Repair method for damaged sidelining of the electrolytic cell
This article introduces the traditional repair of damaged parts of the electrolytic cell lining and the improved repair methods.
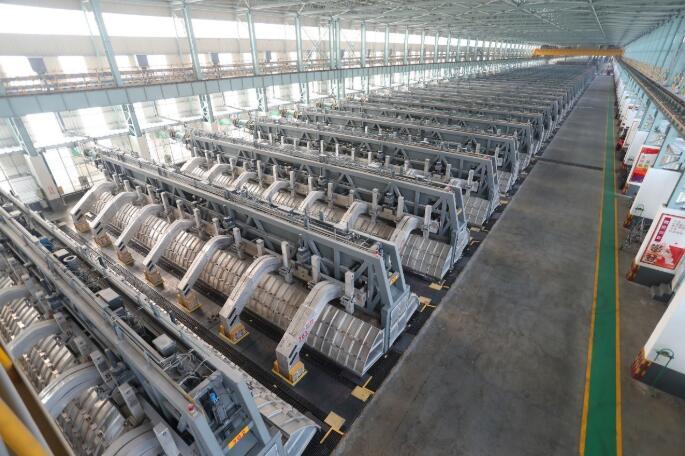
Traditional thermal repair method for damaged parts of electrolytic cell side lining
The traditional hot repair method for the side of the electrolytic cell is to insert a steel plate at the anode end corresponding to the damaged repair part of the side lining. The steel plate plays a role in blocking the electrolyte and aluminum liquid, and then a certain amount of steel plate is added between the steel plate and the tank shell. Use the shelling mechanism of the multi-function crane to compact the repaired area with a certain amount of broken pieces. After compacting, use a pneumatic pick to dig a trench along the damaged area along the tank shell. The size of the trench is determined according to the actual conditions on-site. În general, the trench is planned to the upper edge of the artificial extension leg, with a depth of about 20cm and a width of about 12cm. A small amount of aluminization occurs during the trenching or cleaning process. În general, it is covered with refractory mud and red clay mud, and then the trench is cleaned. , spray coal tar on the lowermost part, level the lower part with hot paste at about 100℃, and place the side carbon blocks in the trench. When installing side carbon blocks, it is required that the gap between adjacent side carbon blocks is as small as possible, that the upper surface of the side carbon blocks is flush with the edge of the electrolytic cell or lowered by 1cm, and that the gap between the carbon blocks and the side tank shell is Alumina powder is filled in. After the above construction is completed, the steel plate is pulled out, and the pressed iron plate is finally welded.
Optimization and improvement of thermal repair methods for damaged linings on the side of electrolytic cells
The purpose of improving the repair method is to repair the sidelining of the electrolytic cell without affecting the operation of the electrolytic cell and the quality of the aluminum liquid. After research, the technicians decided to disconnect the anode guide rod corresponding to the repaired part during repair to make the anode non-conductive. The temperature of the repaired part will be reduced, the magnetic field will be weakened, and the chance of aluminum infiltration during repair will be less. After inserting the steel plate, the aluminum liquid will The quality is not affected, but the repair effect of traditional hot repair methods can be achieved. The processes such as grooving are the same as those of traditional hot repair methods, but cold tamping is used for the lowermost leveling paste.
To ensure construction safety during repair, after disconnecting the anode guide rod, wrap kraft paper between the guide rod and the horizontal busbar, the guide rod, and the small box fixture, and ensure that the guide rod is vertical and does not contact the hook. Prevent accidents such as electrical conduction at the contact part, local overcurrent, and damage to the hook port process energy-saving fixture due to sudden anode effect.
Theoretical analysis of the anode guide rod being able to cut off power during the repair of the sidelining of the electrolytic cell: A company’s 240kA electrolytic cell has dual anodes, and the anode current density is 0.733A/cm. When one group of anodes is non-conductive, the other anodes share the current At this time, the anode current density increases to 0.782A/cm. According to literature reports: With the improvement of the anode carbon block production technology, the current density of the anode carbon block can currently reach more than 0.9A/cm, so it is feasible to perform furnace thermal repairs after disconnecting a set of anode guide rods.
The most important operation in aluminum electrolysis production is to replace the anode. Under normal production conditions, the anode needs to be replaced every two days in the tank. The anode replacement time is about 20 minute. After the new anode is put into the tank, due to the huge temperature difference between the anode and the electrolyte, the new anode will After being immersed in the electrolyte and in contact with the anode bottom palm, a layer of electrolyte condensation shell is formed on the surface of the anode bottom palm due to the temperature difference. This layer of condensation shell completely isolates the liquid electrolyte from the anode, so that the anode carbon block loses its conductive effect. As the new anode hangs in the tank for longer and the temperature gradually rises, the electrolyte condensation shell on the surface of the new anode’s bottom palm gradually melts, and the anode current distribution area gradually increases. După 16 ore, the anode current distribution area reaches 70%, while the inner side of the repaired side The time for disconnecting anodes during lining generally does not exceed 3 ore, which fully proves that disconnecting a group of anodes within 3 hours will not have any impact on the electrolytic cell.
WeChat
Scanați codul QR cu wechat