Float glass furnace
Float glass furnace refractories for each part
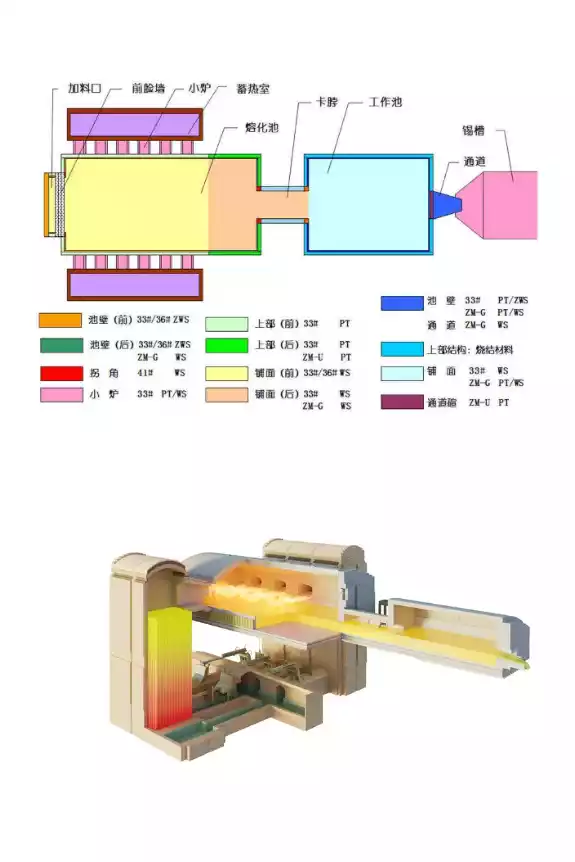
1. L-shaped hanging wall
Silica brick
2. Melting part
Fused Brick Silica Brick
3. Stuck neck
Silica brick
4. Cooling unit
Corundum refractories, silica bricks
5. Annealing kiln, regenerator
High alumina bricks, саз кірпіш, directly bonded magnesia chrome bricks
Glass production process
Glass: an amorphous solid substance obtained by cooling and hardening of a molten substance. The production process includes the preparation of raw materials – the melting of molten glass – the shaping of glass products – the annealing of glass products. The process in the glass kiln includes the mixing of glass batch materials in a reasonable It melts into a liquid phase under the temperature regime, homogenizes and clarifies it, and becomes a transparent liquid.
Silica brick
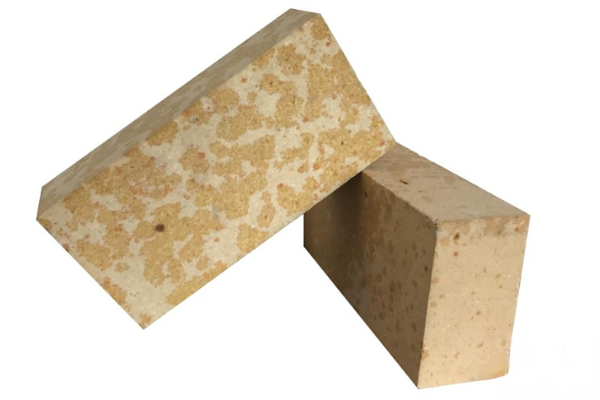
Silica bricks are refractory products with a SiO2 content of more than 93%. They are made from silica with a silicon content of >96%, adding mineralizers and binders, and then mixing, shaping, drying, and firing. They are mainly used for coke oven carbonization. Chambers, combustion chambers and partition walls, glass kiln roofs, kiln walls, high-temperature load-bearing parts of hot blast furnaces carbon roasting furnaces, and other kilns. True density <2.35. It is an acidic refractory material, which is highly resistant to acidic slag or acidic solution corrosion, but has poor resistance to alkaline corrosion; the load softening temperature is high at 1640~1680℃; It has poor thermal shock resistance and fire resistance of 1690~1730℃.
project | index | ||||
BG-96A | BG-96B | BG-95 | JG-94 | G1-94>96 | |
Sio2% | ≥96 | ≥96 | ≥95 | ≥94.5 | ≥94 |
Fe2O3 | ≤0.6 | ≤0.8 | ≤1,0 | ≤1.2 | ≤1.4 |
Melt index % | ≤0.5 | ≤0.7 | / | / | / |
Apparent porosity % | ≤21 | ≤22 | ≤22 | ≤22 | ≤24 |
True density g/cm3 | ≤2.34 | ≤2.33 | |||
Normal temperature compressive strength MPa | ≥40 | ≥35 | ≥30 | ≥40 | ≥30 |
0.2MPa load softening temperature℃ | ≥1680 | ≥1670 | ≥1670 | ≥1650 | ≥1650 |
Heating permanent line changes %1450℃*2h | 0-0.2 | ||||
Residual quartz % | ≤3 | ≤1,5 | / |
Fused zirconia corundum brick
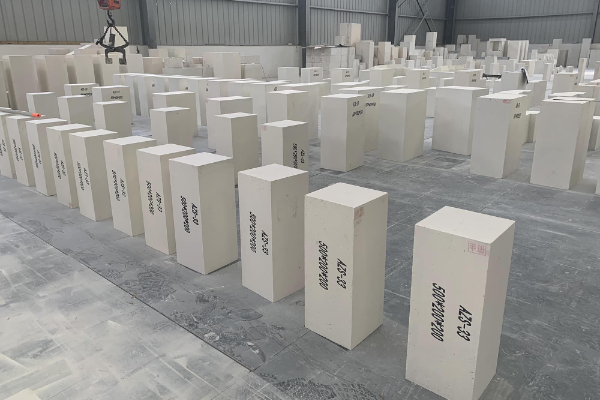
Fused zirconia corundum bricks are used to build kiln pool walls, flame space parapets, small furnace spouts, small furnace level gates, small furnace stacks, tongue gates, т.б. Fused zirconia corundum bricks with 41% zirconium content are used for The corners of the masonry pool wall, the liquid flow hole, and other parts where the glass liquid has the most severe erosion on the refractory material. This material is the glass industry’s most widely used fused cast refractory.
Элемент | Fused Cast AZS Brick | |||
Индекс | RS-AZS33 | RS-AZS36 | RS-AZS41 | |
Chemical Composition% | Al2O3 | ≥50.00 | ≥49.00 | ≥45.00 |
ZrO2 | ≥32.50 | ≥35.50 | ≥40.50 | |
SiO2 | ≤15.00 | ≤13.50 | ≤12.50 | |
Na2O+K2O | ≤1.30 | ≤1.35 | ≤1.30 | |
Volume density g/cm3 | ≥3.75 | ≥3.85 | ≥4.00 | |
Apparent Porosity % | ≤1.2 | ≤1,0 | ≤1.2 | |
Cold Crushing Strength Mpa | ≥200 | ≥200 | ≥200 | |
Exudation Temperature of Glass Phase | ≥1400 | ≥1400 | ≥1410 | |
Bubble Separation Ratio(1300℃×10h) | ≤1.2 | ≤1,0 | ≤1,0 | |
Anti-corrosion rate of glass liquid 1500℃×36h (mm/24h)% | ≤1.4 | ≤1.3 | ≤1.2 | |
Bulk density(g/cm3) | Ordinary casting PT(RN RC N) | ≥3.55 | ≥3.55 | ≥3.70 |
No shrinking casting ZWS(RR EVF EC ENC) | ≥3.65 | ≥3.75 | ≥3.85 | |
Tilt casting QX(RO) | ≥3.65 | ≥3.75 | ≥3.90 | |
No shrinkage casting WS( RT VF EPIC FVP DCL) | ≥3.75 | ≥3.80 | ≥3.95 |
Магнезия кірпіш
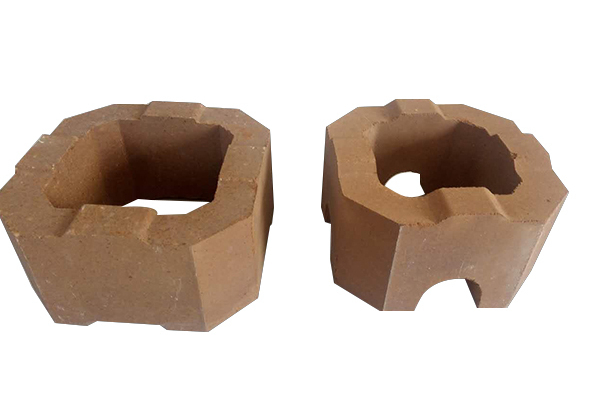
The glass kiln regenerator will use 98 magnesia bricks and 96 magnesia bricks
project | MZ-95 | MZ-96 | MZ-97 | MZ-98 | ||||
straight bricks | Tubular brick | straight bricks | Tubular brick | straight bricks | Tubular brick | straight bricks | Tubular brick | |
Mgo% | ≥95 | ≥95 | ≥96 | ≥96 | ≥96.7 | ≥96.7 | ≥97.2 | ≥97.2 |
Sio2 % | ≤1.8 | ≤1.8 | ≤1,5 | ≤1,5 | ≤1,0 | ≤1,0 | ≤0.6 | ≤0.6 |
Ca0 % | ≤2.0 | ≤2.0 | ≤1.8 | ≤1.8 | ≤1,5 | ≤1,5 | ≤1.3 | ≤1.3 |
Көлемді тығыздық г/см3 | ≥2.95 | ≥2.93 | ≥2.98 | ≥2.95 | ≥3.0 | ≥2.98 | ≥3.02 | ≥3.0 |
Apparent porosity % | ≤17 | ≤18 | ≤16 | ≤17 | ≤15.5 | ≤16.5 | ≤15.5 | ≤16.5 |
Normal temperature compressive strength MPa | ≥70 | ≥60 | ≥70 | ≥60 | ≥70 | ≥60 | ≥70 | ≥60 |
0.2MPaload softening temperature ℃ | 1680 | 1680 | ≥1700 | |||||
Thermal shock resistance 950℃ air times | ≥10 |
Dense zircon bricks
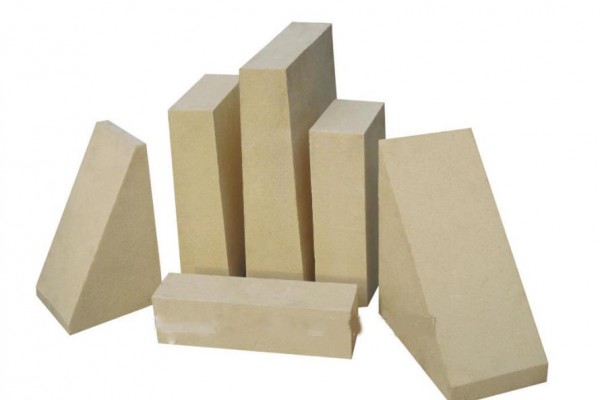
Dense zircon stone is manufactured using isostatic pressing/sintering technology. It has excellent properties such as high-temperature resistance, good thermal shock resistance, and resistance to glass liquid erosion. It is mainly used in the bottom and upper space of alkali-free glass and borosilicate glass tank kilns. Bricks, hook bricks, gap bricks, trough bricks, thermocouple bricks, and viewing hole bricks.
project | ZS-G | ZS-Z | ZS-65A | ZS-65B | ZS-63 |
Zro2 % | ≥65 | ≥68 | ≥65 | ≥65 | ≥63 |
Sio2 % | ≤33 | ≤30 | ≤33 | ≤33 | ≤35 |
Fe203 % | ≤0.2 | ≤0.2 | ≤0.2 | ≤0.2 | ≤0.2 |
TiO2 % | ≤1.2 | ≤1.2 | ≤1.2 | ≤1.2 | / |
Көлемді тығыздық г/см3 | ≥4.3 | ≥4.1 | ≥3.7 | ≥3.6 | ≥3.55 |
Apparent porosity % | ≤1 | ≤11 | ≤17 | ≤19 | ≤20 |
Normal temperature compressive strength MPa | ≥300 | ≥200 | ≥100 | ≥80 | ≥60 |
0.2MPa load softening starting temperature ℃ | ≥1700 | ≥1700 | ≥1680 | ≥1650 | ≥1600 |
Sintered zirconium corundum brick
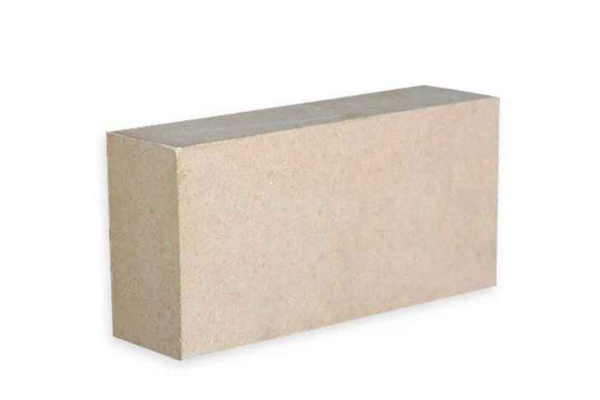
Sintered zirconium corundum bricks have good resistance to alkali vapor and thermal shock. They are mainly used in the flame space of glass kilns, regenerator bricks, and upper grids. They can also be used in float glass kilns and daily glass kilns. Pave the bottom or forehearth with large bricks.
project | AZS-16 | AZS-20 | AZS-32 |
Zro2 % | ≥16 | ≥20 | ≥32 |
Fe203 % | ≤0.5 | ≤0.5 | ≤0.5 |
Көлемді тығыздық г/см3 | ≥2.7 | ≥2.8 | ≥3.2 |
Apparent porosity % | ≤20 | ≤18 | ≤18 |
Normal temperature compressive strength MPa | ≥70 | ≥80 | ≥80 |
0.2MPa load softening starting temperature ℃ | ≥1580 | ≥1620 | ≥1630 |
Zero expansion silica bricks for repair
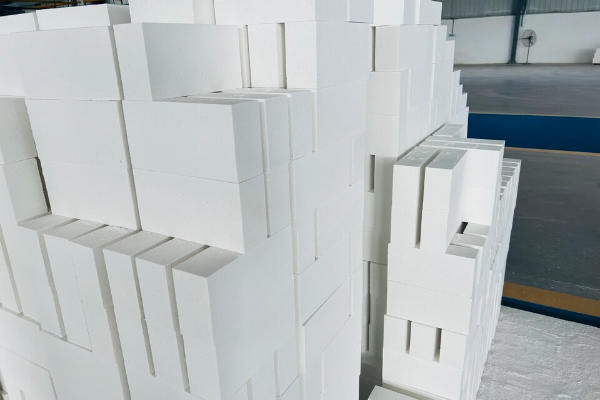
The linear expansion coefficient of zero-expansion silica brick is close to 0, it has excellent thermal shock resistance, high softening temperature under load, and is safe and reliable for long-term use.
project | FS-97 | FS-98 | FS-99 |
Sio2 % | ≥97 | ≥98 | ≥98.5 |
Al203 % | ≤0.5 | ≤0.3 | ≤0.2 |
Fe203 % | ≤0.3 | ≤0.2 | ≤0.1 |
Bulk density g/cm3 | ≥1.75 | ≥1.8 | ≥1.85 |
Apparent porosity % | ≤22 | ≤20 | ≤18 |
Normal temperature compressive strength MPa | ≥25 | ≥30 | ≥35 |
0.2MPa load softening starting temperature ℃ | ≥1500 | ≥1600 | ≥1650 |
Linear expansion rate % 1000℃ | ≤0.2 | ≤0.2 | ≤0.2 |
Thermal shock resistance 1100℃ water cooling times | ≥30 | ≥30 | ≥30 |
Low porosity clay brick
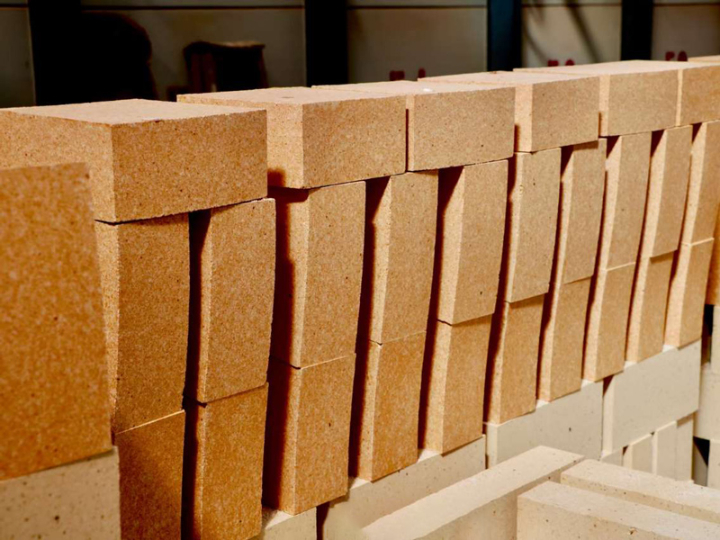
project | DN-11 | DN-14 | DN-17 | ZN-45 | ZN-40 | ZN-40 |
Al203 % | ≥47 | ≥45 | ≥42 | ≥45 | ≥40 | ≥36 |
Fe203 % | ≤1.2 | ≤1,5 | ≤1.8 | / | / | / |
Bulk density g/cm3 | ≥2.4 | ≥2.34 | ≥2.26 | / | 2.0-2.4 | / |
Apparent porosity % | ≤11 | ≤14 | ≤17 | ≤16 | ≤19(22) | ≤22(24) |
Normal temperature compressive strength MPa | ≥80 | ≥65 | ≥50 | ≥60 | ≥40(35) | ≥35(30) |
0.2MPa load softening starting temperature ℃ | ≥1520 | ≥1470 | ≥1430 | ≥1430 | ≥1430 | ≥1380 |
Heated permanent line change % x2h | 0.1~-0.21500 | +0.1~-0.21400-0.2-+0.1 | -0.2~+0.1 | -0.3~+0.1 | -0.4~+0.1 |
WeChat
wechat арқылы QR кодын сканерлеңіз