Characteristics of magnesium calcium iron ramming mass
The dry ramming material of the magnesium electric furnace bottom is composed of MgO as the main crystal phase and Fe2O3 as the sintering agent. At high temperatures, the main crystal phase and the binding phase diffuse through the grain boundary and undergo solid solution reaction to form some high melting point phases, thus forming a hard shell on the surface of the furnace bottom – the sintering layer.
During the sintering process, Fe2O3 reacts with free CaO (f-CaO) to form 2CaO·Fe2O3 (melting point 1436℃), and the raw materials usually contain a small amount of impurities such as SiO2 and Al2O3; SiO2 reacts with f-CaO to form C2S and C3S; Fe2O3 and Al2O3 react with f-CaO to form C4AF (melting point 1415℃) and C2F. These two phases have low melting points and promote the sintering of dry ramming materials.
When the molten pool is sintered, the mixture containing C2F and C4AF can play a sintering role and form a ceramic bond as soon as possible. As the power-on time increases, the temperature increases, and the hard shell becomes thicker and thicker. When the sintered layer reaches a certain thickness, the furnace bottom and furnace slope will have very high strength, good anti-penetration ability, erosion resistance, and scouring resistance.
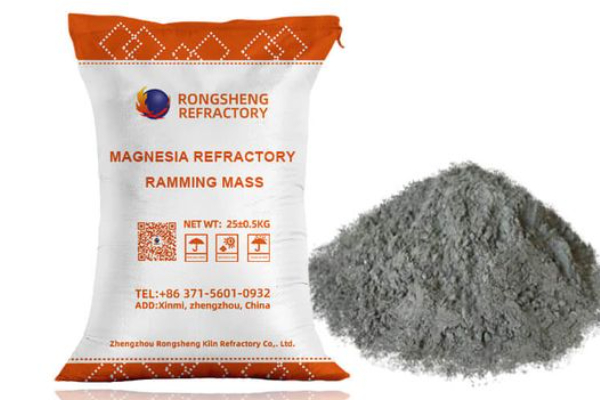
Characteristics of magnesium calcium iron ramming material
Since the main minerals of magnesium calcium iron dry ramming mass are high melting point phases such as magnesium oxide and calcium oxide, the magnesium calcium iron dry ramming material has good high-temperature resistance and slag corrosion resistance. It can be sintered quickly and form a solid whole during use, so it has strong anti-erosion ability, good high-temperature toughness, and is not easy to float during use.
Effect of ramming mass
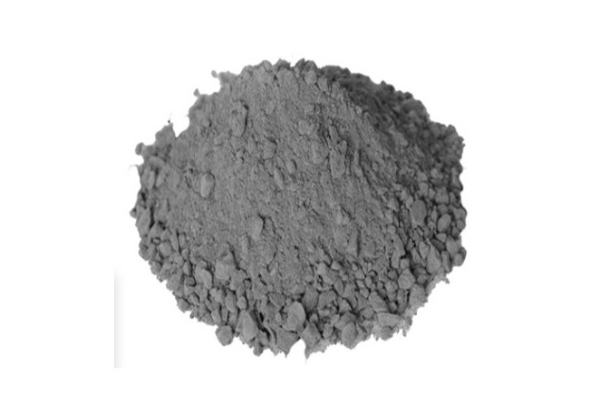
The on-site use results show that the erosion rate of magnesium-calcium-iron dry ramming mass furnace lining is slow and has strong repairability. It can significantly reduce the labor intensity of repairing and dismantling the furnace lining, directly improve the economic benefits of the steel plant, and reduce costs; at the same time, it reduces the time for changing the furnace shell, speeds up the production rhythm, and improves the efficiency of the electric furnace.
WeChat
Scan the QR Code with wechat