Effect of graphite addition amount on magnesia carbon refractory bricks
Magnesia-carbon refractory bricks are carbon-bonded alkaline bricks that are prepared from magnesia, carbon materials, organic binders, and admixtures and are mixed, high-pressure formed, and treated at low temperatures. This brick takes full advantage of the advantages of alkaline materials and carbon materials, so it has excellent thermal shock resistance, spalling resistance, slag resistance, and high-temperature creep resistance. It is an ideal lining material for metallurgical smelting furnaces.
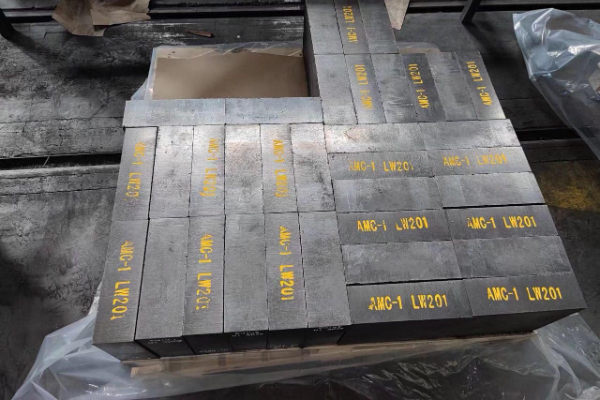
Characteristics of graphite
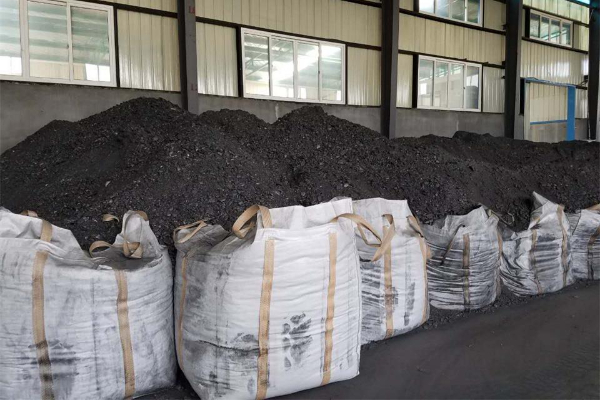
- The melting point of high-temperature resistant graphite is 3850℃±50℃ and the boiling point is 4250℃. Even after ultra-high arc burning, the mass loss is very small and the linear expansion coefficient is also very small. The strength of modifier graphite increases as the temperature increases. At 2000°C, the strength of graphite doubles.
- Electrical and thermal conductivity. The electrical conductivity of graphite is twice as high as that of ordinary non-metallic minerals. Thermal conductivity exceeds that of steel, iron, lead, and other metal materials. Thermal conductivity decreases with increasing temperature, and even at extremely high temperatures, graphite acts as a heat insulator.
- Lubricity. The lubricity of graphite depends on the size of the graphite flakes. The larger the flakes, the smaller the friction coefficient and the better the lubrication performance.
- Chemical stability. Graphite has good chemical stability at room temperature and is resistant to acid, alkali, and organic solvent corrosion.
- Plasticity. Graphite has very good toughness and good plasticity.
- Thermal shock resistance. When graphite is used at high temperatures, it can withstand drastic changes in temperature without being damaged. When the temperature suddenly changes, the volume of graphite does not change much and cracks will not occur.
Effect of graphite on the properties of magnesia carbon bricks
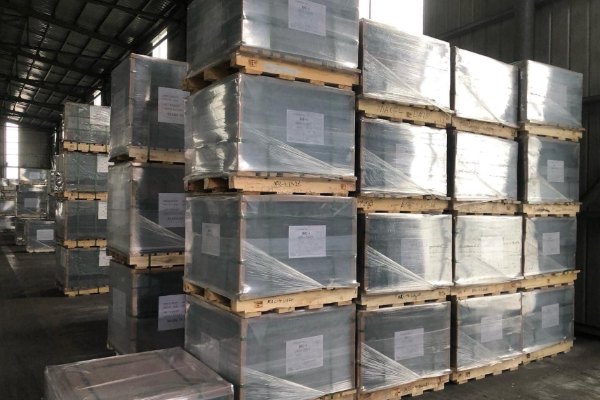
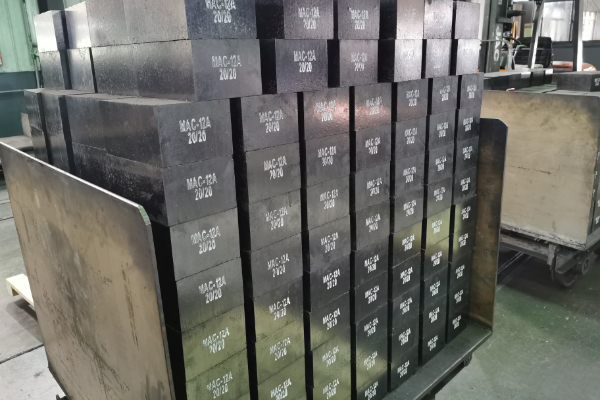
- Graphite content. As the graphite content increases, the strength of magnesia-carbon bricks decreases, the thermal expansion rate decreases, and the residual expansion rate increases. Therefore, the graphite content in the bricks should be controlled at about 20%.
- Graphite purity As the purity of graphite increases, the erosion index of magnesia-carbon bricks drops sharply, and the high-temperature flexural strength index increases significantly. Generally, graphite with a carbon content of greater than 95%, preferably greater than 98%, should be used. Because the higher the purity of graphite, the less ash it contains and the less SiO₂ it contains. Under the action of high temperature, SiO₂ can oxidize the carbon in the bricks, resulting in increased pores and loose structure. It can also interact with MgO, Fe₂O₃, etc. Form low melt, and accelerate the damage of magnesia carbon bricks. In addition, carbon has good thermal conductivity and a small expansion coefficient, and the slag is not easily wetted. Therefore, it can improve the thermal shock resistance of the product and prevent the slag from eroding into the interior of the brick through the pores.
- Graphite flake particle size. As the graphite flake particle size increases. Its anti-oxidation ability is enhanced. When the particle size of flake graphite exceeds 0.125mm, the anti-oxidation property increases slowly. The suitable graphite particle size is 0.125mm. Because graphite is easily oxidized to generate CO, the oxidized graphite loses these excellent properties, reducing the corrosion resistance of refractory materials. This is the fatal weakness of graphite and an important reason for the damage of carbonaceous materials. Therefore, in the actual production of magnesia-carbon bricks, the amount of graphite added should be determined according to the use conditions of carbon-bonded refractory materials, such as the type of smelting equipment, oxygen partial pressure in molten steel and slag, slag characteristics, smelting temperature, and tapping temperature, etc.; The amount of graphite added can also be determined based on whether the products produced emphasize corrosion resistance or thermal shock stability, or require high strength or oxidation resistance.
WeChat
Scan the QR Code with wechat