Introduction au processus de production de briques réfractaires en argile
La brique réfractaire en argile est un matériau réfractaire couramment utilisé, largement utilisé dans les fours industriels à haute température tels que l'acier, verre, ciment, et céramique. Il présente une excellente résistance aux chocs thermiques, résistance à haute température, et stabilité chimique. Cet article présentera en détail le processus de production de briques réfractaires en terre cuite pour aider chacun à mieux comprendre cet important matériau réfractaire..
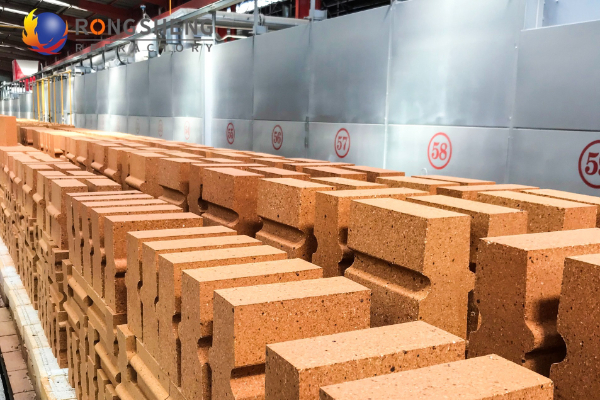
Processus de production de briques réfractaires en argile
① Préparation des matières premières
Principalement la préparation du clinker et la préparation de l'argile de liaison. La préparation du clinker consiste à calciner la matière première d'argile réfractaire à haute température en clinker., puis écraser, écran, et pulvérisez-le en différents niveaux de matériaux granulaires et de poudre fine. La préparation de l'argile de liaison consiste à broyer, sec, pulvériser finement, et mettre l'argile en bouillie. Le clinker d'argile est grossièrement broyé en blocs de moins de 50 mm, puis broyé en différents niveaux d'agrégats de 5 à 2 mm.. Le matériau tamisé entre dans la machine pour être broyé en poudre fine de moins de 0,5 mm. L'argile de liaison est généralement séchée, puis grossièrement écrasé, pulvérisé, et finement pulvérisé en poudre fine de moins de 0,5 mm, ou mélangé avec du clinker pour obtenir une poudre fine.
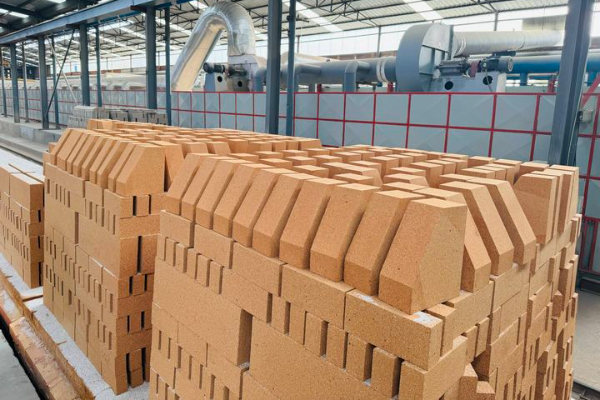
② Mise en lots et mélange
Traitement par lots, mélange, et moulage: Le clinker d'argile réfractaire calciné est utilisé comme matériau maigre, et une certaine proportion d'argile liante est ajoutée pour faire un mélange. Le clinker représente une forte proportion du mélange, ce qu'on appelle un produit multi-clinker. Ce type de produit présente une stabilité de volume élevée et d'autres bonnes propriétés, mais il doit être fortement moulé. Maintenant, les briques multi-clinker sont les produits les plus largement fabriqués et utilisés. Le mélange est moulé après mélange ou après avoir été piégé puis mélangé. Il existe de nombreuses méthodes de moulage, mais la méthode de moulage par pressage semi-sec est actuellement utilisée pour les produits multi-clinker. La pression de moulage a un impact sur la densité, résistance structurelle, et résistance aux scories des briques.
La proportion de boue comprend le rapport massique et le rapport particulaire entre le clinker, argile liante, eau, et additifs. La quantité d'argile liante et d'eau ajoutée varie selon le mode de moulage.. Le rapport de moulage du plastique est: mâchefer: l'argile est (7-5): (3-5), et la teneur en eau est 16%-20%; le rapport de moulage semi-sec est: mâchefer: l'argile est (9-7): (1-3), et la teneur en eau est 3.5%-8.0%. Divers matériaux granulaires sont ajoutés en séquence à l'équipement de mélange, et divers liants sont ajoutés pour faire une boue uniforme.
③ Séchage des briques réfractaires en argile
La teneur en humidité des ébauches de briques en terre cuite séchées varie en fonction de la méthode de moulage.. Le moulage par pressage semi-sec a une faible teneur en humidité dans les flans. Quand l'humidité s'évapore, il n'y a presque pas de retrait. Il peut être séché rapidement ou directement chargé dans le four. Les ébauches de briques à haute teneur en humidité peuvent être séchées au préalable par un séchage à l'air naturel approprié ou par un chauffage à l'air chaud, puis envoyées au four tunnel.. Le facteur clé dans le contrôle du processus de séchage est la vitesse de séchage.. Le principe doit être de s'assurer que les flans ne se déforment pas, fissure, et avoir une certaine force. La teneur en humidité des ébauches qui entrent finalement dans le four de cuisson est contrôlée pour être inférieure 2%.
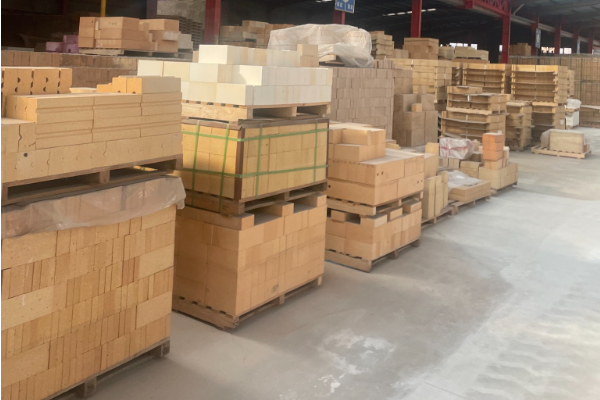
④ Cuisson des briques en terre cuite
Le but de la cuisson est de fritter les briques pour leur donner certaines dimensions, porosité et densité, haute résistance mécanique, bonne stabilité du volume, et bonne résistance au feu. Pendant le processus de cuisson, la matrice des briques subit une série de changements physiques et chimiques, et diverses réactions sont effectuées dans le courant descendant ou le tunnel. Le processus de cuisson est grossièrement divisé en quatre étapes.
- Lorsque la température atteint 200 ℃, la température ne doit pas être augmentée trop rapidement pour éviter que le corps vert ne se fissure. Lors de la cuisson dans un four tunnel, la température du premier 4 les places de stationnement ne doivent pas dépasser 200°C.
b.200-900℃ L'augmentation de la température doit être accélérée à ce stade pour faciliter la réaction chimique de la matière organique et des impuretés dans la billette. Pendant la période de 600 à 900 ℃, une forte atmosphère oxydante doit être maintenue dans le four pour éviter l'apparition de “noyau noir” briques de rebut. - 900-1380℃: (L'augmentation de la température doit être stable pendant la phase de haute température, et l'atmosphère d'oxydation doit être maintenue pour garantir que le corps de brique est chauffé uniformément et pour éviter la fissuration du corps de brique.. Parce qu'à des températures élevées supérieures à 1100 ℃, le retrait au frittage est très fort, et le taux de retrait atteint 5%, il est donc très important de maintenir un gradient de température doux et d'éliminer les contraintes internes.
- La température coupe-feu des briques en terre cuite est généralement supérieure de 100 à 150 ℃ à la température de frittage. Si la plage de température de frittage de l'argile frittée utilisée est étroite, la température coupe-feu doit être inférieure, environ 50-100 ℃ est plus approprié. La température de cuisson des produits en argile Il convient de s'assurer que l'argile liante est complètement ramollie afin qu'elle puisse réagir pleinement avec la poudre fine de clinker et la couche superficielle de particules grossières pour atteindre l'objectif de lier les particules de clinker et de faire en sorte que le produit obtienne une résistance et une résistance appropriées. stabilité du volume. La température de cuisson est généralement de 1 250 à 1 350 ℃. Si la teneur en A1203 est élevée, la température de cuisson du produit doit être augmentée de manière appropriée, environ 1350-1380°C, et le temps de conservation de la chaleur de cuisson est généralement 2-10 heures pour garantir que la réaction dans le produit est suffisante et que les qualités de surface et intérieures du produit sont cohérentes.
- Pendant la phase de refroidissement, selon les changements de réseau du produit dans la section de refroidissement, la température doit être augmentée rapidement à des températures élevées supérieures à 1000°C, et la vitesse de refroidissement doit être ralentie à 1000-800°C. En fait, en production réelle, la vitesse de refroidissement effectivement adoptée n'entraînera pas de risque de fissuration à froid du produit.
WeChat
Scannez le code QR avec wechat