Introducere funcții filtre cu spumă ceramică
Ceramic foam filters can significantly improve the quality of cast iron parts and reduce scrap rates. They can also be used in continuous casting and rolling processes and can be manufactured in all standard sizes and different thicknesses.
The basic materials of foam ceramic filters include silicon carbide, zirconia, and alumina. The foam ceramic filter has an excellent filtration effect on molten copper or molten iron. It uses a three-dimensional structure to effectively remove oxidized inclusions and other non-metallic inclusions through blocking, capturing, and adsorption.
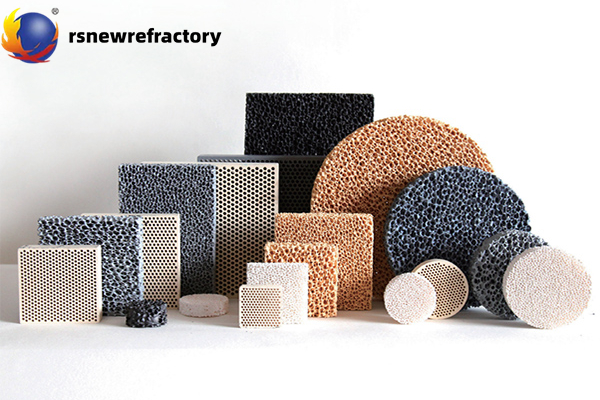
Application of ceramic foam filters
Heat-resistant and chemical-resistant filter material
In the metallurgical industry, when casting aluminum, cupru, and other alloys, foam ceramics can be used as a filter material to remove oxidized ash. Foam ceramic filter plates can be used in sand molds and metal molds, and can be placed horizontally or vertically. MgO-ZrO2-Al2O foam ceramics can also be used to filter industrial pure iron, bearing steel, and high-temperature alloys.
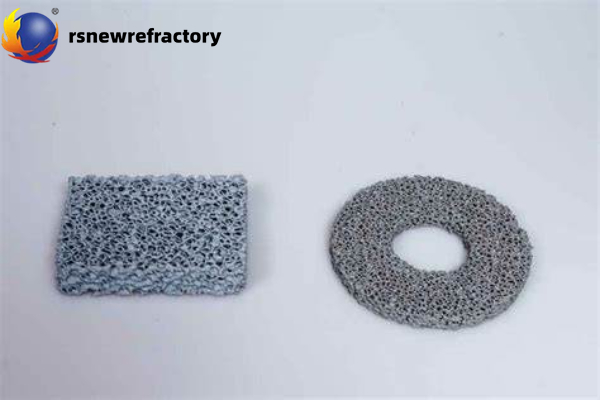
High-temperature gas filtration
Heat-resistant foam ceramics are used to filter gases. They can be placed before the catalyst carrier to filter out dust in the exhaust gas. Prin urmare, it can be used in gas absorption towers, contact reaction towers, degassing towers, and carbonization towers in chemical reactions; it can also be used as a catalyst carrier for precious metals such as palladium, platinum, ruthenium, and nickel. It can be used as a biological enzyme carrier in the food and pharmaceutical industries and has a wide range of uses. în plus, it can also be used as a radiation energy heat transfer converter, gas distribution material, self-preheating burner regenerator, insulation and heat storage material, mixer, agitator, etc.
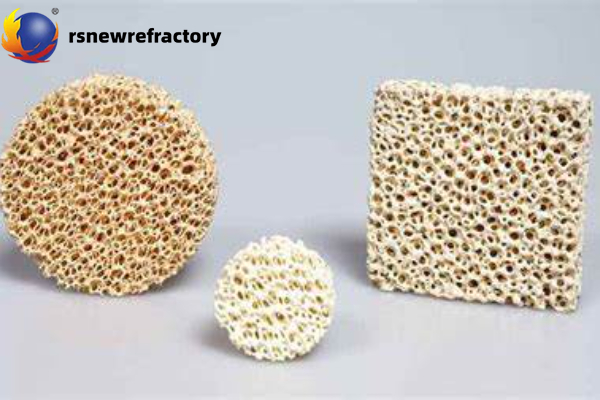
WeChat
Scanați codul QR cu wechat