต้านทานการกัดกร่อน | ปานกลาง | good | very good |
The performance of fused recombined magnesia-chrome refractories is the best, followed by that of semi-recombined magnesia-chromium refractories. Combined with the loss of refractory materials in the hearth, slag chamber, and flue area of the side-blowing furnace, the hearth, slag chamber, and flue area adopt semi-recombined, electrofusion recombined, and directly bonded magnesia-chromium refractory materials.
Chemical composition and physical performance indicators of magnesium-chromium refractories
Index item | Direct binding | Half recombination | electrofusion recombination | |
Component Mass Score/% | Mgo | ~ 60 | ~ 60 | ~ 60 |
Cr2โอ3 | 16~ 17 | 20~21 | 20~21 | |
สิโอ2 | ~1.2 | ~1.2 | 1.0~ 1.5 | |
Apparent porosity/% | 14~15 | 14~15 | 14~15 | |
Bulk density/(กรัม/ซม3) | 3.26 | ~3.25 | 3.28 | |
Compressive strength/MPa | 60~65 | ~50 | 60~ 70 | |
0.2MPa Load softening start temperature/°C | >1700 | >1700 | >1700 | |
Thermal expansion rate/% (1200องศาเซลเซียส) | 1.24 | 1.23 | 1.28 | |
การนำความร้อน(1200℃)/【W/(ม. k)】 | 1.37 | 13.2 | 1.32 | |
Thermal shock/time (1100°C water cooling) | >7 | >7 | >7 |
วีแชต
สแกน QR Code ด้วย wechat