Introductie van het productieproces van kleivuurstenen
Kleisteen is een veelgebruikt vuurvast materiaal, veel gebruikt in industriële ovens op hoge temperatuur, zoals staal, glas, cement, en keramiek. Het heeft een uitstekende thermische schokbestendigheid, sterkte bij hoge temperaturen, en chemische stabiliteit. Dit artikel introduceert het productieproces van vuurvaste bakstenen in detail om iedereen te helpen dit belangrijke vuurvaste materiaal beter te begrijpen.
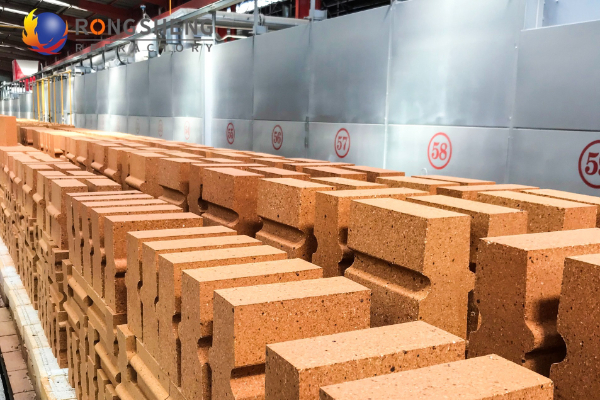
Productieproces van kleivuurstenen
① Voorbereiding van grondstoffen
Voornamelijk de bereiding van klinker en de bereiding van hechtklei. De bereiding van klinker bestaat uit het calcineren van de vuurvaste kleigrondstof bij hoge temperatuur tot klinker, en dan verpletteren, scherm, en verpulver het tot verschillende niveaus van korrelige materialen en fijn poeder. De bereiding van hechtklei is vermalen, droog, fijn verpulveren, en maak een slurry van de klei. De kleiklinker wordt grof gemalen tot blokken van minder dan 50 mm en vervolgens vermalen tot verschillende niveaus van aggregaten van 5-2 mm. Het gezeefde materiaal komt de machine binnen en wordt vermalen tot fijn poeder van minder dan 0,5 mm. De hechtklei wordt doorgaans gedroogd, en daarna grof gemalen, verpulverd, en fijn verpulverd tot fijn poeder van minder dan 0,5 mm, of gemengd met klinker om fijn poeder te maken.
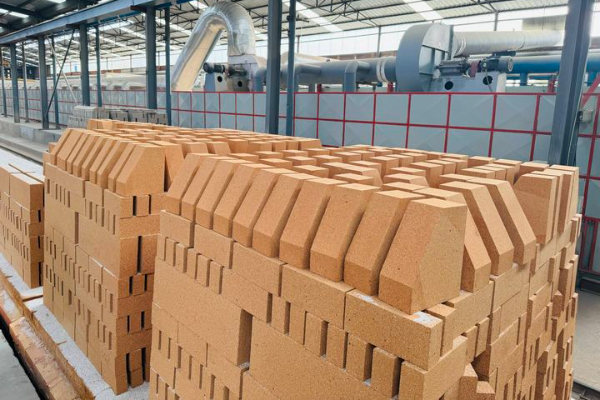
② Baten en mengen
Batchen, mengen, en gieten: Als mager materiaal wordt de gecalcineerde vuurvaste kleiklinker gebruikt, en een bepaalde hoeveelheid bindklei wordt toegevoegd om een mengsel te maken. De klinker maakt een groot deel uit van het mengsel, dat een multiklinkerproduct wordt genoemd. Dit soort product heeft een hoge volumestabiliteit en andere goede eigenschappen, maar het moet sterk worden gevormd. Momenteel, multiklinkerstenen zijn de meest geproduceerde en gebruikte producten. Het mengsel wordt na het mengen of na opsluiting gevormd en vervolgens gemengd. Er zijn veel vormmethoden, maar de semi-droge persvormmethode wordt momenteel gebruikt voor multiklinkerproducten. De vormdruk heeft invloed op de dichtheid, structurele sterkte, en slakweerstand van de stenen.
Het aandeel modder omvat de massaverhouding en deeltjesverhouding tussen klinker, bindmiddel klei, water, en additieven. De toegevoegde hoeveelheid bindmiddelklei en water varieert afhankelijk van de vormmethode. De verhouding tussen kunststof gieten is: klinker: klei is (7-5): (3-5), en het watergehalte is 16%-20%; de verhouding van semi-droog vormen is: klinker: klei is (9-7): (1-3), en het watergehalte is 3.5%-8.0%. Verschillende korrelige materialen worden achtereenvolgens aan de mengapparatuur toegevoegd, en er worden verschillende bindmiddelen toegevoegd om een uniforme modder te maken.
③ Drogen van vuurvaste bakstenen
Het vochtgehalte van gedroogde kleistenen plano's varieert afhankelijk van de vormmethode. Halfdroog persgieten heeft een laag vochtgehalte in de plano's. Wanneer het vocht verdampt, er is vrijwel geen krimp. Het kan snel worden gedroogd of direct in de oven worden geladen. Bakstenen plano's met een hoog vochtgehalte kunnen vooraf worden gedroogd door geschikte natuurlijke luchtdroging of heteluchtverwarming en vervolgens naar de tunneloven worden gestuurd. De belangrijkste factor bij het beheersen van het droogproces is de droogsnelheid. Het principe moet zijn ervoor te zorgen dat de plano's niet vervormen, scheur, en een bepaalde kracht hebben. Het vochtgehalte van de plano's die uiteindelijk de stookoven binnenkomen, wordt zo laag mogelijk gehouden 2%.
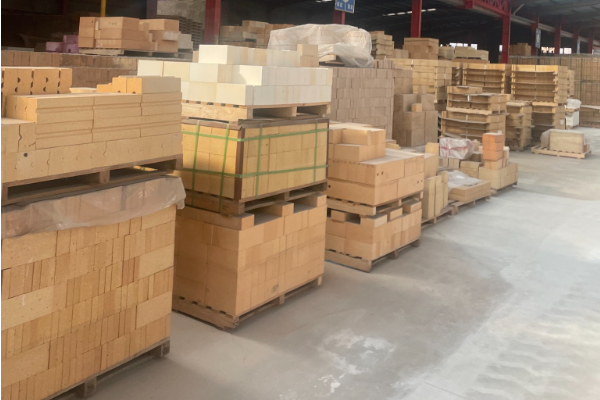
④ Bakstenen bakken
Het doel van het bakken is om de stenen te sinteren om ze bepaalde afmetingen te geven, porositeit en dichtheid, hoge mechanische sterkte, goede volumestabiliteit, en goede brandwerendheid. Tijdens het bakproces, de matrix van de stenen ondergaat een reeks fysische en chemische veranderingen, en verschillende reacties worden uitgevoerd in de valstroom of tunnel. Het bakproces is grofweg verdeeld in vier fasen.
- Wanneer de temperatuur 200℃ bereikt, de temperatuur mag niet te snel worden verhoogd om te voorkomen dat het groene lichaam barst. Bij het stoken in een tunneloven, de temperatuur van de eerste 4 Parkeerplaatsen mogen de temperatuur van 200°C niet overschrijden.
b.200-900℃ De temperatuurstijging moet in dit stadium worden versneld om de chemische reactie van organisch materiaal en onzuiverheden in de knuppel te vergemakkelijken. Tijdens de periode van 600-900℃, In de oven moet een sterk oxiderende atmosfeer worden gehandhaafd om de schijn van verontreiniging te voorkomen “zwarte kern” afvalstenen. - 900-1380℃: (De temperatuurstijging moet stabiel zijn tijdens de hoge temperatuurfase, en de oxidatieatmosfeer moet worden gehandhaafd om ervoor te zorgen dat het baksteenlichaam gelijkmatig wordt verwarmd en om scheuren in het baksteenlichaam te voorkomen. Want bij hoge temperaturen boven de 1100℃, de sinterkrimp is zeer sterk, en de krimp bereikt 5%, het is dus erg belangrijk om de temperatuurgradiënt zacht te houden en interne stress te elimineren.
- De brandwerende temperatuur van bakstenen is over het algemeen 100-150 ℃ hoger dan de sintertemperatuur. Als het sintertemperatuurbereik van de gebruikte gesinterde klei smal is, de brandwerende temperatuur moet lager zijn, rond 50-100℃ is geschikter. De baktemperatuur van kleiproducten Er moet voor worden gezorgd dat de bindende klei volledig verzacht is, zodat deze volledig kan reageren met het fijne poeder van de klinker en de oppervlaktelaag met grove deeltjes om het doel van het binden van de klinkerdeeltjes te bereiken en ervoor te zorgen dat het product de juiste sterkte en sterkte verkrijgt. volumestabiliteit. De baktemperatuur is over het algemeen 1250-1350℃. Als het A1203-gehalte hoog is, de baktemperatuur van het product moet op passende wijze worden verhoogd, ongeveer 1350-1380°C, en de conserveringstijd van de bakwarmte is over het algemeen 2-10 uur om ervoor te zorgen dat de reactie in het product voldoende is en dat de oppervlakte- en innerlijke eigenschappen van het product consistent zijn.
- Tijdens de afkoelfase, volgens de roosterveranderingen van het product in de koelsectie, bij hoge temperaturen boven 1000°C moet de temperatuur snel worden verhoogd, en de afkoelsnelheid moet worden verlaagd tot 1000-800 °C. In werkelijkheid, bij de daadwerkelijke productie, de daadwerkelijk toegepaste afkoelsnelheid zal geen risico op koudescheuren van het product met zich meebrengen.
WeChat
Scan de QR-code met wechat