He aha te mahinga o nga pereki ahi alumina?
High alumina refractory bricks are mainly used for masonry linings of blast furnaces, hot blast stoves, electric furnace roofs, oumu pupuhi, reverberatory furnaces, and rotary kilns. The demand for alumina fire bricks is very high. The following is the specific production process of high alumina refractory bricks.
Alumina fire bricks production process
The following is about the production process of refractory materials: raw material preparation→material mix→forming→dry→sintering→cooling and QA→packaging and storage.
Raw material preparation
Choose high-purity alumina (Ko Al2O3) powder as the main raw material. According to the need, some auxiliary materials may be added, such as clay, quartz sand, silica sand, etc. The selection and ratio of raw materials will affect the performance of the final product.
Material mix
Mix high-purity alumina powder and auxiliary materials in a certain proportion to ensure that various components are evenly distributed. The mixing process can be carried out by dry mixing or wet mixing.
Forming
The mixed raw materials are molded by a molding machine. Common molding methods include extrusion molding, compression molding, and injection molding. By shaping, adobes of the desired size and shape can be obtained.
Dry
The shaped bricks need to be dried to remove the moisture therein. It is usually dried naturally or heated in an oven.
Sintering
The dried bricks are put into a high-temperature furnace for sintering. The sintering temperature is generally above 1500°C, and the adobe undergoes particle bonding, grain growth, and densification at high temperatures. This allows the alumina powder in the adobe to undergo a chemical reaction to form a high-temperature stable mineral phase.
Cooling and QA
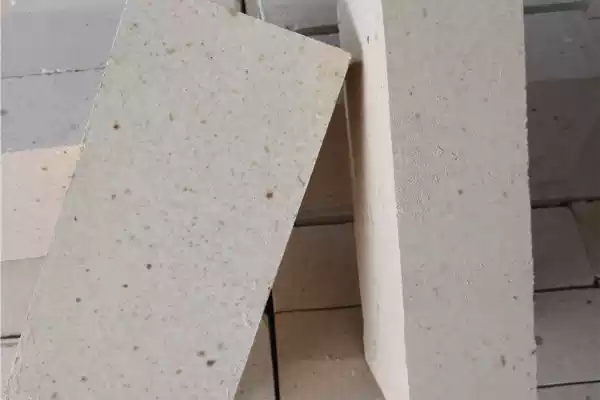
After sintering, the adobe needs to go through a cooling process. Quality inspection is then carried out, including visual inspection, size inspection, chemical composition analysis, etc. The purpose of quality inspection is to ensure that the product meets the specified standards and requirements.
Packaging and storage
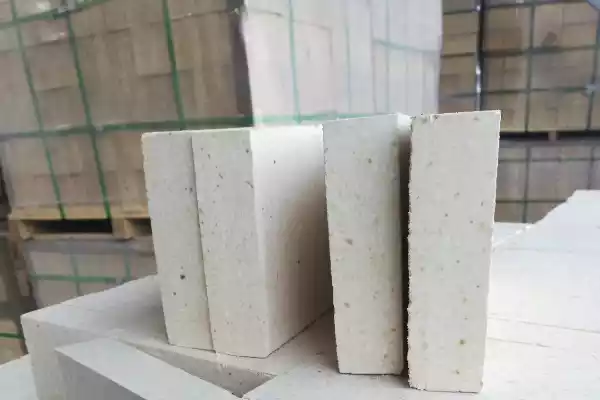
The high alumina bricks are protected by packaging, and common packaging methods include wooden boxes, pallets, etc. During storage and transportation, care should be taken to avoid high alumina bricks from moisture, vibration, and other mechanical damage.
What factors are related to the refractory temperature of high alumina bricks?
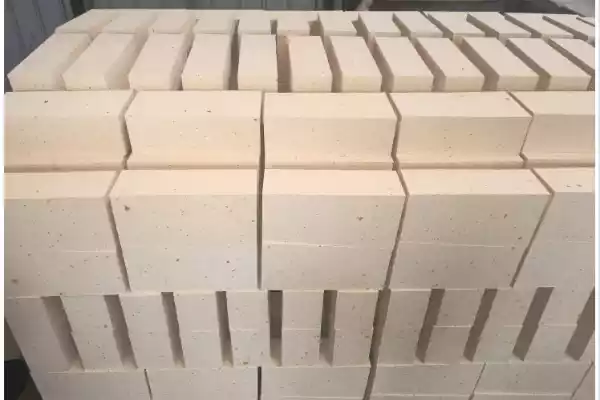
The refractoriness of high alumina bricks fluctuates widely, generally at 1770-2000°C, mainly affected by the AlO content, and increases with the increase of AlO content in the product. I taua wa ano, the refractoriness is also affected by the content and type of impurities and is related to the mineral phase structure of the product.
WeChat
Matawai te Waehere QR me te wechat