Paano mo baguhin ang refractory ceramic ball?
Refractory ceramic ball is an important refractory material, commonly used in high-temperature industrial equipment, such as heating furnaces, hot blast furnaces, and reactors. They have excellent high-temperature resistance, thermal shock resistance, and corrosion resistance, and can maintain stability and durability in extreme environments. The main function of refractory bola is to help uniform heat transfer inside the equipment while protecting the lining material and extending the service life of the equipment. In practical applications, refractory balls need to be replaced regularly to ensure their performance and the normal operation of the equipment.
Replacement steps of refractory ceramic balls
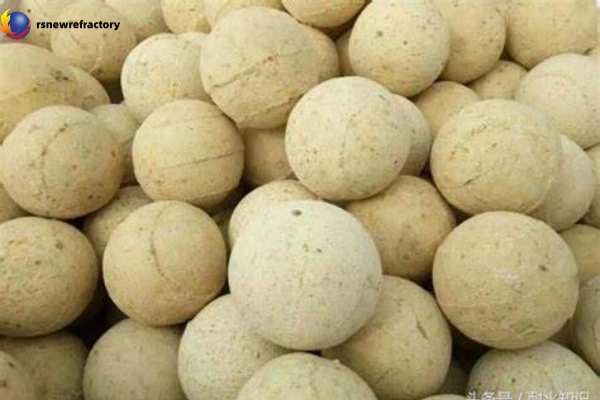
Ball unloading work
After forced cooling of the furnace, the blind plates of the hot air valve, gas valve, flue valve, and exhaust valve are inserted and the water pipes are connected in place. After the furnace is cooled, the two manhole covers for unloading balls are removed and the ball chute is installed. The brickwork in the unloading hole is removed to unload the balls. If there is a blockage, use a rake to manually remove the balls in the ball-holding hole. When the balls are unloaded halfway, there are large pieces of φ40 clay and φ60 high-aluminum refractory balls, and the ball bed surface in the furnace drops to the lower edge of the middle manhole. The bed surface is a large piece of bonding, and the ball wiping hole is also blocked by a large piece. It is necessary to enter the middle manhole for processing and break the large pieces before unloading the refractory ceramic ball.
Broken chunks of glue
Open the bottom manhole fan to exhaust the hot air furnace body to form negative pressure on the upper part of the furnace body and draw in cold air to reduce the temperature near the ball-loading manhole. The construction manager can enter the furnace body only after filling in various relevant confirmation documents. Hang a thin steel wire rope buckle from the thermocouple hole on the arch. After entering, stand on the agglomerate and tie the safety belt to the thin steel wire rope buckle. At the same time, tighten the thin steel wire rope buckle to prevent the agglomerate from collapsing and causing injuries to personnel. Regularly measure the oxygen content and temperature in the furnace, break the agglomerate with a pneumatic pick, clear the block falling channel with a poking chisel, and manually use a rake to pick up the broken balls in the volleyball hole. After unloading the balls, clear and clean the grate channel, then brick the ball unloading manhole and close the manhole cover.
Installation of refractory ceramic ball
Install a chute in the middle manhole, use a crane to lift the new balls into the wine tank and load them into the furnace. When the refractory ball ring is added to the lower edge of the middle manhole, stop adding balls to the middle manhole, and close the manhole with bricks and manhole covers. Start loading balls in the arch manhole. When the refractory balls are loaded to the specified height or when the variety is changed, enter the furnace to level the top of the pile before continuing to load the balls. After completion, level the surface of the refractory balls.
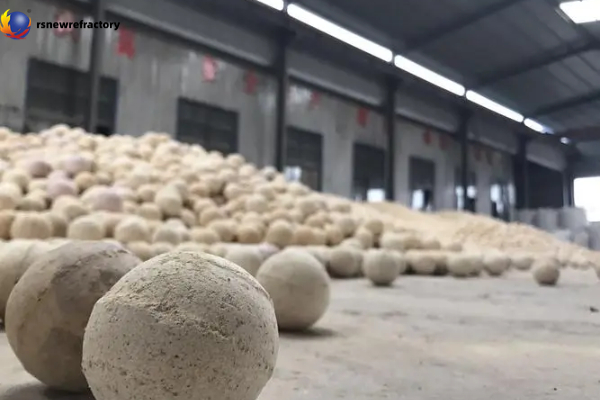
Baking furnace
Connect the coke oven gas hose and the burner: purge the gas from the coke oven gas pipeline, install thermocouples on the exhaust pipe of the bottom manhole to monitor the temperature of the oven flue, and install water cooling facilities. Open the combustion fan on the bottom manhole to exhaust, put the burner into the upper manhole to start baking, switch the coke oven gas valve, adjust the dome temperature, and control the flue temperature according to <3℃Ch. The baking furnace is based on the principle of slow in the early stage and fast in the later stage. The manhole is closed when the dome is above 750℃, and the blast furnace gas is used to bake the furnace. The bottom exhaust pipe is removed, the flue blind plate is removed, and the flue is replaced with normal flue gas. When the dome temperature is baked to 950℃, the furnace is burned normally and put into production.
Adjustment of air supply operation during the blast furnace operation rest period
After the hot blast furnace is baked, the self-plates of the hot blast valve, gas valve, flue valve, and exhaust valve are removed, the pipeline connection is sealed and then the air tightness is tested by stamping. After the test is passed, the furnace will be burned normally to a constant temperature of 1050°C on the dome, and the blast furnace duty room will be notified when the flue temperature reaches 320°C.
WeChat
Scan ang QR Code sa wechat