Spesifikasi untuk menetapkan sendi pengembangan dalam Pembinaan Castable Refraktori Relau
Everyone knows that expansion joints are reserved during the construction of refractory brick masonry. So does the furnace refractory castable also have expansion joints? How do you reserve the appropriate expansion joints for castables tahan api? What size of expansion joints should be reserved for what kind of castables? Do you know these? If no expansion joints are reserved, how will it impact later use?
When refractory bricks or castables are used for the lining of industrial kilns, the lining structure will deform and expand due to the influence of thermal stress caused by temperature changes and temperature gradients. Oleh itu, expansion joints must be left during the construction of refractory bricks and castables.
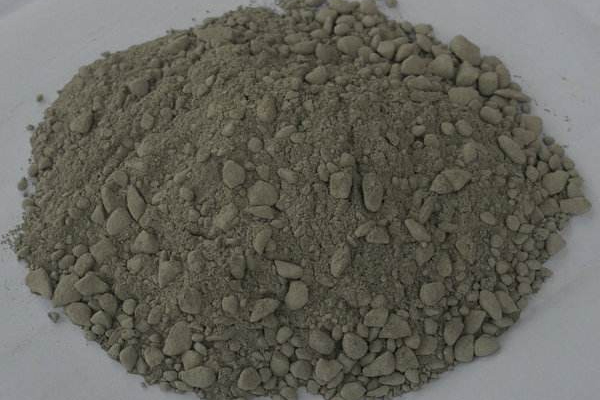
Refractory bricks and castables are made of different raw materials, and their expansion coefficients after heating are also different. The size of the expansion during masonry is mainly determined by the properties of the refractory bricks or castables used and the temperature they are subjected to.
Forms of expansion joints of furnace refractory castable
There are two types of expansion joints in refractory castables: through joints and non-through joints. As shown in the figure, a, b-through expansion joints; c-non-through expansion joints.
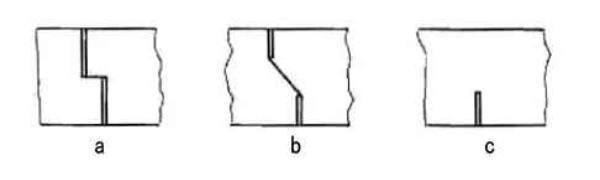
Expansion joints
The arrangement of expansion joints of refractory castables mainly involves selecting the spacing, width, and form of the expansion joints. The distance between the expansion joints of the furnace body assembled from prefabricated parts and the furnace body cast on site is different.
① For furnace bodies assembled with prefabricated components, if the furnace body is short, there is no need to leave additional expansion joints between the prefabricated parts, and only appropriate gaps need to be left at both ends of the furnace body; if the furnace body is long, an expansion joint can be left every 5 to 10 meters along the length of the furnace body according to the temperature of each section of the furnace body, and the joints are filled with ceramic fiber ropes soaked in clay slurry to prevent smoke and fire from emitting outwards at low and medium temperatures in the furnace.
② Furnace bodies cast on site. The spacing and width of expansion joints for furnace bodies of refractory castables cast on site. The values in the table are applicable to clay and high-alumina refractory castables.
③Fixing of fillers. The materials of the expansion joints in the refractory castables should be fixed in place before pouring or carefully filled during pouring. When pouring in blocks, the refractory castables should be divided into several blocks according to their expansion joints. The molds should be used to separate and pour from the expansion joints, and the joint fillers should be embedded after the initial setting.a:δ=3~4mm b:δ=5mm
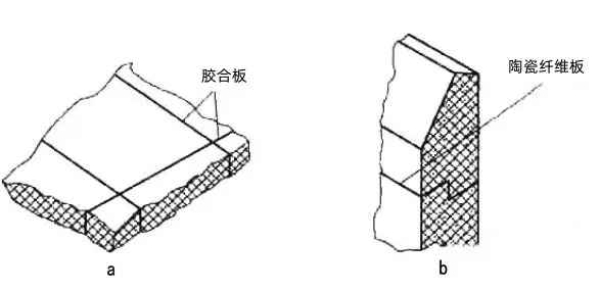
④ Prevent displacement. In order to prevent the expansion joint filler from displacement or local adhesion of refractory castables, the filler layer should be accurately cut and laid tightly. If necessary, nails can be nailed into the castable to stabilize the filler layer.
⑤ Isolation measures. When the filler layer is separated in a cold state and in contact with a hot state under the construction environment, itu dia, it becomes a sliding surface, it is advisable to add an isolation layer to prevent the filler from displacement, prevent leakage from adhesion or block the expansion gap.
Allowable error of expansion joints
(1) The verticality error of vertical expansion joints is allowed to be no more than 2mm per meter in height and no more than 15mm in total height.
(2) The horizontality error of horizontal expansion joints is allowed to be no more than 2.5mm per meter and no more than 15mm in total length.
(3) The error of expansion joints of power station boilers is allowed to be 3~4mm.
(4) The width error of expansion joints is as follows
(5) All types of refractory castables cast on site should be provided with expansion joints as specified in the design drawings. The width error is +3mm and shall not be less than the specified width.
Precautions for construction of expansion joints of furnace refractory castable
When constructing the furnace bottom, the expansion joints of refractory bricks or castables should be staggered in the upper and lower brick layers and the furnace bottom of the same layer. When building the furnace wall, the expansion joints left between the inner and outer layers and the upper and lower layers can also be staggered. When constructing the circular wall, a gap should be left between the outer shells to compensate for expansion.
In the construction of the arch, the expansion joints of refractory bricks and castables should be left straight at both ends. When leaving, consider the longitudinal expansion of the arch and the upward expansion of the furnace wall. When the length of the arch is greater than 5 meters, in addition to leaving expansion joints at both ends, expansion joints should be left in the middle of the arch according to the segmentation of the arch length, and the expansion joints of the staggered arch should be left straight.
The expansion joints of each layer of the multi-layer arch should be staggered, and the expansion joints should be covered with a layer of flat bricks. If it is a dry-laid arch of silica bricks, 1-2mm cardboard should be inserted into the radial joints of the arch every 3-5 bricks to compensate for expansion.
WeChat
Imbas Kod QR dengan wechat