Introdução ao processo de produção de tijolos refratários de argila
O tijolo refratário de argila é um material refratário comumente usado, amplamente utilizado em fornos industriais de alta temperatura, como aço, vidro, cimento, e cerâmica. Possui excelente resistência ao choque térmico, resistência a altas temperaturas, e estabilidade química. Este artigo apresentará detalhadamente o processo de produção de tijolos refratários de argila para ajudar todos a entender melhor este importante material refratário..
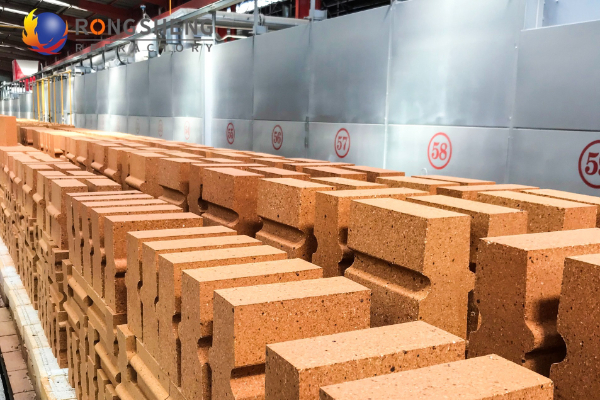
Processo de produção de tijolos refratários de argila
① Preparação de matéria-prima
Principalmente a preparação de clínquer e a preparação de argila de ligação. A preparação do clínquer consiste em calcinar a matéria-prima da argila refratária em alta temperatura em clínquer, e depois esmague, tela, e pulverizá-lo em vários níveis de materiais granulares e pó fino. A preparação da argila adesiva consiste em esmagar, seco, pulverizar finamente, e misture a argila. O clínquer argiloso é triturado grosseiramente em blocos com menos de 50 mm e depois triturado em vários níveis de agregados de 5-2 mm.. O material peneirado entra na máquina para ser moído em pó fino com menos de 0,5 mm. A argila de ligação é geralmente seca, e depois esmagado grosseiramente, pulverizado, e finamente pulverizado em pó fino inferior a 0,5 mm, ou misturado com clínquer para fazer pó fino.
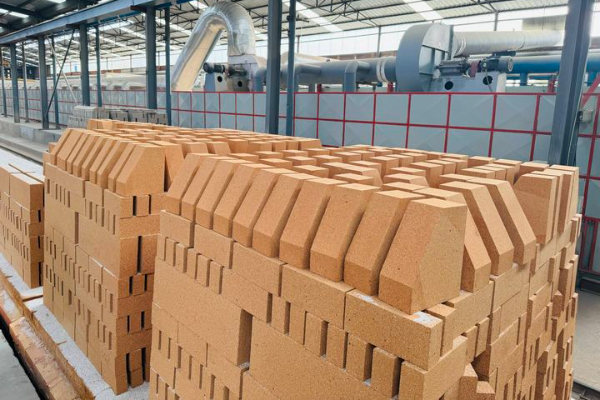
② Dosagem e mistura
Lote, misturando, e moldagem: O clínquer de argila refratária calcinado é usado como material magro, e uma certa proporção de argila ligante é adicionada para fazer uma mistura. O clínquer representa uma elevada proporção da mistura, que é chamado de produto multi-clínquer. Este tipo de produto possui alta estabilidade de volume e outras boas propriedades, mas precisa ser fortemente moldado. Atualmente, os tijolos multiclínquer são os produtos mais produzidos e utilizados. A mistura é moldada após a mistura ou após ser retida e depois misturada. Existem muitos métodos de moldagem, mas o método de moldagem por prensagem semisseca é atualmente usado para produtos multiclínquer. A pressão de moldagem tem impacto na densidade, resistência estrutural, e resistência à escória dos tijolos.
A proporção de lama inclui a proporção de massa e a proporção de partículas entre o clínquer, argila aglutinante, água, e aditivos. A quantidade de argila ligante e água adicionada varia de acordo com o método de moldagem. A proporção de moldagem de plástico é: clínquer: argila é (7-5): (3-5), e o teor de água é 16%-20%; a proporção de moldagem semi-seca é: clínquer: argila é (9-7): (1-3), e o teor de água é 3.5%-8.0%. Vários materiais granulares são adicionados ao equipamento de mistura em sequência, e vários ligantes são adicionados para fazer uma lama uniforme.
③ Secagem de tijolos de argila
O teor de umidade dos blocos de tijolos de argila seca varia dependendo do método de moldagem. A moldagem por prensagem semi-seca apresenta baixo teor de umidade nas peças brutas. Quando a umidade evapora, quase não há encolhimento. Pode ser seco rapidamente ou carregado diretamente no forno. Blocos de tijolos com alto teor de umidade podem ser secos antecipadamente por secagem com ar natural apropriado ou aquecimento com ar quente e depois enviados para o forno de túnel. O fator chave no controle do processo de secagem é a velocidade de secagem. O princípio deve ser garantir que os espaços em branco não se deformem, rachadura, e tem uma certa força. O teor de umidade das peças que finalmente entram no forno de queima é controlado para ficar abaixo 2%.
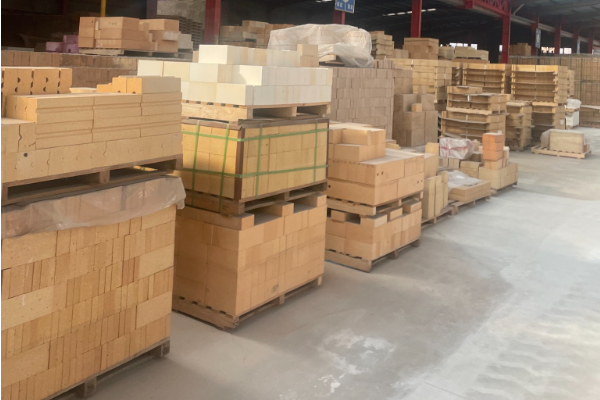
④ Queima de tijolos de barro
O objetivo da queima é sinterizar os tijolos para dar-lhes certas dimensões, porosidade e densidade, alta resistência mecânica, boa estabilidade de volume, e boa resistência ao fogo. Durante o processo de queima, a matriz dos tijolos sofre uma série de alterações físicas e químicas, e várias reações são realizadas na corrente descendente ou no túnel. O processo de queima é dividido em quatro etapas.
- Quando a temperatura atinge 200 ℃, a temperatura não deve ser elevada muito rapidamente para evitar que o corpo verde rache. Ao queimar em um forno de túnel, a temperatura do primeiro 4 os lugares de estacionamento não devem exceder os 200°C.
b.200-900℃ O aumento da temperatura deve ser acelerado nesta fase para facilitar a reação química da matéria orgânica e impurezas no tarugo. Durante o período de 600-900℃, uma forte atmosfera oxidante deve ser mantida no forno para evitar o aparecimento de “núcleo preto” resíduos de tijolos. - 900-1380℃: (O aumento da temperatura deve ser estável durante o estágio de alta temperatura, e a atmosfera de oxidação deve ser mantida para garantir que o corpo do tijolo seja aquecido uniformemente e para evitar rachaduras no corpo do tijolo. Porque em altas temperaturas acima de 1100℃, o encolhimento de sinterização é muito forte, e a taxa de encolhimento atinge 5%, por isso é muito importante manter o gradiente de temperatura suave e eliminar o estresse interno.
- A temperatura de combate ao fogo dos tijolos de argila é geralmente 100-150°C mais alta que a temperatura de sinterização. Se a faixa de temperatura de sinterização da argila sinterizada utilizada for estreita, a temperatura de extinção de incêndio deve ser mais baixa, cerca de 50-100°C é mais adequado. A temperatura de queima dos produtos de argila Deve-se garantir que a argila ligante esteja totalmente amolecida para que possa reagir totalmente com o pó fino de clínquer e a camada superficial de partículas grossas para atingir o objetivo de unir as partículas de clínquer e fazer com que o produto obtenha resistência adequada e estabilidade de volume. A temperatura de queima é geralmente 1250-1350℃. Se o conteúdo do A1203 for alto, a temperatura de queima do produto deve ser aumentada adequadamente, cerca de 1350-1380°C, e o tempo de preservação do calor de queima é geralmente 2-10 horas para garantir que a reação no produto seja suficiente e que as qualidades superficiais e internas do produto sejam consistentes.
- Durante a fase de resfriamento, de acordo com as mudanças na estrutura do produto na seção de resfriamento, a temperatura deve ser aumentada rapidamente em altas temperaturas acima de 1000°C, e a taxa de resfriamento deve ser retardada em 1000-800°C. Na verdade, na produção real, a taxa de resfriamento efetivamente adotada não causará o risco de trincas a frio do produto.
WeChat
Escaneie o código QR com o wechat