The basic method for the synthesis of magnesia-aluminum spinel
Magnesia-aluminum spinel (MgAl2O4), also known as spinel, is an important inorganic compound that generally has a high melting point, excellent thermal stability, and mechanical strength. It can be prepared through different synthetic methods, the following are some common ones:
Preparation of magnesium aluminum spinel
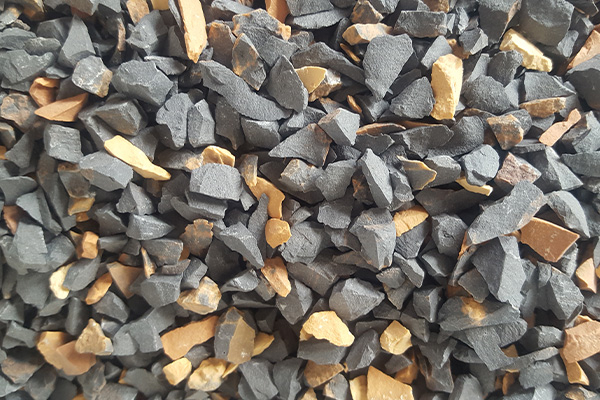
Momenteel, spinel which can be used as a raw material for refractory materials must be obtained through a synthetic method. The main synthetic methods are sintering and electric fusion. The raw materials are high-purity alumina and chemical-grade magnesium oxide.
Preparation of spinel by sintering method
The advantage of the sintering method is that the process is a continuous ceramicization process, which can control the feeding speed and maintain a uniform temperature distribution in the kiln. Daarom, the products produced are very homogeneous, with a grain size between 30-80 μm and a porosity. Lower (<3°%).
Preparation of spinel by electrofusion method
The electrofusion method is an intermittent operation process. The raw materials must be sorted and homogenized in advance before operation because if the raw material block is too large, the cooling time needs to be extended. At this time, the microstructure will be uneven during the cooling process, and If the cooling rate is too fast, the spinel crystal will be smaller on the outside than on the inside, and a large collection of low-melting-point impurities will accumulate in the center.
Characteristics of magnesium aluminum spinel
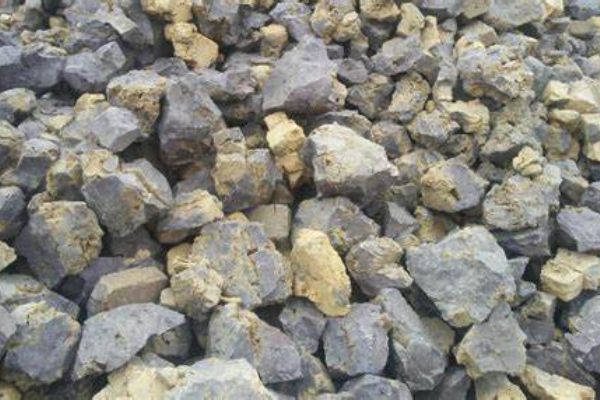
Magnesia-aluminum spinel has high slag corrosion resistance, weerstand tegen thermische schokken, and high temperature and compressive strength. High-quality pre-synthesized spinel provides new raw materials for the production of amorphous and shaped high-purity refractory materials. Daarom, Has been widely used.
Magnesia-aluminum spinel refractory castable
Magnesium-aluminum spinel-containing vuurvaste gietstukken are formulated from corundum, magnesia, high-alumina bauxite, and synthetic magnesia-aluminum spinel aggregates and powders. Due to the existence and generation of spinel, expansion, and micro-cracks will occur, thereby buffering the thermal stress generated in the material. Daarom, it has good resistance to slag erosion and thermal shock. Tegelijkertijd, the spinel phase can wrap the periclase And improve the hydration resistance.
WeChat
Scan de QR-code met wechat