Forming method of special-shaped refractory bricks
Forming in the manufacturing process of refractory bricks refers to the process in which refractory raw materials are processed into bricks of specified size and shape with the help of external forces and models. There are many molding methods for special-shaped refractory bricks. Commonly used molding methods include compression molding, vibration molding, extrusion molding, ramming molding, isostatic pressing, melting and casting, grouting, etc.
How to choose the forming method of special-shaped refractory bricks?
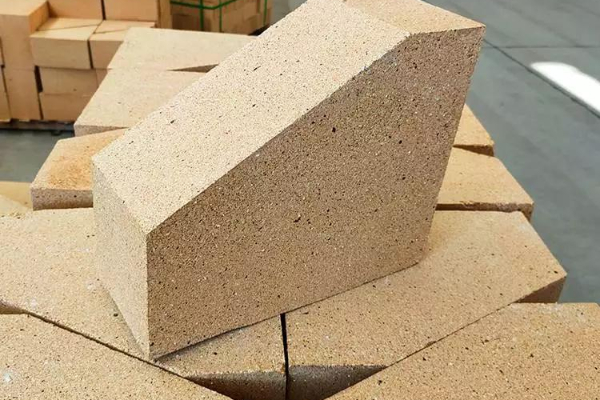
The choice of molding method is mainly based on the properties of the mud material, the shape and size of the green body, and other process requirements. In addition to the vast majority of refractory bricks that are machine-pressed, vibration molding is generally used to form large special-shaped refractories, controlled pressure molding is generally used to form tubular refractories and grouting molding is generally used to form hollow-walled refractories. Isostatic pressing is currently mainly used for the production of high-performance refractory materials.
Of course, the choice of forming method is also limited by the equipment conditions of the production plant, so some refractory bricks cannot use better farming methods.
Refractory brick molding meets usage requirements
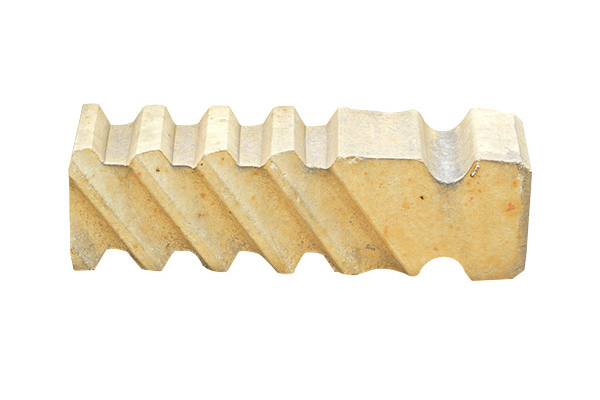
The forming of refractory bricks is first of all to meet the use requirements of the product. When laying refractory bricks, the product is required to have a certain shape, accurate size, and sufficient strength. Secondly, molding is also an effective means to improve the physical and chemical properties of products. Molding can improve the organizational structure of products.
Method of forming refractory bricks
According to the moisture content of the blank, it can be divided into
(1) Semi-dry method: The moisture content of the raw materials is about 5%, and it is suitable for raw materials with different clinker contents (50%–100%):
2) Plastic method: The moisture content of the bad material is about 15%, which is suitable for manufacturing large or complex-shaped products.
(3) Grouting method: The moisture content of the bad material is about 40%, and it is suitable for the production of various types of hollow thin-walled refractory materials.
Requirements that fire brick molding should meet
(1) Shape, size, and accuracy meet design requirements
(2) The structure is uniform and dense, with no cracks on the surface or inside.
3)Have sufficient mechanical strength
(4) Meet expected physical performance requirements. The processing process of refractory bricks is forming. The main methods are machine pressing forming, isostatic pressing forming, melting casting forming, vibration forming, ramming forming, extrusion forming, hot pressing forming, etc.
WeChat
Scan the QR Code with wechat