He Whakaaturanga Poto mo te Hanganga me te Mahinga o te Steel Ladle refractory
The steel ladle refractory is also called the ladle refractory lining, which is used to hold molten steel. Molten steel is also subjected to refining and other process operations in the ladle. The steel ladle is composed of three parts: the outer shell, the lining, and the injection control mechanism.
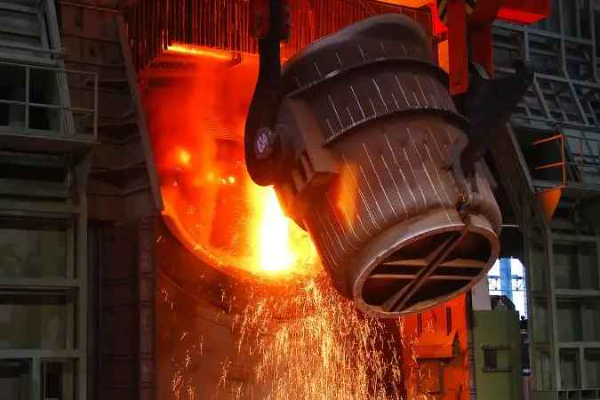
Steel ladle refractory structure
The ladle shell is welded from boiler steel plates, and the thickness of the barrel wall and barrel bottom steel plates is about 14~30mm and 24~40mm. To ensure the smooth removal of baking moisture, 8~10mm small holes are drilled into the ladle shell. I tua atu, reinforcing ribs and reinforcing hoops are welded on the waist of the ladle shell.
Introduction to the ladle refractory Lining
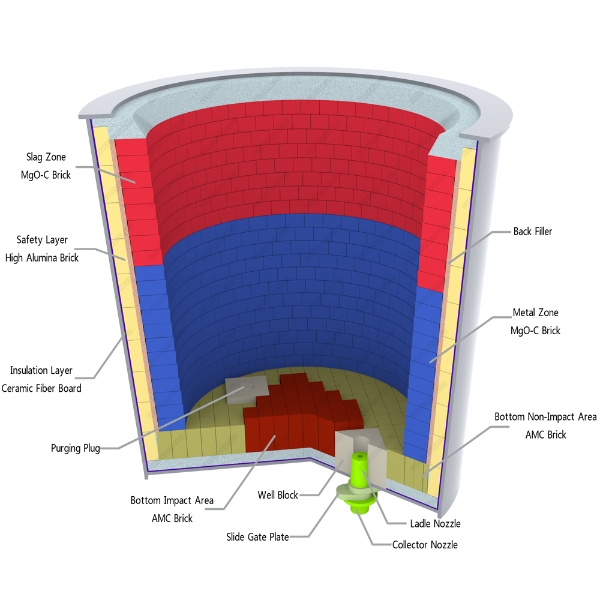
The lining of the ladle is composed of an insulation layer, a permanent layer, and a working layer. The insulation layer is close to the steel plate and is about 10~15mm thick. It is mainly used to reduce heat loss and is often built with asbestos boards: In order to prevent the molten steel from burning through the ladle, there is also a permanent layer inside the insulation layer, which is about 30~60mm thick. This layer is built with pereki uku a pereki teitei-konumohe; the working layer of the ladle is in direct contact with the molten steel and slag. It will be directly subjected to mechanical scouring rapid cooling and heating and is prone to peeling. The life of the ladle is related to the quality of this layer. This layer is usually built in a comprehensive way, ara, the bottom of the ladle is made of wax bricks or high-alumina bricks, the wall of the ladle is made of high-alumina bricks and aluminum-carbon bricks, and the slag line is often made of magnesium-carbon bricks.
Steel ladle molten steel control system
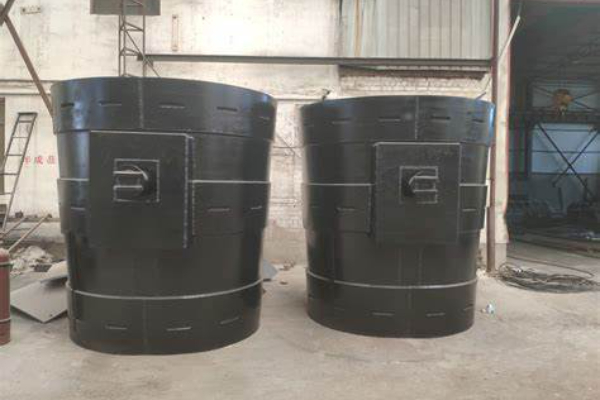
The opening of the sliding nozzle of the ladle is used to control the size of the steel flow and the height of the liquid level of the tundish. The sliding nozzle consists of an upper nozzle, an upper slide plate, a lower nozzle, and a lower slide plate. During operation, the movement of the lower slide plate can be used to adjust the overlap of the upper and lower injection holes and thus control the size of the injection flow. There are two ways to adjust it, namely hydraulic and manual. Since the sliding nozzle has to withstand the scouring of high-temperature slag, the static pressure of molten steel, and the effects of rapid cooling and heating, the refractory material is required to be resistant to high temperature, scouring, rapid cooling and heating, and have good slag resistance, and have sufficient high-temperature strength. I tenei wa, the most commonly used materials are high-aluminum, magnesium, magnesium-aluminum composites, etc., and there are also slide plates that are soaked in asphalt to increase the service life of the slide plate.
The upper nozzle is located between the ladle and the tundish. During production, there is a set of special long nozzle installation devices on-site to hang it on the lower nozzle, to prevent the injection flow between the ladle and the tundish from being secondary oxidation, at the same time, it can also avoid the splashing of the injection flow and the slag rolling problem of open casting. The materials of the long nozzle are mainly fused quartz and alumina carbon.
WeChat
Matawai te Waehere QR me te wechat