Material introduction of bottom pouring brick
Generally speaking, the materials of bottom pouring brick include high alumina bricks, саз кірпіш, and mullite bricks.Applied to the tablet steel casting of various alloy structural steels (including stainless steel and various carbon steels). The product has high refractoriness, strong resistance to fracture, and strong resistance to adhesion. The appearance is neat, the flow channel is smooth, the size is precise and the quality is excellent. It is used to produce ladle lining bricks, arc lining bricks, fired and unfired plug bricks, casting mouth bricks, seat bricks, and sleeve bricks for ladle castings. High-quality raw materials and unique processing technology give the product excellent high-temperature physical and chemical properties, corrosion resistance, and no deformation or falling off.
Application of bottom pouring bricks
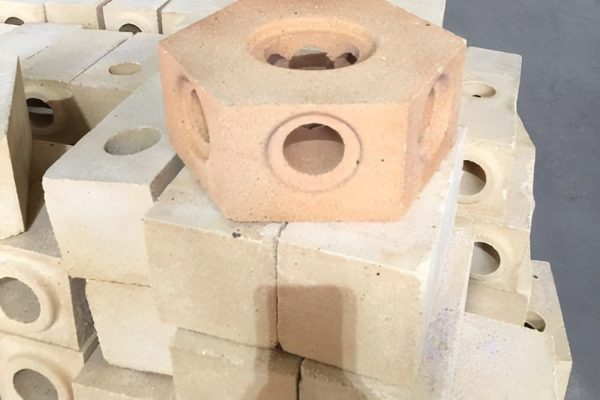
Applied to the tablet steel casting of various alloy structural steels (including stainless steel and various carbon steels). The product has high refractoriness, strong resistance to fracture, and strong resistance to adhesion. The appearance is neat, the flow channel is smooth, the size is precise and the quality is excellent. It is used to produce ladle lining bricks, arc lining bricks, fired and unfired plug bricks, casting mouth bricks, seat bricks, and sleeve bricks for ladle castings. High-quality raw materials and unique processing technology give the product excellent high-temperature physical and chemical properties, corrosion resistance, and no deformation or falling off.
Analysis of the characteristics of bottom pouring brick of different materials
In recent years, mullite flow steel bricks are more and more produced, and most of them are expanded and reproduced from clay. Because the surface pores of high alumina bricks are large and the mesh structure is relatively loose, the surface pores of mullite bricks are dense and the surface has fibrous crystals, presenting a network cross structure. This cross-density structure can prevent the deep corrosion of steel bricks by heat convection of molten steel. In general, during the process of steel flowing through water, molten steel will easily react with the refractory of high alumina bricks.
The production process of high-alumina flow brick is similar to that of clay brick, but the difference is that it contains more high-alumina cement clinker, has higher refractoriness than clay brick, and has good resistance to strong acid and alkali, so it is suitable for various kiln belts. AI203 aluminum silicate fiber felt flow brick with a water content of more than 48% is generally called high-alumina flow brick.
Clay bottom pouring brick refers to clay products made of aluminum silicate felt with a moisture content of 30%-40% AI203. Clay flow bricks are made of 50% soft plastic clay and 50% hard plastic clay clinker, which are mixed according to the required particle size distribution requirements, formed and dried, and fired at a high temperature of 1300-1400℃. The mineral composition of clay flow bricks is mainly kaolinite (AI203.2Si02·2H20) and 6%-7% residue (potassium, sodium, calcium, titanium, iron oxides). The firing process of clay flow bricks is mainly the process of kaolinite continuously dissolving into mullite (3AI203·2Si02) crystals. Si02 and A1203 in clay flow bricks form eutectic low-melting aluminum silicate with residues during the firing process, which surrounds the mullite crystals. Clay flow steel bricks belong to acidic fireproof material products, which can resist the corrosion of acidic and alkaline slag and acidic and alkaline gases, but have weaker resistance to alkaline chemicals.
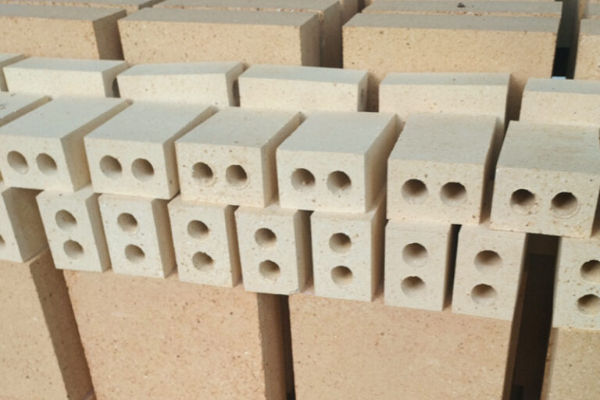
Clay bottom pouring bricks have good thermal properties and are resistant to rapid cooling and heating. The refractoriness of clay flow bricks is similar to that of silica bricks, reaching 1690-1730℃, but the load softening temperature is about 200℃ lower than that of silica bricks. Because clay flow bricks contain not only highly refractory mullite crystals but also nearly half of the low-melting-point amorphous glass phase. Within the temperature range of 0-1000℃, the volume of clay flow bricks expands uniformly with the increase of temperature, and the linear expansion curve is close to this line. The linear expansion rate is 0.6%-0.7%, which is only about half of that of silica bricks. When the temperature reaches 1200℃ and then rises again, its volume will begin to shrink from the maximum expansion value. The residual shrinkage of clay flow bricks causes the cracking of the filler wall mortar, which is a major defect of clay bricks. When the temperature exceeds 1200℃, the low-melting-point substances in the clay flow steel bricks gradually melt, and the particles are too close to each other due to the surface tension, resulting in volume contraction. Since the load softening temperature of clay flow steel bricks is low, they will contract at high temperatures, and the heat conductivity is 15%-20% lower than that of silica bricks, and the impact toughness is also worse than that of silica bricks. Therefore, clay flow steel bricks can only be used in alternating primary and secondary positions, such as heat storage room sealing walls, small exhaust duct lining bricks and heat storage room checkerboard bricks, furnace mouth lining bricks, furnace top and riser lining bricks, т.б.
WeChat
wechat арқылы QR кодын сканерлеңіз