Zircon brick is a refractory product made of zircon as raw material and soft clay as a binder.
Zircon brick production process
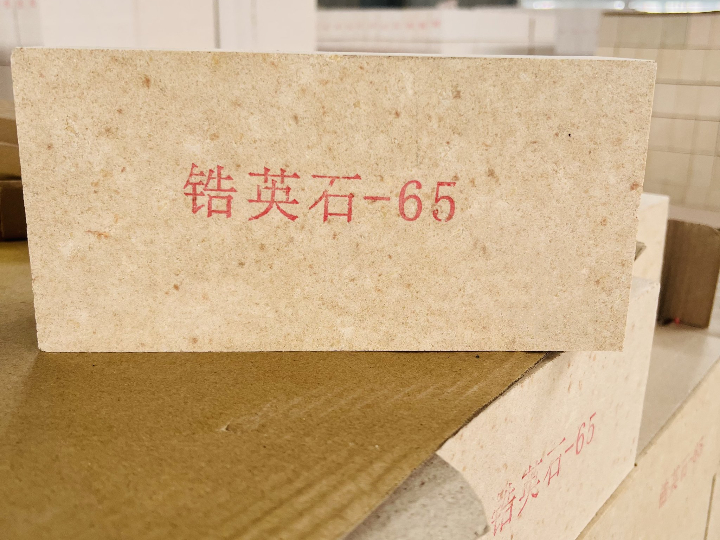
After the zircon sand is pulverized, it is made into agglomerates, and after being calcined, it is pulverized into a suitable particle size. After batching → mixing → trapping → high-pressure molding → drying → high-temperature firing.
Physical and chemical indicators of zircon bricks
Item | Index |
ZrO2 % | ≥65 |
SiO2 % | ≤33 |
Fe2O3 % | ≤0.2 |
TiO2 % | ≤1.2 |
Bulk Density g/cm3 | ≥3.8 |
Apparent Porosity % | ≤17 |
Cold Crushing Strength MPa | ≥120 |
0.2Mpa Refractoriness Under Load ℃ | ≥1700 |
Thermal shock resistance cycle 1100℃water cooling | >10 |
Product features of zircon bricks
- High-temperature resistance, high-strength
- Strong anti-strike ability, anti-washing, and erosion of molten steel and glass solution
- Low thermal expansion rate, stable volume at high temperature
- Good thermal shock resistance
- High bulk density, low porosity, and strong permeability resistance
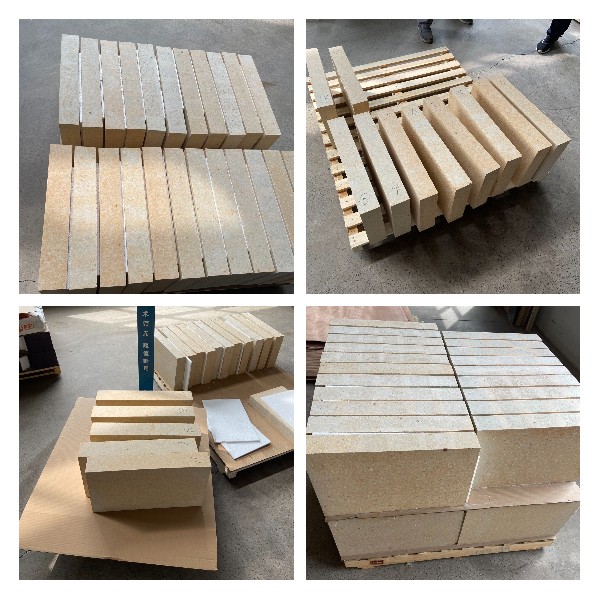
Application of zircon brick
- Masonry steel drum lining for degassing, stainless steel drum lining, continuous casting steel drum lining, sprue brick, plug brick, and high-temperature induction furnace lining.
- For parts that contact glass solution.
- Zircon bricks have the property of not being corroded by metal chromium, aluminum oxides, and their slag. Can be used in the bottom of a furnace.
Shipping about zircon brick
Zircon bricks are packaged on wooden pallets before transportation, and the factory delivery time is generally 7-12 days, and customized products will take a little longer time.
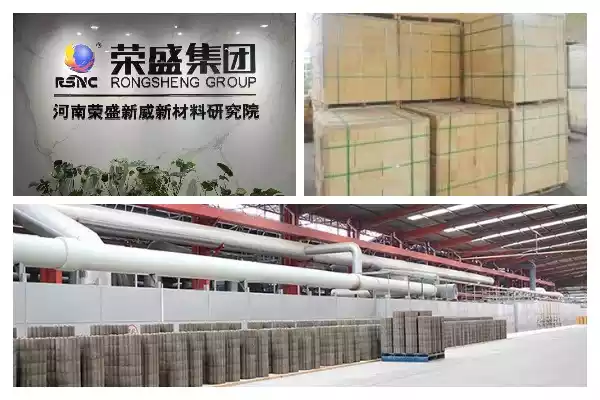
Why choose us?
The factory has been established for 20 years and has 20 senior refractory engineers. The factory can provide a complete set of refractory materials for refractory kilns. The factory produces 80,000 tons of shaped refractory materials and 50,000 tons of unshaped refractory materials yearly.
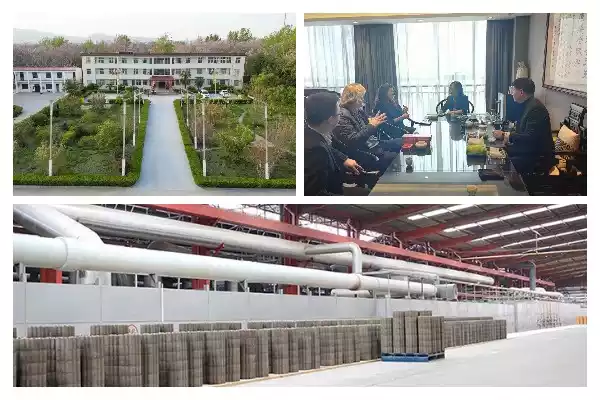
WeChat
Scan the QR Code with wechat