Különböző anyagok a bemeneti fúvókához
As an important part of the “three major parts” of continuous casting, the sub entry nozzle has experienced continuous development from a molten quartz nozzle to an aluminum carbon nozzle, and then to the current aluminum carbon-zirconium carbon composite nozzle. Due to its excellent resistance to slag erosion and thermal shock, the aluminum carbon-zirconium carbon composite submerged nozzle has been widely adopted as the mainstream submerged nozzle. The basic requirements for the material of the submerged nozzle are good resistance to molten steel dissolution, strong resistance to slag erosion, and good thermal shock resistance, and it is not easy to get the nozzle blocked.
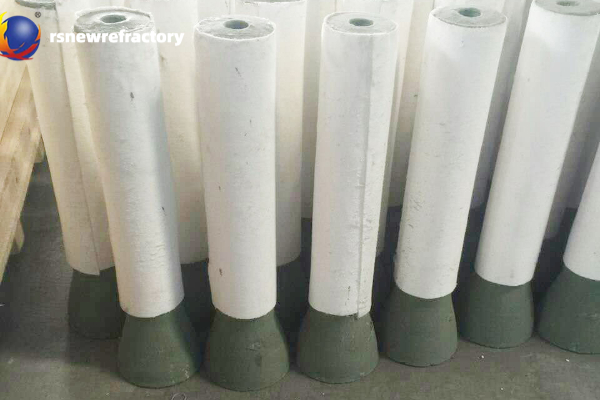
Fused silica nozzle
Fused quartz products have good properties: kicsi hőtágulási együttható, and good volume stability; due to the small thermal expansion coefficient, it has good high-temperature thermal shock stability; good chemical stability, and good acid resistance, except for hydrofluoric acid and concentrated phosphoric acid above 300℃, it has chemical erosion, and basically does not react with other acids; erózióállóság; high temperature is a high viscosity, 105Pa·s (106 poise) at 2000℃, and can reach 5×108Pa·s at 1550℃; nagy szilárdságú, poor thermal conductivity, almost unchanged below 1100℃; low conductivity. Viszont, when used for a long time at high temperatures, crystal transformation will occur, and quartz will precipitate, resulting in cracks and peeling of the nozzle. Ezen kívül, since the fused quartz nozzle can react with manganese in steel, it cannot cast steel with a high manganese content, and can only cast ordinary carbon steel and low manganese steel.
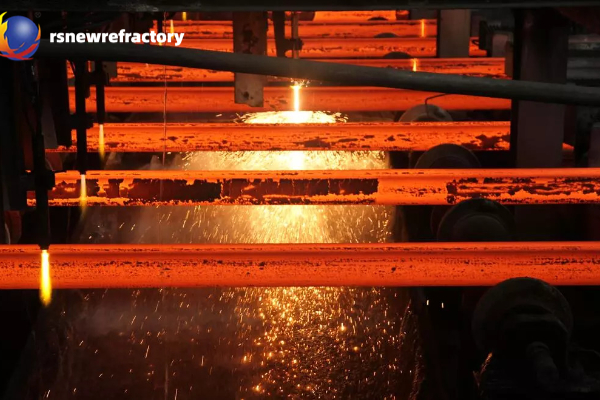
Aluminum carbon submerged nozzle
Aluminum carbon nozzles usually use a composite composed of alumina, fused quartz, and graphite. The material of aluminum carbon nozzle alumina is generally fused or sintered alumina, synthetic mullite, and other synthetic raw materials, and the graphite is flake graphite with a purity of more than 99%. Aluminum carbon immersion nozzles are composed of the above raw materials, and then isostatically pressed and fired in a reducing atmosphere. They are ceramic-bonded composite materials.
Compared with fused quartz nozzles, aluminum carbon nozzles have better resistance to molten steel erosion, less pollution to molten steel, small temperature changes caused by long-term use, és hosszú élettartam. It can realize multi-furnace continuous casting and expand the types of continuous-casting steel. Ebből adódóan, aluminum carbon immersion nozzles have been the mainstream nozzles of continuous-casting crystallizers for a long period of time.
Many nozzles currently used are improved on the basis of aluminum carbon nozzles. Viszont, there are still some defects in the aluminum carbon nozzle during the continuous casting process: poor resistance to mold slag erosion, gyenge hőkancia -ellenállás, and poor thermal conductivity, which will cause slag and alumina inclusions to adhere to the nozzle, resulting in nozzle blockage, seriously affecting the smoothness of continuous casting. Ezen kívül, graphite, one of the raw materials, is dissolved and oxidized by molten steel, causing partial damage to the nozzle.
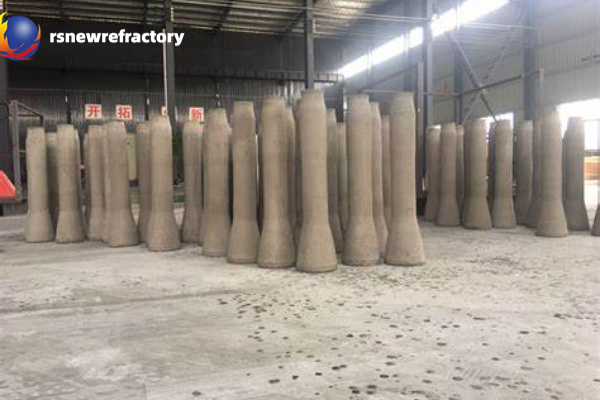
Aluminum carbon-zirconium carbon composite sub entry nozzle
① Aluminum-carbon-zirconium-carbon composite immersion nozzle
With the continuous use of aluminum-carbon nozzles, their disadvantages are gradually exposed in the continuous casting process: the corrosion resistance of aluminum-carbon nozzles is relatively poor, and it is easy to cause local corrosion at the nozzle slag line, forming a “neck shrinkage phenomenon” or even fracture, and it is easy to form Al2O3 and other deposits of molten steel deoxidation products inside the nozzle, causing nozzle blockage, which seriously affects the continuous casting of multiple furnaces. Ebből adódóan, many researchers have continuously studied the material of nozzle refractory materials. On the basis of aluminum-carbon nozzles, aluminum-carbon-zirconium-carbon composite immersion nozzles have been developed, vagyis, the main body is mainly made of Al2O3-C material, and the slag line is composited with a layer of ZrO2-C material. Its multi-layer structure is shown in Figure 1. The material composition of zirconium carbon refractory in the slag line is generally: ZrO2 accounts for 65%~85%, stabilizer CaO accounts for 3%~8%, stabilizer Y2O3 accounts for about 1%, graphite accounts for 10%~20%, and there are some additives. Zirconium carbon refractory is used in the slag line because zirconium oxide has strong chemical stability and is more resistant to continuous casting mold slag erosion than aluminum oxide. ZrO2 dissolved in the slag at high temperatures will increase the viscosity of the mold slag. Ezen kívül, the saturated solubility of zirconium oxide in continuous-casting mold slag is very low, and only a part of it can be dissolved into the slag. The undissolved zirconium oxide particles float on the surface of the liquid slag, which increases the apparent viscosity of the mold slag and reduces its fluidity. This inhibits the erosion of the mold slag on the ZrO2-C material in the slag line, improves the corrosion resistance of the nozzle, and extends the service life of the submerged nozzle.
②The properties of ZrO2 in the slag line
Zirconia has relatively stable chemical properties and is not easy to react chemically with other substances. It also has a high melting point (2700℃), high resistivity, high refractive index, and very low thermal expansion coefficient. Ebből adódóan, it is often used as a high-temperature refractory material and ceramic insulation material. Zirconia has different crystal structures at different temperatures. There are three main types: monoclinic system (m-ZrO2), tetragonal system (t-ZrO2) and cubic system (c-ZrO2).
When heated to 1170℃, monoclinic (m-ZrO2) will transform into tetragonal (t-ZrO2), accompanied by volume shrinkage. When the temperature drops to 850~1000℃, it will transform from tetragonal (t-ZrO2) to monoclinic (m-ZrO2), and volume expansion will occur, accompanied by a volume change of about 3%~5%.
As the refractory material for the slag line of the submerged nozzle, pure zirconium oxide is not used directly but needs to be stabilized before it can be used as a nozzle refractory. Viszont, the thermal expansion coefficient of completely stabilized ZrO2 is large, which will reduce the thermal shock resistance of the submerged nozzle, while the thermal shock stability of the nozzle can be improved by the small expansion coefficient of partially stabilized ZrO2. Ebből adódóan, partially stabilized ZrO2 (PSE) is usually used in the slag line.
Common stabilizers for zirconium oxide include CaO, MgO, Y2O3, stb. The solid solutions formed by these stabilizers and zirconium oxide have different stability. Among them, the solid solution formed by Y2O3 and zirconium oxide will not decompose when heated for a long time at high temperature, while the solid solution formed by MgO and zirconium oxide has the worst stability, and decomposition reaction will occur when heated at high temperature for a long time;
For the solid solution formed by CaO and zirconium oxide, partial decomposition will occur when heated at a high temperature for a long time. Ebből adódóan, in terms of the stability of the solid solution formed after the zirconium oxide is stabilized, Y2O3 has the best effect, but its resources are relatively scarce and expensive.
Ebből adódóan, CaO is generally selected as a stabilizer. Ezen kívül, due to the uneven distribution of zirconium and calcium elements in the stabilized zirconium oxide, the stabilizer CaO will produce desolvation, resulting in the instability of the stabilized zirconium oxide and its corrosion resistance will be reduced. In the zirconium oxide stabilized by Y2O3, the distribution of zirconium and yttrium in the solid solution is very uniform, and it is not easy to produce instability. Ebből adódóan, a small amount of yttrium trioxide is usually added to the calcium-stabilized zirconia, and the amount of calcium oxide added is usually around 3%~8%, and the content of Y2O3 is usually around 1%.
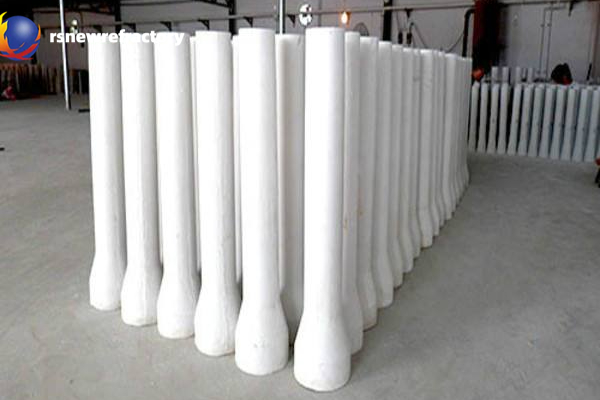
WeChat
Olvassa be a QR-kódot a wechat segítségével