Ang papel na ginagampanan ng anchor fire brick sa paggamit ng mga refractory castables
Refractory castables are a widely used material in high temperature industrial applications, especially in industries such as smelting, ceramics, and glass. In order to improve the performance and stability of castables, anchor fire bricks are introduced as key components.
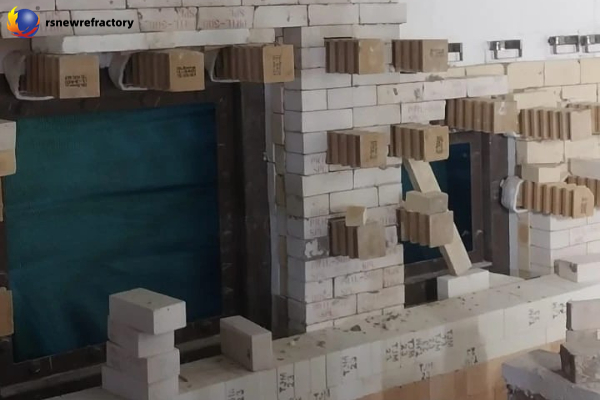
Ang papel na ginagampanan ng anchor fire brick sa paggamit ng mga refractory castables
Anchor bricks play the role of skeleton in refractory castables. So anchor bricks are also called hanging bricks. There are three products that play the role of the skeleton in the use of refractory castables: one is anchor bricks, the other is anchors, and the third is tortoiseshell nets. Anchors and tortoise shell nets are both metal products, and only anchor bricks are refractory products.
Size and shape of anchor fire bricks
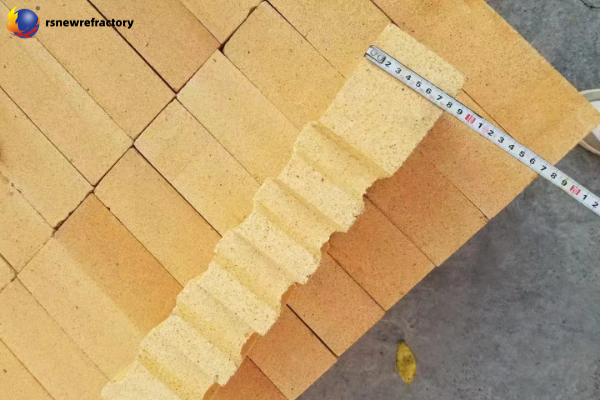
There are many shapes and connection methods for anchoring fire bricks, and their sizes are different. Generally, they are made according to user customization. There are also some regular lengths of 330, 380, 440, and 500m. The thickness is generally around 100mm. The function of anchoring bricks is to enhance the strength of the refractory castable lining.
Anchoring bricks are divided into those with holes and those without holes. The use of those with holes and those without holes is different from the use of furnace roofs and furnace walls. They are used to be embedded in the castable and hung with hanging parts, so they can also be called hanging bricks.
Anchor nail introduction
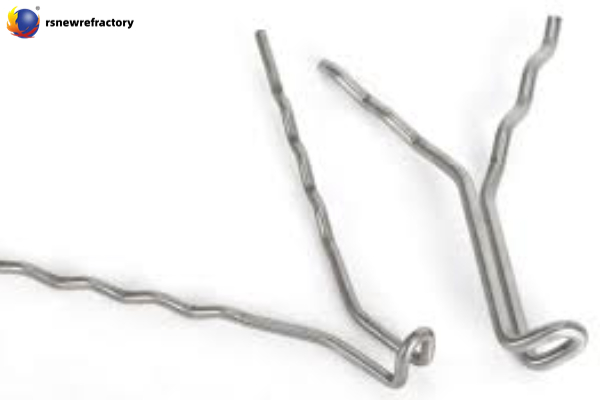
The anchor is directly welded on the furnace shell. When the refractory castable is poured, the anchor is buried in the lining to anchor and connect. The most commonly used ones are Y, V, and L shapes. The height is determined according to the thickness of the refractory castable. If the thickness of the castable is 200mm, the height of the anchor can be 160-180mm. The anchor is very easy to oxidize at high temperatures. When buried in the castable lining, it should be determined according to the thickness of the lining and the use temperature.
Production of anchor bricks
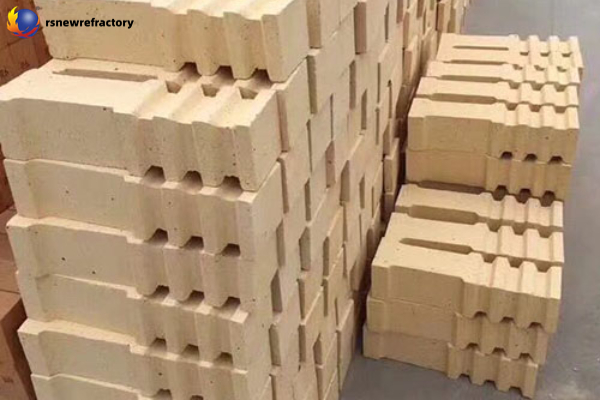
Anchor refractory bricks are refractory bricks that are made by mixing raw materials, molding, and sintering. They have high strength, good thermal shock stability, and toughness. However, the mold of anchor bricks is a difficult point in the production process. The mold is complex and difficult to make, and the mold cost is much higher than that of general refractory bricks.
If the anchor brick has a hole, the installation hole is generally at the neck. The finished anchor brick must not have cracks and the size must be accurate. It is convenient to use on the furnace top. Anchor bricks generally use grade 3 high aluminum more, because grade 3 high aluminum anchor bricks are tough. Although the first-grade high aluminum bricks have good quality, the hardness also increases. When used in general castables, cracks are prone to occur.
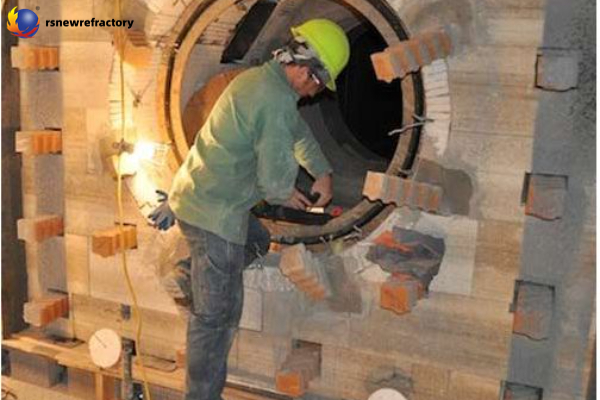
WeChat
Scan ang QR Code sa wechat