การแนะนำกระบวนการผลิตอิฐทนไฟแมกนีเซีย - โครไมต์
Magnesia-chromite refractory brick is an alkaline refractory product containing MgO: 55%-80%, Cr2O3: 8%-20%, with periclase and composite spinel XO·Y2O3 as the main crystal phases, among which XO is mainly MgO and FeO; Y2O3 is mainly Cr2O3, อัล2O3, เฟ2O3. The molar number of XO and Y2O3 is equal, and the excess Y2O3 is dissolved in the composite spinel. There is also a small silicate phase (forsterite and olivine).
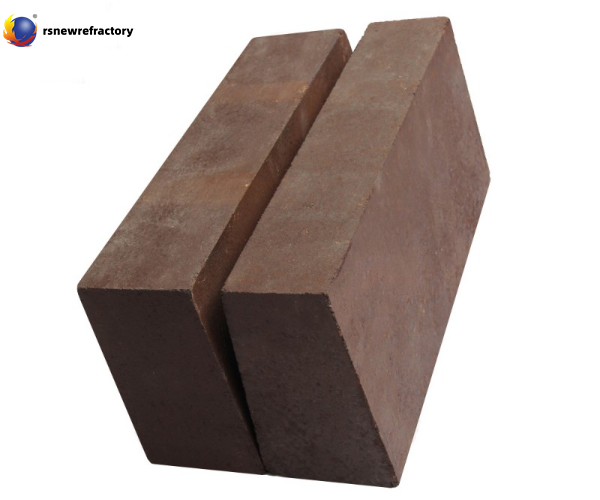
Magnesia-chrome bricks raw materials
Magnesia-chrome bricks are made of high-quality sintered magnesia sand and chromite (Cr2O3: 30%?45%, CaO less than 1%~1.5%) as the main raw materials. The production process of magnesia-chrome bricks is generally similar to that of อิฐแมกนีเซีย. Unfired magnesia-chrome bricks use an inorganic magnesium salt solution as a binder. The loosening effect is caused by the expansion of MgO and Cr2O3, อัล2O3, or iron oxides during the firing process to form spinel. Pre-synthesized magnesia-chrome sand can be used to make bricks, which must be fired in an oxidizing atmosphere above 1600℃. If the atmosphere properties change, Fe2O3 in chromite is affected by oxidation-reduction reactions to form various valent oxides of iron. ในเวลาเดียวกัน, Cr2O3 is also reduced to produce compounds of different valences. Under repeated reactions, the bricks are damaged, so products with high MgO and low Cr2O3 are used as much as possible.
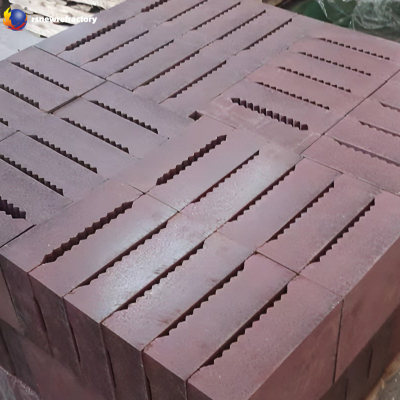
Types of Magnesia-chromite refractory brick
Magnesia-chrome bricks can be divided into fused-cast magnesia-chrome bricks, directly bonded magnesia-chrome bricks, silicate bonded magnesia-chrome bricks, recombinated magnesia-chrome bricks, semi-recombined magnesia-chrome bricks, pre-reacted magnesia-chrome bricks and unfired magnesia-chrome bricks.
Effect of preparation technology on properties of magnesia-chromite refractory brick
The difference in production process makes the structure of magnesia-chrome materials significantly different, which in turn affects the performance of magnesia-chrome bricks. ตัวอย่างเช่น, direct-bonded magnesia-chrome bricks have good thermal shock stability, fused-bonded magnesia-chrome bricks have strong corrosion resistance, and the performance of semi-rebonded magnesia-chrome bricks is between the two. For this reason, this section will discuss in detail the impact of the production process on the performance of magnesia-chrome bricks.
What properties does the preparation process affect on magnesia-chrome refractory bricks?
The production process has an impact on the organizational structure, hot strength, thermal shock stability, เป็นต้น. of magnesia-chrome bricks
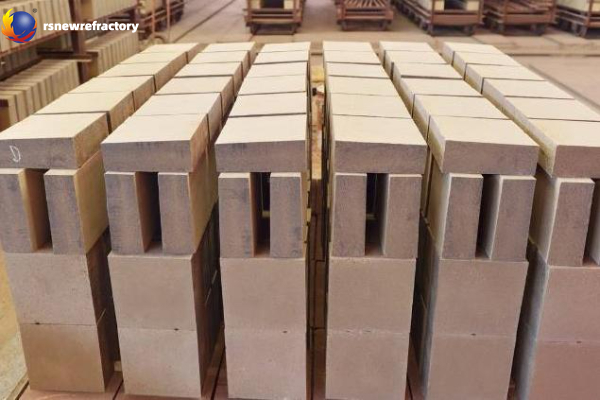
Effect of chromium ore on the performance of MCH bricks
Chromium ore is the main raw material for producing magnesia-chromite refractory bricks. The content of main impurities varies due to different sources. นอกจากนี้, the amount of chromium ore added will also affect the performance of protactinium-chrome bricks. This section will mainly explain the influence of chromium ore source and additional amount on the performance of directly bonded magnesia-chrome bricks.
Influence of chromium ore particle size
The compressive strength of the product increases with the decrease of the critical particle size of chromium ore, while the high-temperature flexural strength (1400℃, 0.5h) decreases with the decrease of the critical particle size of chromium ore. When the critical particle size of chromium ore is 1.5mm, the thermal shock stability reaches a peak.
Effect of chromium ore content on the properties of direct bonded magnesia-chrome bricks
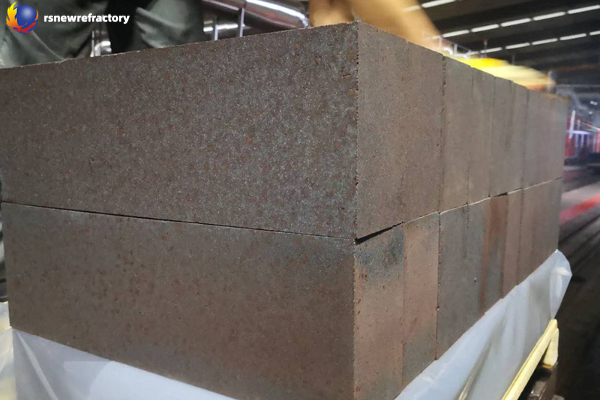
With the increase of chromium ore content, the apparent porosity of the directly bonded magnesium-chromium sample decreases, the bulk density increases, and the thermal shock stability improves.
วีแชต
สแกน QR Code ด้วย wechat