세라믹 가마용 내화 벽돌을 선택하기 위한 요구 사항은 무엇입니까?
생산 기술의 향상으로, 세라믹 가마는 내화 재료에 대한 더 높은 기준과 요구 사항을 가지고 있습니다.. 현재, 세라믹 가마는 세라믹 제품을 소성하는 기능을 만족시키면서 가마의 수명을 최대한 향상시키고 에너지를 절약해야 합니다.. Different parts of the ceramic kiln use different refractory materials. The refractory materials used in the ceramic kiln can be divided into two categories: heat preservation and heat insulation.
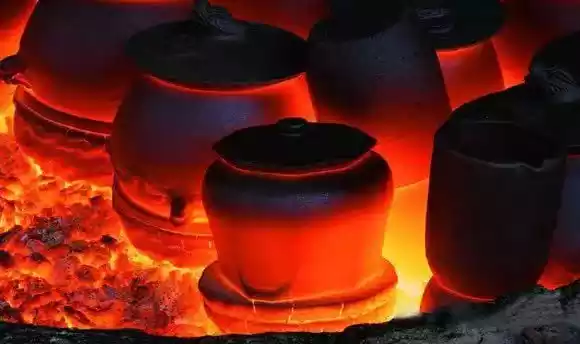
What are the requirements for refractory materials in ceramic kilns?
Thermal conductivity of refractory bricks
The ceramic kiln uses refractory materials with low thermal conductivity, which can reduce the surface temperature of the kiln, reduce the loss of heat dissipation, and reduce the cost of producing ceramics.
굴곡강도
The flexural strength of refractory bricks has a certain influence on the structural stability of ceramic kilns. High flexural strength refractory bricks can prolong the service life of the kiln and reduce the deformation and cracking of the kiln caused by thermal expansion. 게다가, refractory bricks with high flexural strength can ensure that the ceramic kiln can carry higher loads.
Load softening temperature
일반적으로, the load softening temperature of the inner layer material of the ceramic kiln should be 100-500°C higher than the normal working temperature of the kiln, such as firing a porcelain brick kiln, the load softening temperature of the inner layer material of the firing zone should be higher than 1380°C. 그렇지 않으면, during the operation of the kiln or when the kiln is ignited and baked because the short-term kiln temperature is higher than the long-term use temperature, the furnace body will be deformed or even sunk and damaged.
Changes in reburn line
The maximum operating temperature refers to the experimental temperature at which the refiring line changes no more than 2% for 24 hours of continuous heat preservation. When the refractory ceramic fiberboard is used in a ceramic kiln, if excessive refiring shrinkage occurs at high temperatures, the furnace body will be damaged. The increase in the brick joints will affect the integrity and airtightness of the furnace body, and even cause damage to the furnace body structure, especially the kiln roof bricks, whose shrinkage will cause the kiln roof to sink and deform. Relatively speaking, burning expansion is less harmful, especially small expansion often has a good effect on prolonging the life of the kiln body.
Thermal Shock Stability
Thermal shock stability refers to the ability of refractory materials to resist rapid temperature changes without being damaged. There are also certain requirements for the thermal shock stability of refractory bricks in ceramic kilns.
For the batch kiln, the kiln body must be heated from room temperature to the firing temperature of ceramic products for each operation and then lowered to room temperature after holding for a period of time. Repeated heating and cooling in this way, if the thermal shock resistance of the refractory material is not good, it is easy to crack, peel off and turn around the refractory brick, which will cause the kiln body to collapse in severe cases.
For ceramic kilns with continuous operation, such as tunnel kilns and roller kilns, although they are operated continuously and run day and night, kiln shutdown will also occur when the kiln is powered off, fuel is cut off, equipment is damaged, and periodic maintenance. Every shutdown of the kiln means the process of dropping from the firing temperature to room temperature and then heating to the firing temperature, so the life of the kiln is closely related to the thermal shock resistance of the refractory material.
게다가, thermal shock stability is even more important for ceramic kiln furniture and kiln cars, which are constantly subjected to heat and cold cycles. 그러므로, ceramic fiberboards used in kiln furniture and kiln cars must have good thermal shock resistance.
위챗
위챗으로 QR코드 스캔