Clasificarea amestecurilor de batere refractare
Refractory ramming mixes are amorphous refractory materials constructed by ramming (manual or mechanical) and hardened under heating above normal temperature. Masa de batere refractară is composed of refractory aggregate, pudra, liant, and admixture in proportion, and is constructed by ramming, so it is called refractory ramming mass. It is made by mixing refractory aggregate, pudra, liant, or admixture with a certain grade, apă, or other liquid.
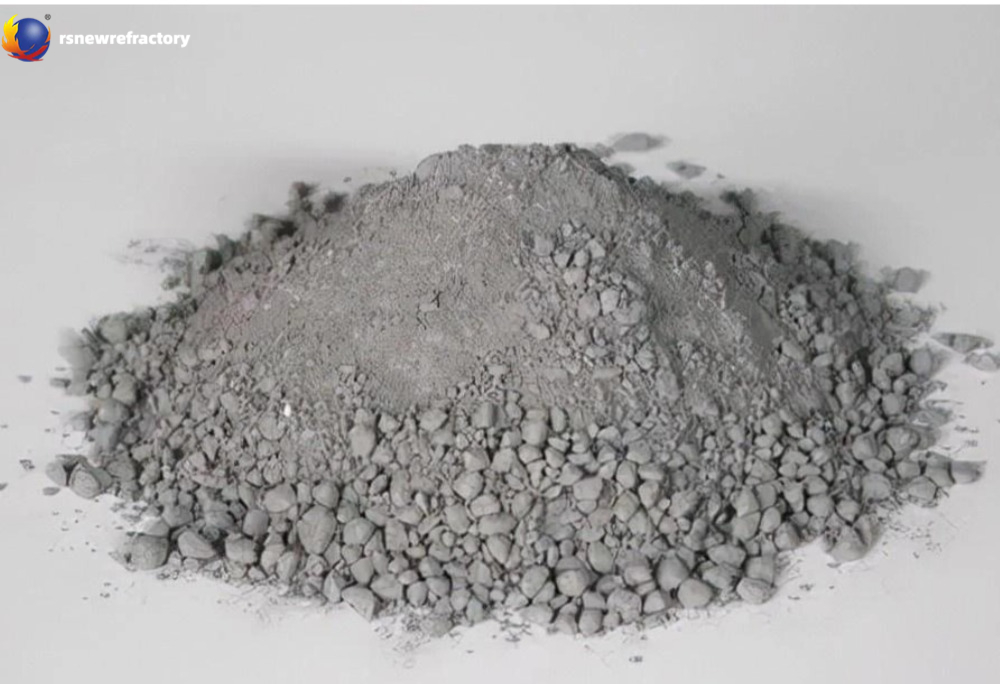
Clasificarea amestecurilor de batere refractare
There are many types of ramming materials. The material contains high-alumina, lut, magnezia, dolomită, zirconium, and silicon carbide-carbon refractory ramming materials.
Refractory ramming masses are divided into clay ramming materials, bogat în alumină, mullite corundum, silice, magnezia, and silicon carbide according to the type of refractory aggregate;
Ramming refractories are divided into water glass, phosphoric acid and phosphate, aluminum sulfate, brine, ciment, bonded clay, and organic binders according to the type of binder.
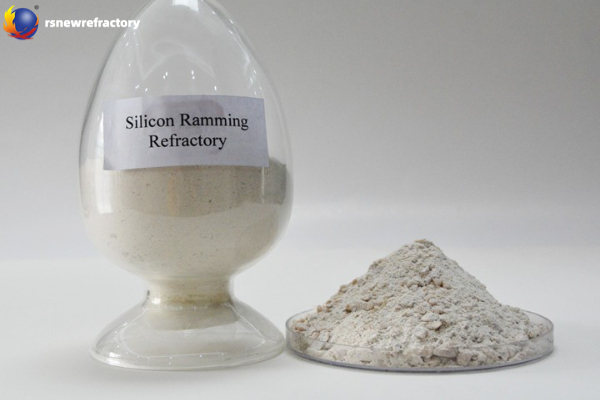
Refractory ramming mass construction
The refractory ramming material is mixed on-site and rammed with a pneumatic pick or machine, and the wind pressure is not less than 0.5MPa. The parts with less material or unimportant use can also be knotted by hand. Prin urmare, the lining of the refractory ramming mix has low moisture content and dense knots, and its performance is better than the refractory castables of the same raw materials. The disadvantages of refractory ramming material are slow construction speed and high labor intensity. It has a tendency to be replaced by dry vibrating material and high-quality refractory castables.
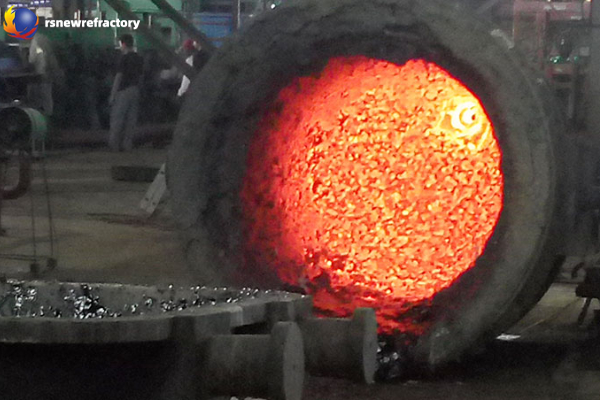
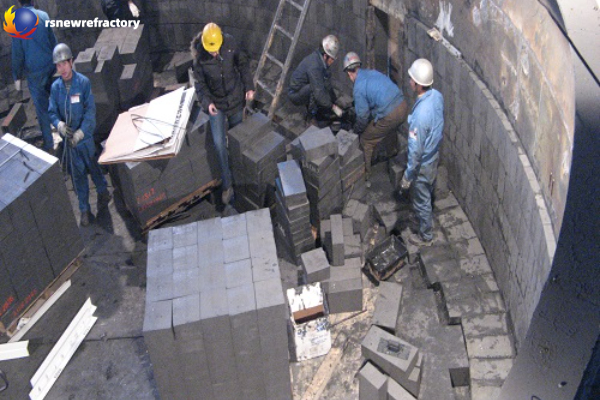
Application of refractory ramming
Refractory ramming is widely used, especially in thermal equipment such as smelting furnaces. In recent years, a variety of carbon-containing and silicon carbide refractory ramming materials have been developed and used on the lining of the iron ditch of blast furnaces. The lining life has been greatly improved compared with traditional iron ditch materials. In the bridge and other parts of large hot weathering ironmaking furnaces, the use of refractory ramming materials containing mismatched carbon are used to ram the working lining, which has also achieved outstanding application results. New types such as silicon carbide and silicon nitride refractory ramming materials have also been used in blast furnaces.
WeChat
Scanați codul QR cu wechat