マグネシア炭素煉瓦の製造工程のご紹介
マグネシウムカーボンレンガは、 耐高温耐火物, 主に高温窯のライニングに使用されます。. Mgo-c ブリックはコンバーターで使用できます, 電気炉, ひしゃく, および他の部分, 窯の重要な耐火物です.
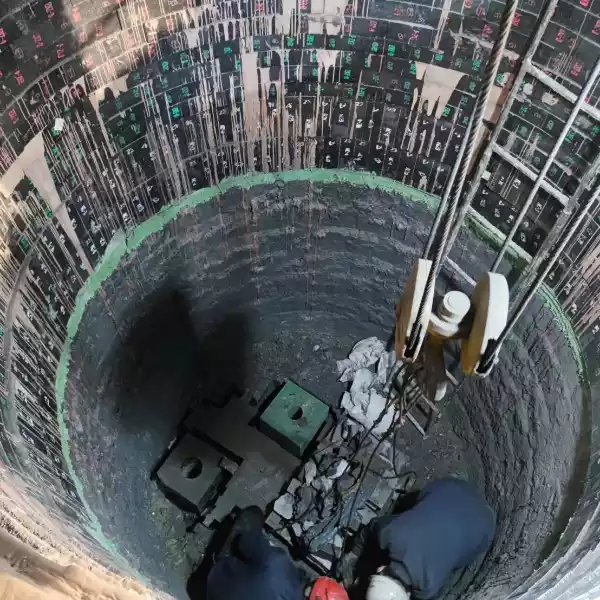
マグネシアカーボンレンガ 高温耐性の特性を持っています, 強い耐スラグ性, 優れた耐熱衝撃性, 高温クリープが小さい. マグネシアカーボンレンガの主成分はマグネシアとカーボンです。. マグネシアカーボンれんがの具体的な製造プロセスは次のとおりです。:
マグネシウム炭素レンガを製造する 2 つの方法
マグネシアカーボンレンガを作るには2つの方法があります: 焼成油含浸マグネシアカーボンレンガと 未焼成マグネシアカーボンレンガ. 前者のレンガ製造プロセスはより複雑で、ほとんど使用されません。. 未焼成マグネシアカーボンれんがの製造方法は次のとおりです。.
マグネシアカーボンレンガはどのように作られるのか?
泥の準備
繁殖時には粒子の臨界サイズの選択が重要です. 微細な骨材粒子により開気孔率が減少し、抗酸化能力が向上します。. しかし, 小さな凝集粒子は閉気孔を増加させ、嵩密度を低下させます。. 加えて, 細粒のMgO骨材は黒鉛と反応しやすい, 一般的に粒径は1mm程度と考えられています。. 高圧成形機条件下, マグネシアの粒子は微細化する傾向があります.
成分にグラファイトが添加されている
材料に添加されるグラファイトの質と量が重要です. 一般的に言えば, 耐火レンガ中の黒鉛含有量を増やすと、耐スラグ性と耐火レンガの熱衝撃安定性が向上します。, ただし強度や耐酸化性は低下します。. マグネシアカーボンれんがの炭素含有量が少なすぎる場合 (<10%), 耐火レンガにネットワーク骨格が形成できない場合, カーボンの利点が十分に発揮できない. したがって, 炭素含有量は、以下の範囲でより適切です。 10-20%.
マグネシウムカーボンレンガ製造のための原料混合
混合プロセス中, グラファイトがマグネシア粒子を均一に取り囲むようにする, 給餌シーケンスは次のようにする必要があります: マグネシア粒子→結合剤→黒鉛→マグネシア微粉末, および添加剤粉末. 黒鉛の含有量が多いため、, 低密度, そして極微量の添加物, 均一に混ぜるには長い時間がかかります, ただし、混合時間が長すぎる場合は、, マグネシア粒子の周りの黒鉛と微粉末が簡単に落ちます。, したがって、混合時間は適切である必要があります.
マグネシアカーボンレンガの成形
MgO-Cレンガの形成は耐火レンガの構造をコンパクトにする重要な要素です: 材料に添加される黒鉛の質と量は非常に重要です. 泥中の大量の黒鉛と骨材の重要な粒子が小さいため, 高圧成形を使用し、軽量第一の作業手順で厳密にプレスすることをお勧めします。, 重圧, 亀裂の形成を避けるための複数の圧力. 掃除機をかけるという操作手順を採用することをお勧めします。, 疲労とプレッシャー. 加えて, 高圧成形されたアドビの表面は非常に滑らかです, 取り扱い中や組み立て中に滑りやすくなっています。. したがって, 形成された日干しレンガには、滑りを防ぐための樹脂フィルムを形成するために、厚さ 0.1 ~ 2 mm の熱硬化性樹脂を含浸またはコーティングする必要があります。. 一般に滑り止め加工と呼ばれる加工です。.
MgO-Cレンガの熱処理
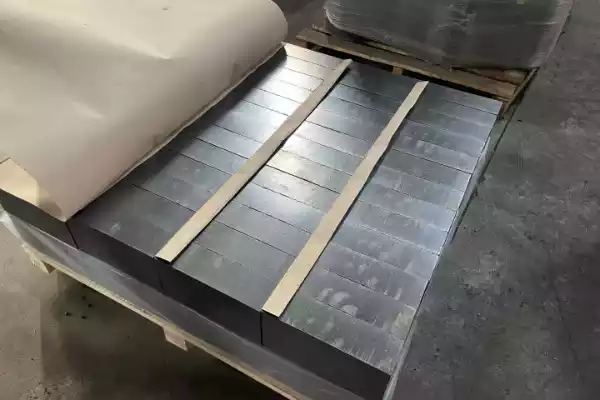
成形されたマグネシア カーボン アドビは、使用する前に硬化する必要があります。, 硬化時の温度の流行は耐火レンガの性能に大きな影響を与えます. 200~250℃での硬化処理がより適していることが研究により証明されています。, これはレンガのかさ密度を確保し、空隙率を減らすのに適しています。. 250℃を超える場合、または200℃未満の場合, 硬化処理は悪影響を及ぼします. 空気を厳密に管理する必要がある. 通常50~60℃, 樹脂が軟化するため, 適切に保温する必要があります; 100~110℃で, 溶剤が大量に排出されるため, 暖かくしておかなければなりません; 200~250℃で, 反応を完了させるために, 適切に保温する必要もあります.
微信
wechatでQRコードをスキャンしてください