Care sunt efectele compoziției cărămizii de rulare de mullit asupra performanței?
Brick types using flow steel bricks in the mold casting system include funnel bricks, injection pipe bricks, center bricks, DC bricks, flow steel tail bricks and mold bottom bricks. The raw mineral composition of mullite runner brick is mainly kaolinite (Al2O3·2SiO2·2H2O) și 6% la 7% impurities (potasiu, sodiu, calciu, titanium, iron oxides). The firing process is mainly a process in which kaolinite continuously loses water and decomposes to form mullite (3Al2O3·2SiO2) crystals. Mullite crystal is the only stable form of aluminosilicate under high temperatures, and its theoretical conversion rate is 87.64%. SiO2 and Al2O3 in flowing steel bricks form eutectic low melting point silicates with impurities during the firing process, surrounding the mullite crystals.
Mullite runner brick component
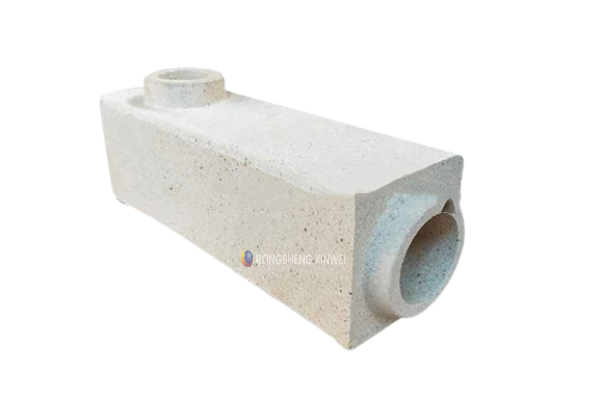
The main component of mullite runner brick is alumina, followed by silica, and also contains a small amount of iron oxide. It is conceivable that the physical and chemical properties of fluidized steel bricks are closely related to the contents of these main components. Changes in the main components will have a greater impact on the physical and chemical indicators of fluidized steel bricks.
The main forms of damage to fluidized steel bricks during high-temperature reactions
When the flowing steel bricks are in contact with the molten steel, the interaction between the molten steel and the refractory material includes the following aspects.
- First, the refractory material is eroded by the molten steel, causing the refractory material to peel off, and the refractory material falls into the molten steel. This is a physical process. În general, it is easy to occur when there are unstable points such as low melting point caves in the refractory material locally;
- Second, the components in the refractory material, such as oxides, carbon, nitrides, etc., react chemically with elements such as Al, Si, Mn, Fe, etc. in the molten steel. The reaction interface is large, but the thickness of the chemical reaction layer is small, and this reaction runs through the entire process of contact between refractory materials and molten steel. Since the physical dissolution process often occurs before the chemical reaction process, and the speed of physical melting loss is much faster than the speed of chemical reaction, it can be considered that the contact between flowing steel bricks and molten steel occurs. The main act of damage is physical melting.
- The reaction between bottom pour brick and molten steel is physical melting first and then a chemical decomposition reaction. The thickness of the decomposition reaction interface layer is minimal and the reaction speed is slow. Using the melting point of flowing steel bricks to characterize the refractoriness is scientific, and the calculation method is relatively simple.
WeChat
Scanați codul QR cu wechat