Qu'est-ce que le ciment réfractaire?
Le ciment réfractaire est aussi appelé ciment aluminate et ciment haute température. Le ciment aluminate est composé de bauxite et de calcaire comme matières premières, clinker calciné avec de l'aluminate de calcium comme composant principal, et le contenu de l'alumine d'environ 50%, puis enfoncer un matériau cimentaire hydraulique, ciment réfractaire souvent jaune ou brun, mais aussi gris. Le ciment à haute température est généralement utilisé pour doublure des fours industriels.

Classification du ciment réfractaire
Le ciment réfractaire peut être divisé en ciment réfractaire d'aluminate, ciment réfractaire à faible teneur en aluminate de calcium, ciment d'aluminate de calcium et de magnésium, et ciment réfractaire de la dolomite selon les différents composants.
1. Ciment réfractaire d'aluminate
Le ciment réfractaire en aluminate est généralement un ciment réfractaire fabriqué en mélangeant et broyant un clinker réfractaire en aluminate à faible calcium et un clinker de ciment à haute alumine. Par rapport au ciment réfractaire en aluminate à faible calcium: Force précoce plus élevée, réfractarité similaire, et une utilisation cohérente.
2. Ciment réfractaire à faible teneur en aluminate de calcium
Le ciment réfractaire en aluminate à faible calcium est en bauxite de haute qualité et en calcaire dans une proportion appropriée, fritté et rectifié.
3. Ciment d'aluminate de calcium et de magnésium
Le ciment au calcium-magnésium-aminé est principalement composé de bauxite et de dolomite de haute qualité dans une proportion appropriée, fritté et rectifié. La composition du ciment d'aluminate de magnésium de calcium est généralement: l'alumine représente 66% à 74%, l'oxyde de calcium représente 13% à 18%, et l'oxyde de magnésium représente 10% à 13%. Traces de silice et d'oxyde de fer. La composition minérale est en aluminate de calcium et en aluminate de calcium 45% à 60%, et Spinel explique 35% à 50%. La réfractarité est supérieure à 1650 ° C.
3. Ciment réfractaire de la dolomite
Le ciment à haute température à la dolomite est en dolomite comme principale matière première puis ajouté avec l'apatite, minerai de fer, etc..
Quelles sont les exigences techniques pour la production de ciment à haute température?
- La finesse du ciment à haute température: Plus les particules de ciment sont fines, Plus la surface spécifique est grande, la réaction d'hydratation plus rapide et plus suffisante, Et plus la force précoce et ultérieure est élevée.
- Définition du temps de ciment à haute température: Pour s'assurer qu'il y a suffisamment de temps pour terminer divers processus tels que le mélange, transport, et moulure pendant la construction, Le temps de réglage initial du ciment ne doit pas être trop court; Une fois la construction terminée, On espère que le ciment peut durcir dès que possible pour générer de la force, Donc, l'heure de réglage final ne devrait pas être trop longue. La résistance initiale à la résistance au ciment de feu ne doit pas être plus tôt que 45 minutes, et l'heure de mise en scène finale ne doit pas être plus tard que 390 minutes.
- Stabilité du volume du ciment réfractaire: L'uniformité du changement de volume de la pâte de ciment dans le processus de réglage et de durcissement est appelée stabilité du volume du ciment. Si le changement de volume est inégal, La stabilité du volume est mauvaise, et la déformation et la fissuration sont sujettes à se produire, réduire la qualité du projet et même provoquer des accidents.
À quels problèmes doivent être prêts à l'attention lors de la cuisson de la doublure de fournaise de ciment réfractaire?
- À température ambiante de 350 ° C, il est plus susceptible de provoquer des rafales locales, une attention particulière doit donc être portée à la cuisson lente. S'il y a encore beaucoup de vapeur qui sort après avoir gardé au chaud à 350 ° C, la vitesse de chauffage devrait encore être ralentie.
- Dans les conditions d'une mauvaise ventilation et d'une décharge difficile de vapeur d'eau, Le temps de maintien doit être prolongé de manière appropriée.
- Lors de la cuisson avec de l'huile lourde, Il est nécessaire d'empêcher strictement l'huile lourde de pulvériser à la surface de la doublure du four pour éviter l'éclatement partiel.
- Lors de la cuisson au bois de chauffage, Le contact direct avec la flamme rend souvent le chauffage local trop rapide, donc il doit être protégé.
- Pour le nouveau résistant au ciment de feu de feu, il peut être cuit après au moins 3 jours.
- Le refroidissement de la doublure de ciment réfractaire doit également être lent, et la ventilation forcée doit être évitée.
Rongsheng Monolithic Refractories Factory

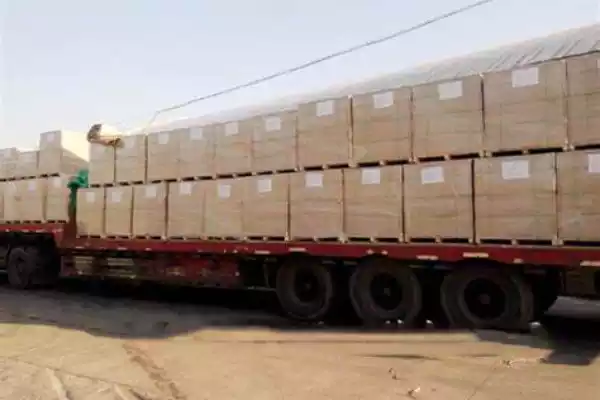
Rongsheng Monolithic Refractory Material Factory est une entreprise qui produit des matériaux réfractaires pour les fours. Le réfractaire monolithique produit comprend castables, bétons à faible teneur en ciment, matériaux de pilonnage, et plastiques. Nous prenons en charge la personnalisation réfractaire des produits et pouvons envoyer des échantillons gratuitement.
WeChat
Scannez le code QR avec wechat