Silicon carbide mullite bricks are fired bricks composed of mullite (3Al2O3.2SiO2) en siliciumcarbide (SiC) als de belangrijkste mineralen. Silica-mullite brick has the high-temperature resistance of mullite and the wear resistance, corrosieweerstand, and good thermal conductivity of silicium carbide.
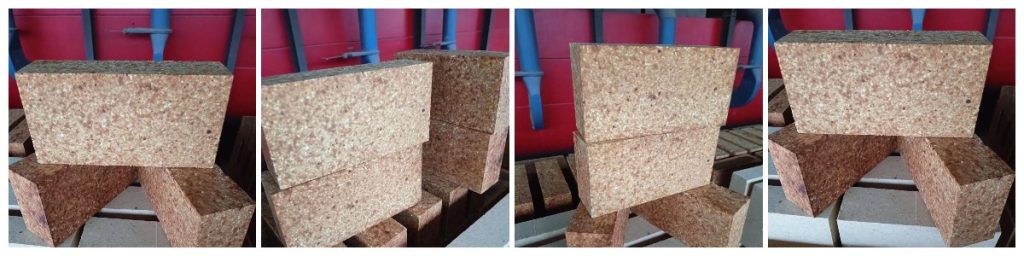
Physical and chemical indicators of silica mullite refractory brick
Product | AZM-1650 | AZM-1680 | |
Chemische samenstelling | SiC+SiO2 | ≥30 | ≥32 |
Al2O3 | ≥65 | ≥65 | |
Bulkdichtheid(g/cm3) | ≥2,65 | ≥2.70 | |
Schijnbare porositeit (%) | ≤19 | ≤19 | |
Koude verpletterende sterkte(MPa) | ≥90 | ≥100 | |
Refractoriness Under Load | ≥1650 | ≥1680 | |
Bestand tegen thermische schokken | ≥15 | ≥20 |
The main uses of silicon carbide mullite brick
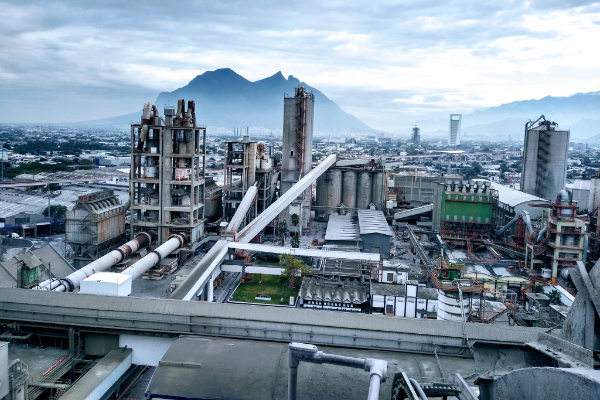
It is suitable for the transition zone, preheating zone, tertiary air duct, five-stage preheater, and lime kiln discharge chute of cement rotary kiln.
Comparison of silicon mullite brick and magnesia-alumina spinel bricks
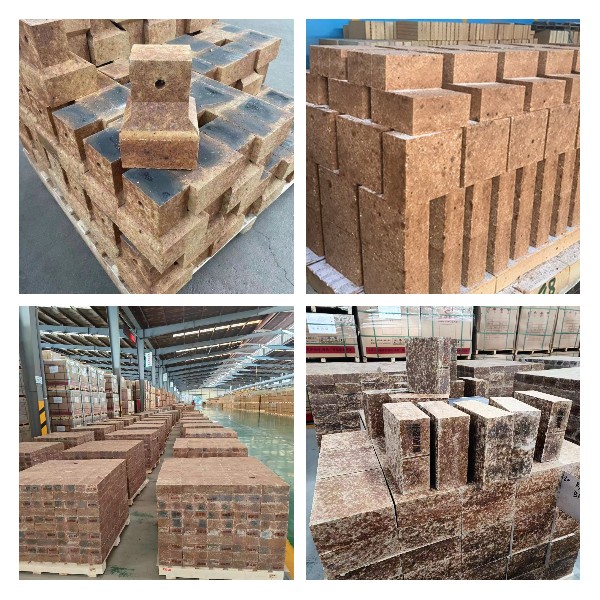
Silica mullite refractory bricks are suitable for the transition zone of cement kilns as well as magnesia-alumina spinel bricks. Compared with magnesia-alumina spinel bricks, they have a higher cost performance. Compared with magnesia-alumina spinel bricks, silicon mullite bricks have the advantages of low thermal conductivity, goede thermische schokstabiliteit, and high cost performance.
Compared with silicon carbide mullite bricks, magnesia-alumina spinel bricks have the advantage of stronger corrosion resistance and the disadvantage of high thermal conductivity. In the system of waste cement rotary kiln processing, magnesia-alumina spinel bricks have better alkali-sulfur corrosion resistance. , so in large-scale rotary kilns, magnesium-alumina spinel bricks are still mostly used for masonry due to safety factors.
WeChat
Scan de QR-code met wechat