Quels sont les types de ciment réfractaire?
Utilisation de bauxite et de chaux de haute qualité comme matières premières, ils sont mélangés à une quantité appropriée de matière première selon une certaine proportion. Après frittage, on obtient le clinker avec de l'aluminate comme composant principal, puis broyé en poudre fine pour fabriquer un matériau cimentaire résistant au feu et dur à l'eau, appelé ciment réfractaire. Le degré réfractaire du ciment réfractaire n'est pas inférieur à 1580 ℃.
Types de ciment réfractaire
Le ciment réfractaire peut être divisé en ciment réfractaire d'aluminate, ciment réfractaire à faible teneur en aluminate de calcium, ciment d'aluminate de calcium et de magnésium, et ciment réfractaire dolomite selon différentes compositions.
Ciment réfractaire d'aluminate
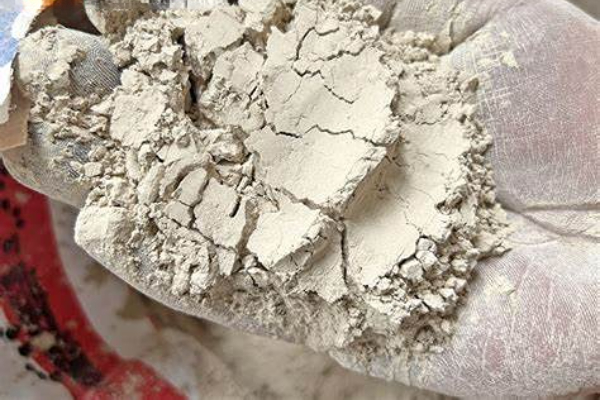
Le ciment réfractaire d'aluminate est un ciment réfractaire qui est généralement mélangé et broyé en 4 parties (en masse) de clinker de ciment réfractaire à faible teneur en aluminate de calcium et 1 partie de clinker de ciment à haute teneur en alumine. Comparé au ciment réfractaire à faible teneur en aluminate de calcium: la force initiale est plus élevée, le degré réfractaire est proche, et l'utilisation est la même.
Ciment réfractaire à faible teneur en aluminate de calcium
Le ciment réfractaire d'aluminate à faible teneur en chaux est un ciment d'aluminate fabriqué à partir de bauxite et de calcaire de haute qualité dans une proportion appropriée., fritté et rectifié. Sa composition est généralement: l'oxyde d'aluminium représente 70%, l'oxyde de calcium représente 19% à 23%, dioxyde de silicone <4%, oxyde de fer <1.5%. La composition minérale est principalement du disaluminate de calcium, comptabilité 60% à 70%, et le caractère réfractaire est supérieur à 1650°C. Comparé au ciment à haute teneur en alumine, les principales différences sont: teneur élevée en alumine, faible teneur en oxyde de calcium, faible résistance initiale, et caractère réfractaire élevé. Il peut être formulé en béton réfractaire ou en mortier réfractaire avec des granulats réfractaires (comme la bauxite calcinée, fragments de briques à haute teneur en alumine, etc.) avec une température réfractaire supérieure à 1770°C, et peut être utilisé comme revêtement de fours rotatifs à ciment et d'autres fours industriels.
Ciment d'aluminate de calcium et de magnésium
Le ciment d'aluminate de calcium et de magnésium est un ciment d'aluminate fabriqué à partir de bauxite et de dolomite de haute qualité dans une proportion appropriée., fritté et rectifié. La composition du ciment d'aluminate de calcium et de magnésium est généralement: l'alumine représente 66% à 74%, l'oxyde de calcium représente 13% à 18%, et l'oxyde de magnésium représente 10% à 13%. Des traces de dioxyde de silicium et d'oxyde de fer. La composition minérale est composée d'aluminate de calcium et de désaluminate de calcium représentant 45% à 60%, et la comptabilité spinelle pour 35% à 50%. Le caractère réfractaire est supérieur à 1650℃.
Comparé au ciment d'aluminate à faible teneur en calcium, le ciment d'aluminate de calcium-magnésium présente les avantages suivants: forte résistance à l'érosion chimique des scories et des métaux fondus; lorsque la teneur en alumine est la même, en raison de la présence de spinelle, Le caractère réfractaire est élevé; l'eau de gâchage est moindre, la porosité est faible après durcissement du ciment, et le retrait de calcination est faible; la perte de résistance lorsqu'elle est chauffée à 1 100 °C et déshydratée est faible. Le ciment d'aluminate de calcium et de magnésium, le corindon blanc fondu et d'autres agrégats sont formulés en béton, qui peut être utilisé comme revêtement de fours rotatifs à ciment et autres fours industriels.
WeChat
Scannez le code QR avec wechat