The functions and types of refractory ramming mass
Refractory ramming mass is used to repair and protect the refractory brick masonry inside industrial furnaces. It has important functions and many types.
Refractory ramming materials introduction
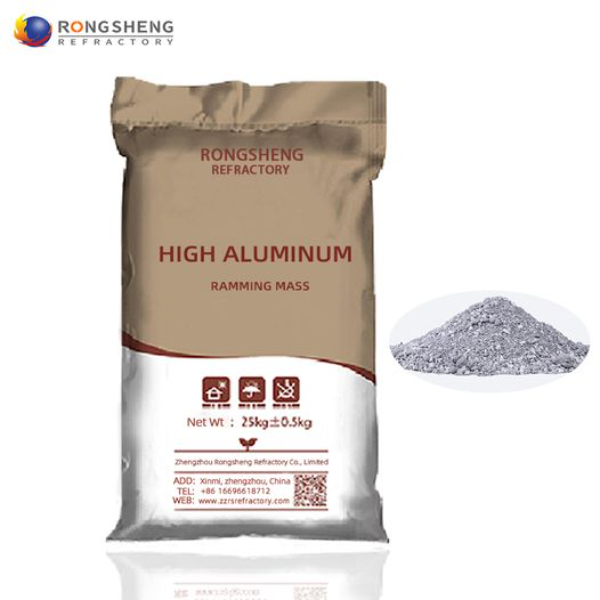
Refractory ramming materials generally refer to dry ramming mass, including clay, alumină ridicată, mullite, corindon, silicon, magneziu, carbură de siliciu, mullite, and corundum. It is a bulk material made by adding a variety of ultra-fine powder additives and using fused cement or composite resin as a binding agent. The different combination methods are water glass, phosphoric acid, phosphate, aluminum sulfate, brine, high alumina cement, lut, and other binding agents. It is used to fill the gap between the furnace cooling equipment and the masonry or the filling material for the masonry leveling layer. Ramming materials have good chemical stability, are resistant to erosion, abrasion, spalling, and thermal shock, and are widely used in metallurgy, materiale de construcții, topirea metalelor neferoase, industria chimica, utilaje, and other manufacturing industries.
Application of ramming materials
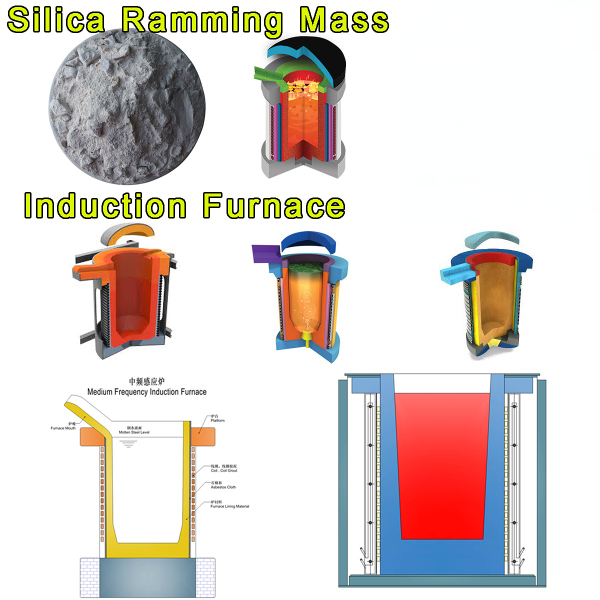
Acidic, neutral, and alkaline ramming materials are widely used in coreless intermediate frequency furnaces and cored induction furnaces. As intermediate frequency furnace ramming materials, they are used to melt gray cast iron, ductile iron, D-forged cast iron, vermicular graphite cast iron, and cast iron alloys. , melt carbon steel, alloy steel, high manganese steel, tool steel, heat-resistant steel, stainless steel, melt aluminum, and its alloys, melt copper alloys such as copper, brass, white copper bronze, and other special steels.
What are the types of refractory ramming mass?
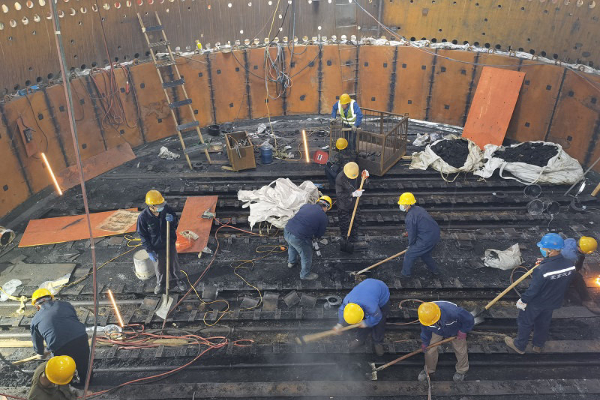
The types of ramming materials can be divided into carbon ramming materials, silica ramming materials, corundum ramming materials, magnesia ramming materials, and medium-frequency furnace ramming materials.
WeChat
Scanați codul QR cu wechat