Tipos y características de incineradores de basura.
Los incineradores de basura son un tipo de equipo para el tratamiento de residuos sólidos.. Quema la basura hasta convertirla en cenizas y humo a altas temperaturas., reduciendo así el volumen de basura y eliminando sustancias nocivas. Los siguientes son varios tipos comunes de incineradores de desechos..
Cinco tipos de incineradores de basura
Incinerador tipo parrilla
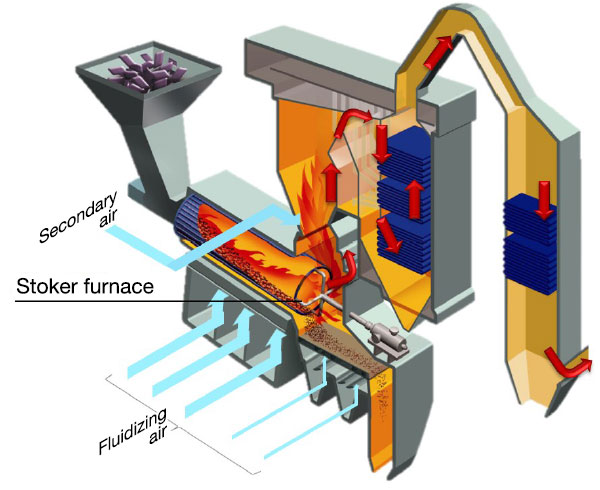
El incinerador tipo parrilla funciona continuamente y puede procesar más de 200 toneladas de residuos por día. Está equipado con una rejilla de horno en la parte inferior., y los residuos se suministran a través de la tolva superior. Los residuos a quemar se colocan en la parrilla del horno., y el aire de combustión se inyecta desde la parte inferior del horno para su secado e incineración directa.. Cuando se utiliza un incinerador tipo parrilla para la eliminación de desechos, Generalmente no es necesario clasificar o triturar los residuos., excepto artículos grandes. La temperatura superficial de la capa de residuos puede alcanzar hasta 800°C., y el rango de temperatura de los gases de combustión está entre 2800 y 1000°C. El incinerador tiene una sola cámara de combustión., asegurando una combustión confiable, buen aprovechamiento del calor residual, rendimiento de combustión estable, y una alta tasa de agotamiento. Los residuos sólidos permanecen en el horno durante aproximadamente 1 a 3 horas, mientras que los gases permanecen sólo unos segundos. Este tipo de incinerador es alto y delgado., con un gran volumen. Requiere técnicas operativas avanzadas., tiene un costo mayor, y la parrilla debe soportar altas temperaturas., y corrosión, y tener buenas propiedades mecánicas, o puede ser propenso a sufrir daños.
CAO (Oxidación controlada del aire) sistema de incineración
La CAO (Oxidación controlada del aire) El sistema de incineración es un nuevo tipo de incinerador de residuos con una capacidad de procesamiento de hasta 150 toneladas por día. Sus características clave incluyen un proceso de dos etapas.: primero, Los residuos sufren descomposición por oxidación térmica., seguido de gasificación y combustión.. Esto da como resultado una combustión estable con una alta eficiencia de combustión.. Sin embargo, el proceso de combustión es lento, y exige un control preciso de los niveles de oxígeno y las temperaturas del horno.. Si los residuos tienen alto contenido de humedad y carecen de ignición asistida por aceite., Es posible que no se logre una combustión estable.. El sistema consta de dos cámaras de combustión.: Los residuos sólidos permanecen en la primera cámara. (a temperaturas de 600-800°C) por aproximadamente 3-6 horas, mientras los gases pasan por la segunda cámara (a temperaturas de 800-1000°C) durante aproximadamente 1-3 artículos de segunda clase, impulsado por una hélice.
Incinerador de lecho fluidizado
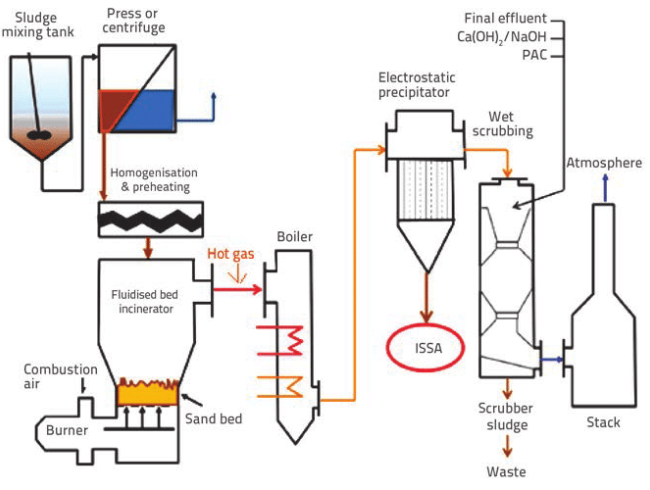
El incinerador de lecho fluidizado está formado por placas de distribución porosas.. Se añade una gran cantidad de arena de cuarzo al horno., calentado a más de 600°C, y aire caliente (por encima de 200°C) es soplado desde abajo, haciendo que la arena hierva. Entonces, se introducen los residuos. Los residuos hierven junto con la arena caliente., secarse rápidamente, encendido, y quemado. Antes de entrar al horno, los residuos deben clasificarse y triturarse (10-30centímetro). dentro del horno, sufre combustión suspendida. Este proceso de alta eficiencia conduce a una quema completa.. Sin embargo, La capacidad de procesamiento de residuos del incinerador se limita a menos de 150 toneladas por día. La temperatura dentro del horno es uniforme., y la tasa de combustión es relativamente rápida. Los residuos sólidos permanecen en el horno durante 1-2 horas, mientras los gases permanecen en el horno sólo unos segundos.
Incinerador de residuos industriales de horno rotatorio
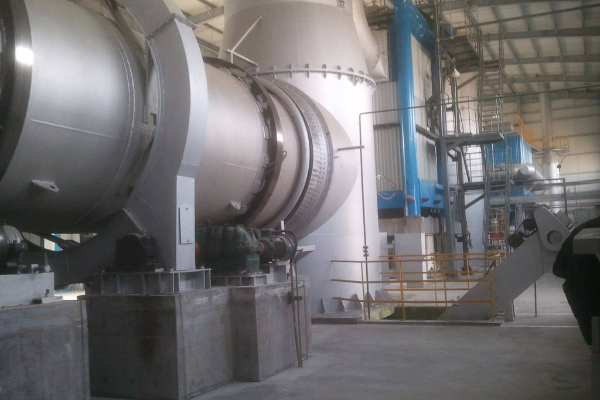
El incinerador de horno rotatorio consta de un horno rotatorio, dispositivo de alimentación de residuos, cámara de combustión secundaria, y quemador, y está equipado con una parrilla de horno en la parte trasera para la incineración secundaria. Este tipo de horno rotatorio es adecuado para procesar residuos a gran escala y residuos industriales. (como lodos, residuos de pintura, plástica, etc.) sin necesidad de clasificación previa ni trituración de los residuos. Tiene una capacidad de procesamiento de más 200 toneladas por día. Los residuos sólidos permanecen en el horno rotatorio durante 2-4 horas a una temperatura de aproximadamente 900°C. La temperatura en la cámara de incineración trasera está entre 1000-1200°C.. Las partículas de ceniza resultantes después de la incineración son pequeñas., y la eficiencia de quemado es relativamente alta.
Características de cuatro tipos de incineradores de basura.
De los cuatro tipos anteriores de incineradores de residuos, Se puede observar que los incineradores de residuos convencionales generalmente funcionan a temperaturas de combustión relativamente bajas., normalmente por debajo de 1000°C. Como resultado, Es posible que algunos materiales combustibles no experimenten una combustión completa.. Componentes de residuos peligrosos, como los que se encuentran en los desechos médicos, no están completamente procesados, que puede afectar negativamente la calidad local del suelo y del agua, lo que lleva a una contaminación ambiental secundaria. Además, La incineración a baja temperatura puede generar dioxinas que son perjudiciales tanto para el medio ambiente natural como para la salud humana.. Garantizar una combustión integral y lograr cero emisiones de dioxinas, Se han empleado muchas tecnologías avanzadas en el tratamiento de residuos sólidos desde la década de 1980.. Estos incluyen métodos ultrasónicos., técnicas de gasificación-fusión, Enfoques de combustibles derivados de residuos., y tecnologías de oxidación fotoquímica..
Gasificador de plasma
En comparación con las técnicas de combustión tradicionales., La tecnología de plasma ioniza el aire., alcanzando temperaturas de 3000°C a 10000°C en una fracción de segundo. Esta alta temperatura hace que las sustancias tóxicas se descompongan rápidamente., prevenir la formación de dioxinas. Los gases peligrosos y los metales pesados se vuelven inofensivos tras el tratamiento en el horno de plasma.. Cuando los residuos se introducen en el horno de gasificación por plasma., Los residuos orgánicos sufren una rápida deshidratación., pirólisis, y descomposición, produciendo una mezcla de gases combustibles compuesta principalmente de H2, CO, y algunos gases orgánicos. Este se somete además a una combustión secundaria para lograr la reducción y la inocuidad.. Materiales inorgánicos (como metales, vaso, etc.) derretirse bajo el plasma de alta temperatura, logrando la reducción. Comparado con la combustión tradicional, La tecnología de plasma proporciona un tratamiento más exhaustivo de residuos peligrosos., generando un residuo cristalino que no supone ningún peligro y puede utilizarse en materiales de construcción sin necesidad de entierro. A través de este proceso, El volumen de residuos se reduce significativamente., Las sustancias tóxicas se descomponen., y las cenizas de incineración forman escoria de vidrio., transformándose en material inofensivo. La tecnología de plasma para residuos de alto riesgo es tendencia en el tratamiento de residuos peligrosos.
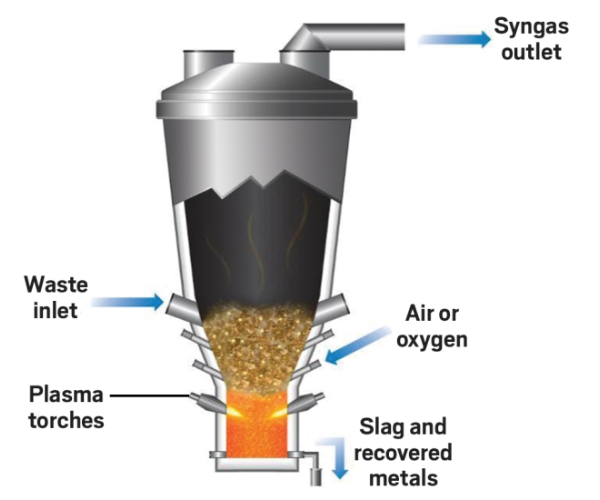
El rango de temperatura de trabajo del horno de gasificación por plasma es de 1200°C a 1700°C., con temperaturas cerca de la antorcha de plasma que alcanzan hasta 1700°C. Esta alta temperatura instantánea impone requisitos exigentes a la resistencia del material refractario al estrés térmico.. El proceso implica una intensa radiación térmica., provocando un rápido calentamiento de la superficie del material refractario, lo que resulta en gradientes de temperatura significativos y estrés térmico. Además, La gasificación de residuos produce una gran cantidad de vapor de agua., cual, al levantarse, Puede corroer gravemente el material refractario del revestimiento superior del horno..
WeChat
Escanea el código QR con wechat