Quali materiali refrattari sono utilizzati nel forno di forgiatura
The working temperature of the forging heating furnace is above 1000°C. Reasonable selection of furnace-building refractory materials is of great significance to ensure the normal operation of the heating furnace, improve the life of the furnace and save energy.
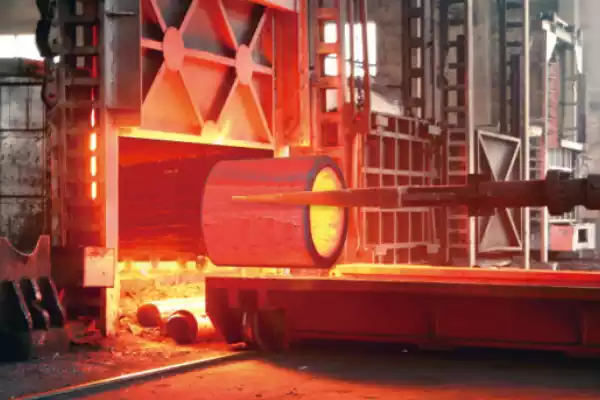
Introduction of forging
La forgiatura è un processo di lavorazione dei metalli necessario che svolge un ruolo fondamentale nella produzione di varie parti e componenti. Ad alte temperature, alta pressione, e dure condizioni di lavoro, refractory materials are the key to ensuring the stable forging process. This article will introduce several joint forging refractory materials and their application in the forging process.
Forging furnace requirements for refractories
- It should have the property of not deforming and not melting under sufficient temperature
- It can have the necessary structural strength at high temperatures without softening deformation
- The volume is stable at high temperatures, and the brickwork will not be deformed or cracked due to expansion and contraction
- When the temperature changes sharply or the heating is uneven, it will not crack and peel off
- Can resist the chemical erosion of metal solution, slag, furnace gas, eccetera.
What are the refractory materials in the forging industry?
Refractory brick
In forging furnaces and heating furnaces, mattoni refrattari are widely used as lining materials to protect furnace structures from high temperatures and molten metal corrosion. The main refractory bricks used are mattoni refrattari ad alto contenuto di allumina, aluminum silicate refractory bricks, E mattoni refrattari al carburo di silicio.

Silicon carbide crucible
UN crogiolo in carburo di silicio is a high-temperature-resistant container made of silicon carbide material. In the forging process, it can be used to carry molten metals and alloys and has excellent heat resistance and corrosion resistance.
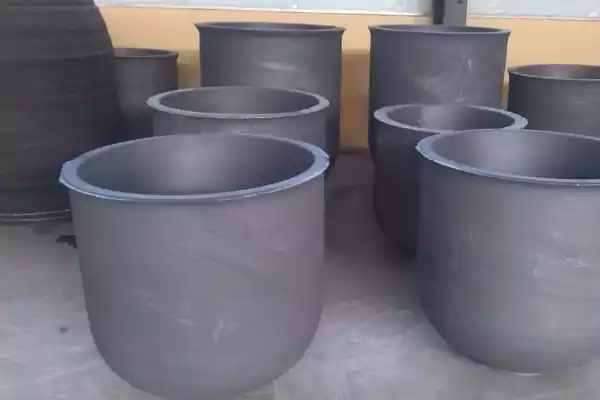
High alumina castable
High alumina castable is a kind of refractory castable, mainly composed of high alumina aggregate and binder. It has good high-temperature resistance and thermal shock resistance and is widely used in forging molds to withstand high-temperature metal pouring.
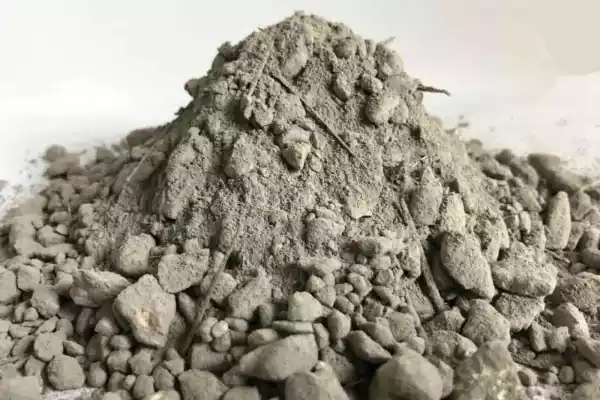
Graphite electrode
Graphite electrode is a refractory material used in high-temperature electric arc furnaces to heat metal materials to a high-temperature state. During the forging process, graphite electrodes are usually used to heat and maintain the temperature of the forging to ensure the smooth progress of the forging process.
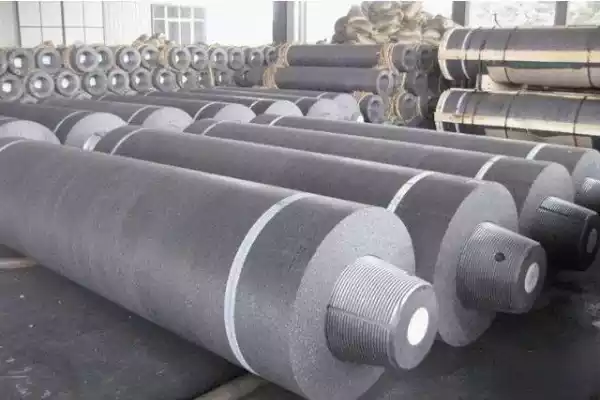
coperta in fibra ceramica
UN coperta in fibra ceramica è un leggero, high-temperature refractory insulation material. It is often used for heat insulation of forging equipment to reduce heat energy loss and improve heating efficiency.
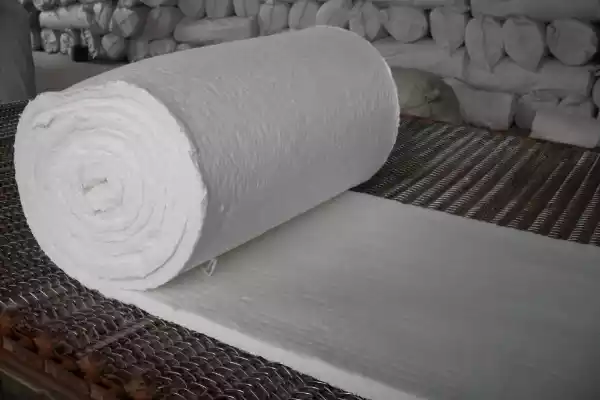
Rivestimento refrattario
IL refractory coating is a refractory material used to coat the surface of forging equipment. It has properties such as high-temperature resistance, resistenza alla corrosione, and wear resistance, which can prolong the service life of forging equipment and improve work efficiency.
How to choose refractory materials for different parts of the forging furnace?
Refractory materials for forging play a vital role in the forging process. They can protect equipment and structures under high temperatures, alta pressione, e dure condizioni di lavoro, ensuring a stable and efficient forging process. According to different forging processes and equipment requirements, the selection of appropriate refractory materials is a key step to ensure the success of the forging process. You can contact us for consultation. Rongsheng Refractories has 20 years of experience in refractory production.
WeChat
Scansiona il codice QR con wechat