Three important properties of magnesite iron spinel refractory brick
Magnesia-iron spinel refractory brick is one of the important products in the refractory industry. This spinel material obtained by modification of iron elements not only retains the advantages of traditional magnesium-aluminum spinel, but also develops new properties that are more adaptable to harsh working conditions.

Corrosion resistance of magnesia-iron spinel refractory brick
The magnesium oxide in the magnesia-iron-aluminum spinel brick reacts with iron oxide, iron spinel, and aluminum spinel to form uneven pores and fine crack structures locally, forming a highly direct bonding structure between crystals; MgO and Al2O3, Fe2O3 or FeO of the iron-aluminum spinel are more likely to react, forming a mutual diffusion phenomenon, and at the same time forming the formation of secondary spinel, a dense layer with a high Fe content will be formed around the iron-aluminum spinel particles. The formation of secondary spinel after sintering also enhances the compactness of the magnesia-iron-aluminum composite spinel brick; the direct bonding between magnesia sands and the chemical stability of the iron-aluminum spinel are the strong resistance to silicate melt penetration and salt-alkali erosion of the magnesia-iron-aluminum composite spinel brick.
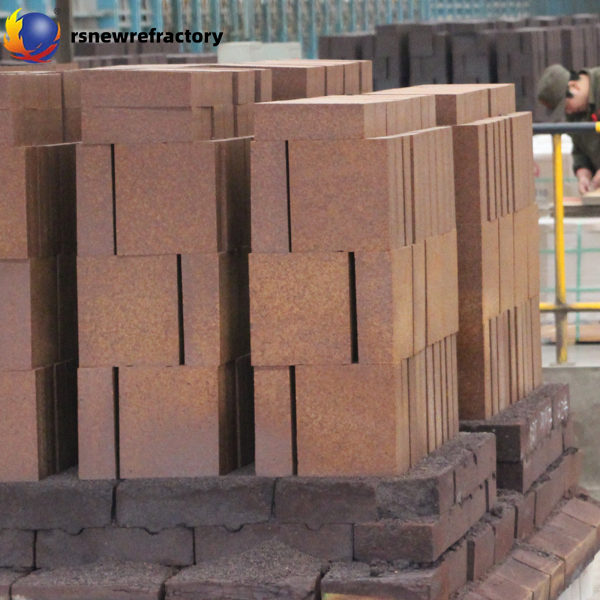
During the production and use of magnesia-iron-aluminum spinel bricks, the generated spinel has good erosion resistance, and the liquid phase in the cement clinker is mainly C4AF and C3A. During the cement production process, the first component of the clinker that penetrates into the interior of the brick is mainly C4AF. At the same time, when the liquid phase in the clinker enters the surface of the brick, the liquid phase reacts with the chemical composition of the brick to first form a high-temperature refractory layer, which prevents further penetration of the liquid phase and improves the ability to resist clinker erosion.
Kiln skin performance
The process of kiln skin formation is that when the kiln temperature reaches a certain value, the kiln material produces melt and reacts with the surface of the refractory bricks, penetrates into the bricks through the pores of the bricks, and the infiltrate enters the bricks and solidifies at a position below 1200℃, producing a “mechanical anchoring” effect. This stage is the initial adhesion and fixation stage of the kiln skin. On this basis, the upper kiln skin is bonded with the clinker particles, and the kiln skin gradually thickens. When the kiln skin thickens to a certain value, it reaches a dynamic balance and stops thickening to form a kiln skin. When the kiln operation process changes (especially when the kiln is stopped), the kiln skin will fall off when the gravity of the kiln skin is greater than the “anchoring force” of the kiln skin on the bricks, causing damage to the lining bricks. Kaya nga, the “anchoring force” of the kiln skin on the lining bricks is of great significance to the stability of the kiln skin. In order to make the kiln skin and the lining bricks firmly bonded, in addition to the chemical composition of the refractory bricks, the organizational structure of the bricks is also very important. There should be a certain amount of evenly distributed pores to facilitate the penetration of the kiln material melt to form a “mechanical anchoring”.
During normal calcination, the kiln charge is a liquid phase with C3A-C4AF as the main component, so the chemical composition of the kiln charge has an important influence on the stability of the kiln lining. The higher the content of AI2O3+Fe2O3 in cement clinker (i.e., the lower the silicate rate and the higher the temperature), the more melt there is. Al2O3 and Fe2O3 have different effects on the amount of melt formation and melt viscosity. The relationship between the temperature and the cement clinker melt with different relative contents of Al2O3 and Fe2O3 (i.e., alumina rate) is shown. When A/F=1.38, a liquid phase appears at 1280℃, and more melt can be formed at a lower temperature (1300°C), and the amount of melt does not change much in a wider temperature range (to 1450℃), which is more conducive to the adhesion of the kiln lining.
Magnesia-iron-aluminum spinel bricks contain magnesia-iron-spinel, iron-aluminum spinel and magnesia-aluminum spinel. MgO and Al2O3, Fe2O3 or FeO in cement clinker are easy to react and form mutual diffusion. This diffusion allows part of the components in the magnesia-iron-aluminum spinel bricks to enter the clinker melt, and part of the clinker melt will also invade the reaction layer of the magnesia-iron-aluminum spinel bricks. This chemical reaction makes the magnesia-iron-aluminum spinel bricks and cement clinker organically combined into a mutually fused whole. This mutual diffusion and fusion will also form the formation of secondary spinel, forming uneven pores and fine structures locally, increasing the penetration of cement clinker into refractory materials and improving the performance of the kiln skin.
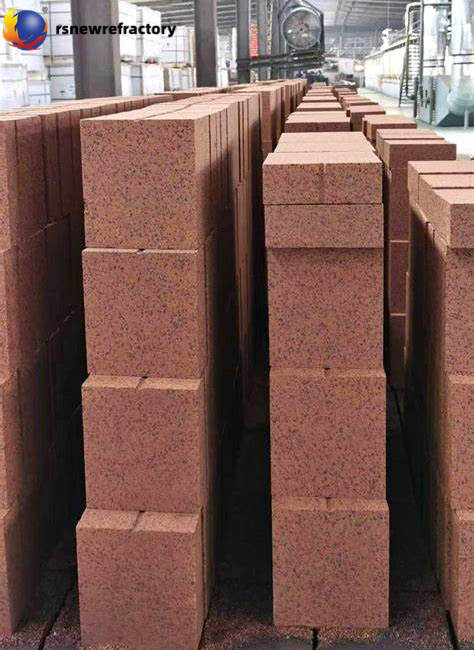
Thermal shock resistance of magnesia-iron spinel bricks
Ferroaluminum spinel has the characteristics of a small thermal expansion coefficient and high thermal conductivity, which can significantly reduce the thermal stress of magnesia-ferroaluminum spinel bricks. Magnesia-ferroaluminum spinel bricks contain periclase, ferroaluminum spinel, magnesia-ferro-spinel, magnesia-aluminum spinel, and other materials. Due to the different thermal expansion coefficients of various phases, a large number of microcracks exist inside the material during the firing process, thereby increasing the toughness of the material. Kaya nga, magnesia-ferroaluminum spinel bricks have good flexibility and thermal shock resistance.
WeChat
Scan ang QR Code sa wechat