Comparison of refractory bricks and refractory insulating castable in use
Refractory materials are widely used in the thermal industry. The proportion of refractory insulating castable is growing continuously, but πυρίμαχα τούβλα still occupy a certain position. The following is a comparison between refractory bricks and refractory castables in use.
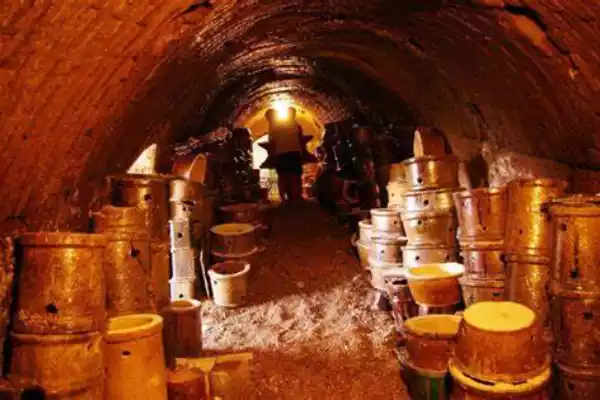
Why are refractory bricks more widely used?
Functional refractories play a role in controlling steel flow during continuous steel casting. In other application fields, high-quality refractory castable materials have not yet been developed, so refractory brick products are still the first choice. In most occasions where basic refractory linings are used (dolomite, magnesia, magnesia carbon, magnesia chrome), refractory brick products are preferred. Για παράδειγμα, the inner lining of the converter, the slag line brick of the ladle, the furnace wall of the electric furnace, the firing zone and transition zone of the cement rotary kiln, the lining of the smelting non-ferrous metal (χαλκός, lead, zinc, και τα λοιπά.).
Application of refractory castable
Refractory insulating castables are not only used to manufacture new unshaped refractory linings but also are widely used for repairing and maintaining refractory linings in service. There are various construction methods for refractory castables, including vibrating and non-vibrating (self-flowing) pouring, gunning, ramming, and pressing. – Some construction methods have become and will continue to be the leading construction methods of refractory castables. According to the traditional method, refractory insulating castable is used as the bottom of the traditional electric arc furnace (basic refractory), gun mud, blast furnace tapping trough, and some repair and maintenance materials. On some occasions, products with complex shapes have been replaced by unshaped refractory materials, thus producing composite linings. Waste incinerators are an example.
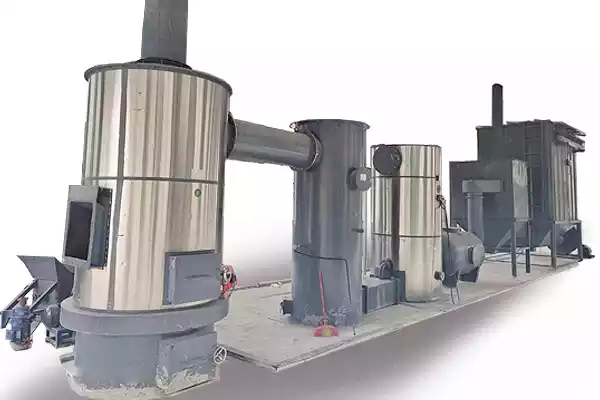
Refractory castables for kiln maintenance
Refractory castables play an important role in kiln maintenance because extensive repairs can be achieved with minimal downtime, and in some cases, while the kiln is in operation. Systematic repairs to the lining can prolong the service life of the kiln. The repair of an oxygen-blown alkaline lining (MgO-C brick) is a successful example. Using alkaline mixed materials for regular spraying and precisely controlling the formation of slag, slag splashing for furnace protection can increase the life of the inner lining to more than 2000 furnace times, while the consumption of refractory materials per ton of steel can be reduced to less than 1Kg.
Problems with refractory insulating castable
Although the construction of refractory castable is simple, it often cracks when it is used.
Advantages of refractory castables over refractory bricks
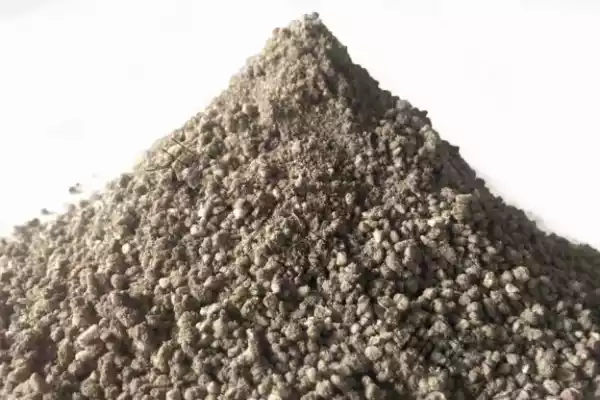
- Less energy consumption during production, only 1/15~1/20 of refractory bricks.
- The labor rate is low, and the production efficiency during use is 3~8 times higher than that of refractory bricks.
- The finished refractory castable is easy to store and transport.
- It can realize mechanized furnace building. The construction efficiency is 5 να 15 times higher than that of bricklaying.
- It can be arbitrarily shaped and made into an integral lining, which can increase its service life by 30%~150%, and some can be as high as several times.
- Την ίδια στιγμή, there is no seam, good air tightness, less heat loss, and can greatly save energy.
- It can repair the kiln, prolong its service life and improve the furnace operation rate.
Comparison of refractoriness between refractory bricks and refractory castables
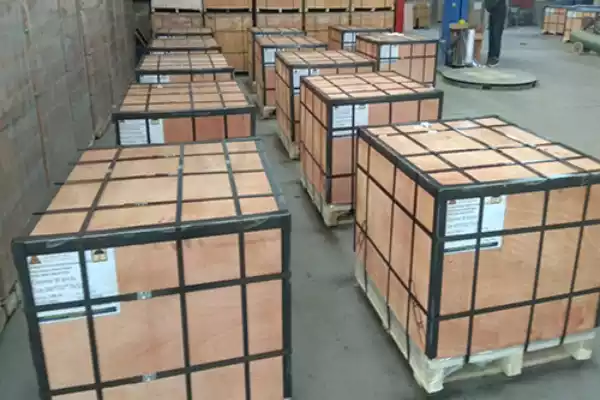
When preparing refractory bricks, there is not much difference in the selection of raw materials when preparing refractory castables, except that refractory bricks are shaped refractory materials, while refractory castables are unshaped refractory materials. Επομένως, there is no difference between the refractoriness of refractory bricks and the refractoriness of refractory castables. Ωστόσο, it is precisely because refractory bricks are stereotyped refractory products. Relatively, refractory bricks have low creep performance, αντοχή στη φθορά, and refractory performance. The performance is better than that of refractory castables
WeChat
Σαρώστε τον κωδικό QR με το wechat