Il cemento refrattario è anche chiamato cemento ad alta temperatura. Il grado refrattario di cemento refrattario non è inferiore a 1580 ℃. Il cemento refrattario è un clinker realizzato calcolando la bauxite e il calcare come componente principale, con solfato di calcio come componente principale e un contenuto di allumina di 50%, e poi macinare in polvere fine per creare un materiale cementizio idraulico resistente al fuoco. Può essere usato come rivestimento per il rotatorio di cemento e altri forni industriali.
Tipi di cemento di fuoco refrattario
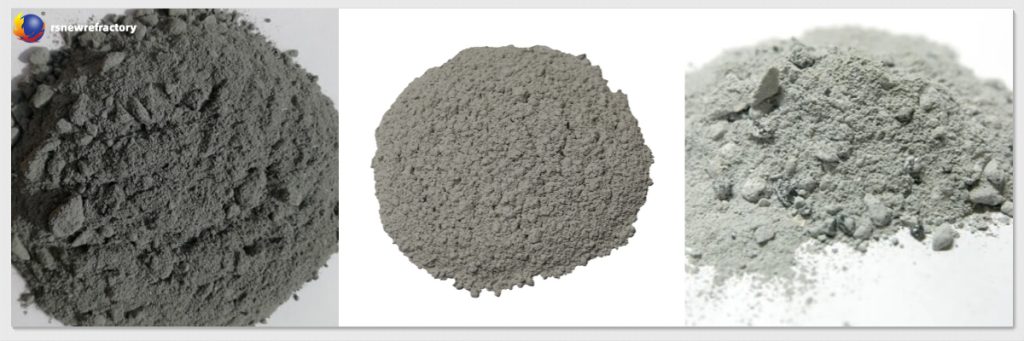
Il cemento refrattario può essere suddiviso in cemento refrattario alluminato, cemento refrattario a basso contenuto di alluminato di calcio, cemento alluminato di calcio e magnesio, e cemento refrattario della dolomite secondo diverse composizioni.
Indicatori fisici e chimici del cemento del forno refrattario
Cemento in alluminato di calcio | ||||||
CA-65 | CA-68 | CA-70 | CA-75 | CA-80 | ||
Composizione chimica(%) | Al2O3 | 64-66 | 67-69 | 69-71 | 73-75 | 77-80 |
CaO | 32-34 | 29-31 | 27-29 | 23-25 | 18-20 | |
SiO2 | 1.8 | 1.2 | 0.3 | 0.3 | 0.3 | |
Fe2O3 | 0.6 | 0.6 | 0.3 | 0.3 | 0.3 | |
Superficie specifica(cm2/g) | 4500 | 4500 | 5000 | 5500 | 7000 | |
Tempo di impostazione(H:min) | Impostazione iniziale(min) | 0:40 | 0:40 | 0:40 | 0:45 | 0:45 |
Impostazione finale(min) | 8:00 | 8:00 | 10:00 | 10:00 | 10:00 | |
Modulo freddo di rottura(MPa) | 24 ora | 6.0min | 6.0min | 6.0min | 6.0min | 5.0min |
72 ora | 8.0min | 8.0min | 8.0min | 8.0min | 6.0min | |
Forza di frantumazione a freddo(MPa) | 24ora | 45.0min | 45.0min | 45.0min | 45.0min | 35.0min |
72ora | 70.0min | 70.0min | 70.0min | 70.0min | 60.0min | |
Refrattarietà(°C) | 1680 | 1710 | 1730 | 1750 | 1770 |
Applicazione di cemento ad alta temperatura
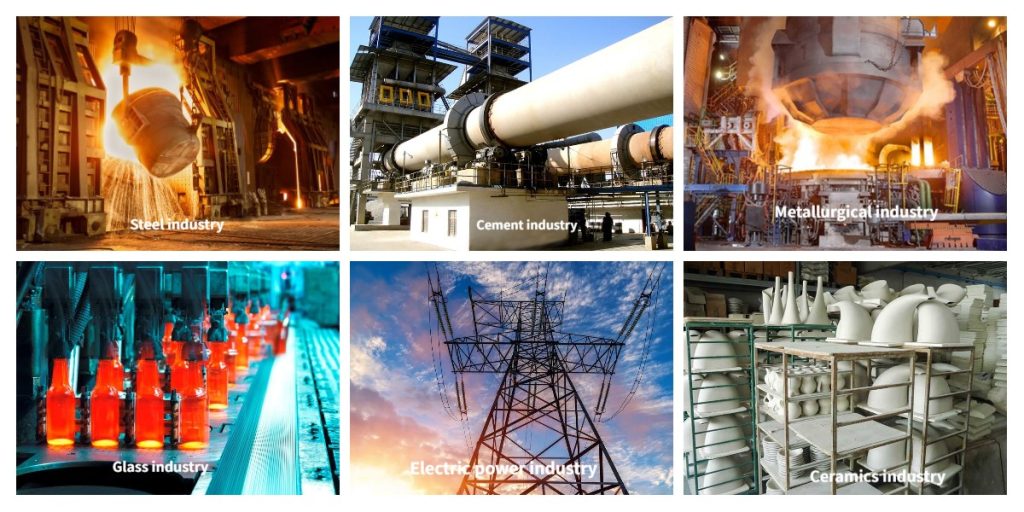
Le principali aree di applicazione del cemento refrattario sono industrie continue ad alta temperatura, come la fusione in acciaio, produzione di vetro, produzione di cemento, corpi di forno, eccetera. Il cemento refrattario è ampiamente utilizzato in questi campi perché può resistere a condizioni di ambiente di lavoro dure come ad alte temperature sostenute, Alte pressioni, corrosione chimica, eccetera.
Cose da notare quando si cottura il rivestimento del forno di cemento refrattario
(1) Alla temperatura normale di 350 ° C, è molto probabile che si verifichi lo scoppio locale, quindi particolare attenzione va posta alla cottura lenta. Se una grande quantità di vapore emerge ancora dopo l'isolamento a 350 ° C, la velocità di riscaldamento dovrebbe essere ancora rallentata.
(2) In condizioni in cui la ventilazione è scarsa e il vapore acqueo non può essere facilmente scaricato, Il tempo di conservazione del calore dovrebbe essere adeguatamente esteso.
(3) Quando si cuoce con olio pesante, Fai attenzione a non spruzzare olio pesante sulla superficie del rivestimento del forno per evitare lo scoppio locale.
(4) Quando si cuoce con legna da ardere, Il contatto diretto con la fiamma spesso provoca un eccessivo aumento della temperatura locale e deve essere protetto.
(5) Il cemento refrattario appena versato deve aspettare 3 giorni prima della cottura.
(6) Anche il raffreddamento del rivestimento del forno di cemento refrattario dovrebbe essere lento e la ventilazione forzata dovrebbe essere evitata.
Confezione e spedizione in cemento forno
Il cemento refrattario è confezionato in sacchi da 25 kg, che può anche essere personalizzato, e poi confezionato in sacchetti tonnellate per facilitare il trasporto e il trasporto.
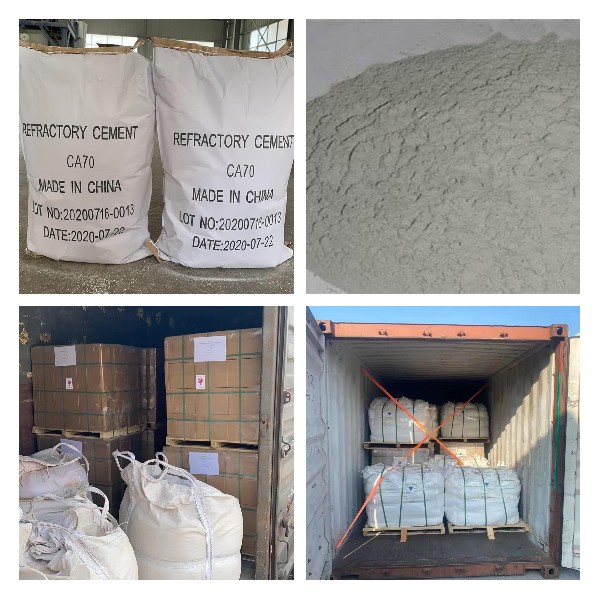
I nostri altri materiali refrattari
Siamo un produttore di materiali refrattari cinesi in grado di produrre mattoni refrattari di materiali diversi; ad esempio mattoni ad alto contenuto di allumina, mattoni di silice, mattoni di corindone, mattoni isolanti in mullite, mattoni di carbone di magnesia, eccetera. Possiamo anche produrre materiali refrattari non formati, ad esempio calcinabili, plastiche refrattarie, e materiali di sperimentazione refrattaria; e può fornire prodotti isolanti del forno; come coperte in fibra ceramica, pannelli in fibra ceramica, e può anche dare ugelli a fusione di mestoli continui e altri materiali refrattari.
I nostri partner
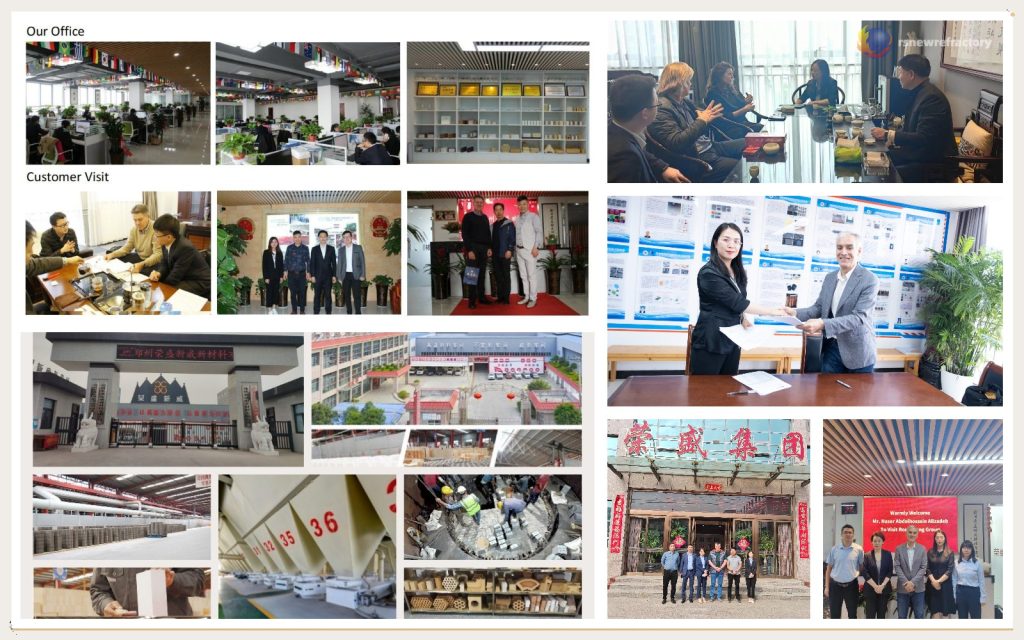
WeChat
Scansiona il codice QR con wechat