Altoforno fusorio e refrattari
Un altoforno è un tradizionale dispositivo di combustione utilizzato per riscaldare metalli o altre sostanze. Il suo principio di base è quello di fornire energia termica ad alta temperatura fornendo una grande quantità di aria alla camera di combustione per far bruciare la fiamma più vigorosamente. Gli altiforni sono ampiamente utilizzati nel processo di fusione grezza del rame, Guida, piombo-zinco, antimonio, e altri metalli.
La struttura dell'altoforno
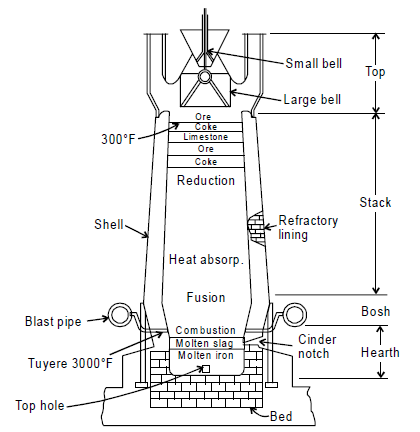
L'altoforno è composto da una volta del forno, corpo del forno, letto principale (detta anche gola), focolare, dispositivo ugello, e così via.
Piano del forno
Il tetto è la parte superiore di un altoforno, noto anche come tetto. È una struttura sigillata utilizzata per coprire la parte superiore del corpo del forno per mantenere alte temperature nel forno e controllare efficacemente il processo di combustione. Una serie di porte del forno o porte di caricamento sono solitamente disposte sulla volta del forno per l'alimentazione o lo scarico dei prodotti nel forno.
Involucro della fornace
Il pozzo del forno è la struttura cilindrica principale dell'altoforno, che è il contenitore per la carica e il carburante e ospita il processo di fusione. Il corpo del forno è solitamente costruito con mattoni refrattari o materiali refrattari per mantenere la stabilità strutturale alle alte temperature. Di solito è presente un'uscita delle scorie sul fondo del corpo del forno per scaricare le scorie di scarto generate nel forno.
Livello di Tuyere o bosh
Il basamento è la zona conica inferiore dell'altoforno, detto anche focolare. Durante il processo di fusione, minerale, coke, e gli altri combustibili vengono immessi nel letto attraverso la volta del forno. In questo letto, iniziano le reazioni di fusione e i gas caldi risultanti e il metallo liquido salgono verso la parte superiore del vano forno.
Focolare dell'altoforno
Il focolare è un altro nome comune per il letto, che è l'area direttamente correlata alla reazione di fusione nell'altoforno. Nel focolare, il gas ad alta temperatura prodotto dalla combustione del coke reagisce con il minerale di ferro, riducendo il minerale di ferro a ferro liquido, mentre le scorie di scarto formano schiuma e galleggiano sulla superficie del ferro fuso.
Sistema Tuyere
Il dispositivo a tubiera è una parte importante dell'altoforno. Viene utilizzato per introdurre aria ad alta pressione (solitamente aria del forno) nel fondo del forno per controllare e mantenere l'apporto di ossigeno necessario per la reazione di fusione in questo letto. Di solito ci sono più tubiere distribuite attorno al perimetro dell'altoforno, che è collegato ai ventilatori e alle condutture ad alta pressione. Regolando la posizione della tubiera e il flusso d'aria, l'operatore può controllare con precisione la temperatura e il processo di reazione nel forno.
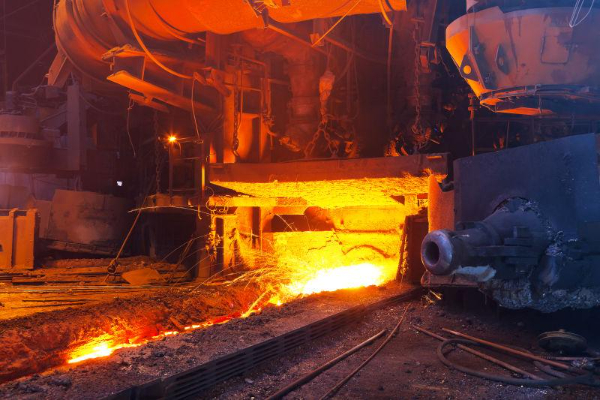
Come funziona un altoforno?
Materiali solidi come la carica di fusione (concentrarsi, minerale sinterizzato, eccetera.), coke, flusso, e il materiale inverso vengono aggiunti dalla parte superiore del forno, e l'aria ad alta pressione soffiata nel dispositivo a tubiera sul lato della parte inferiore del corpo del forno sta salendo, e i materiali verso il basso subiscono reazioni come la fusione, ossidazione, e riduzione per completare il processo di fusione. Metallo liquido, opaco, e le scorie vengono scaricate dalla gola o dal focolare nella parte inferiore del forno, e gas di combustione, polvere di fumo, metalli gassosi, oppure escono ossidi metallici dallo scarico fumi sulla parte superiore del forno.
Quali materiali refrattari vengono utilizzati negli altiforni?
Attualmente, la maggior parte di essi sono tetti di forni chiusi, e il corpo del forno è una camicia d'acqua completa. I materiali refrattari vengono utilizzati solo nella gola e nel cuore, perché le scorie sono scorie alcaline, quindi la parte della gola è costituita principalmente da mattoni di magnesia, mattoni di magnesia-cromo, e mattoni in alluminio-cromo; La parte superiore è composta da mattoni di magnesia, mattoni cromati di magnesia, e mattoncini in alluminio cromato; il fondo del forno è incassato in un arco rovescio
WeChat
Scansiona il codice QR con wechat