Comparison between fused corundum and sintered corundum
This article is about the comparison between fused corundum and sintered corundum, including a comparison of chemical composition, organizational structure, sintering performance, mechanical strength, and performance.
Comparison between fused corundum and sintered corundum
- Chemical composition
The A1203 of sintered corundum has high purity, reaching more than 99.5%-99.6%, with few impurities, especially less Na20.
- Organizational structure
The organizational structure of sintered corundum is a dense polycrystalline sintered body with no glass phase; while fused corundum is a single crystal with a flat surface. Sintered corundum is an irregular and polygonal crystal with a crystal size of 5-80 microns, while fused corundum is composed of 1000 micron large crystals in the form of flakes and rods.
- Sintering properties
The sintering performance of sintered corundum is better than that of fused corundum because it is calcined at a temperature above 1800°C and the crystal size grows from 10 microns to more than 100 microns. Dense sintering between crystals is formed. The most obvious difference in the structure between sintered corundum and fused corundum is the crystal size and pore state. The fused corundum has many large pores, the shape is also uncertain, and there are more open pores. The total porosity of sintered corundum is not much different from that of electrofused corundum, but most of them are spherically distributed in the particles in the form of closed pores, and some are concentrated at the grain boundaries. The more developed the crystallization, the larger the pore diameter. During calcination, the shrinkage of sintered corundum is greater than that of electric fusion, precisely because of the shrinkage of sintering. Only then can the shrinkage of the bricks be reduced during firing, thereby ensuring that products with precise dimensions can be obtained, so that the products can be sintered at a lower temperature; for electric corundum products, the molded body has almost no change after being fired, making it difficult to sinter, it is difficult to produce molded body strength.
- Mechanical strength burning
The mechanical strength of Jie Gang Wu is greater than that of electrofusion. Because there are tiny convexities on the surface of the crystal particles, it is easy to combine with the binding agent. + Outside the knife, because the crystals do not grow too much and retain appropriate activity, it is easy to It is densely bonded with various binding agents with high strength; the crystals of fused corundum grow from hundreds of microns to thousands of microns, and the particle surface is smooth and lacks activity, making it difficult to combine with binding agents to form a strong combination. Sintered corundum The mechanical strength is not only related to the crystal size, but also related to the porosity. Because sintered corundum has high density and few pores, it has high strength.
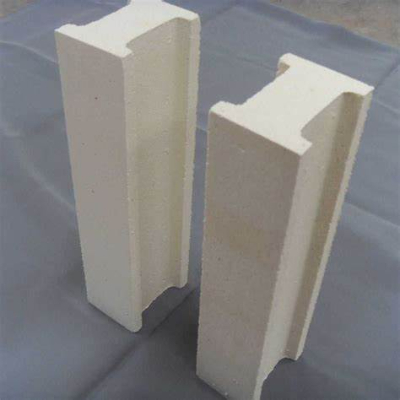
- Performance
According to the above reasons, sintered corundum has high chemical stability, high melting and softening temperatures, large thermal conductivity, excellent resistance to rapid cooling and rapid heating, strong corrosion resistance to molten metal and slag, and excellent high-temperature and Low temperature electrical insulation, stable in oxidizing and reducing atmospheres, very hard, with high wear resistance, most suitable for refractory materials.
WeChat
Scan the QR Code with wechat