The construction method of ramming material
The ramming material is a bulk material made of silicon carbide, graphite, and electrically calcined anthracite as raw materials, mixed with various ultrafine powder additives, and fused cement or composite resin as a binder. It is used to fill the gap between furnace body cooling equipment and masonry or masonry leveling layer. The μάζα εμβολισμού has good chemical stability, αντοχή στη διάβρωση, and wear resistance.
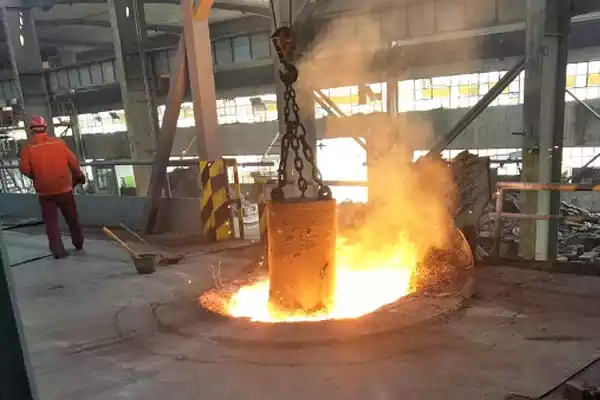
Classification of ramming materials
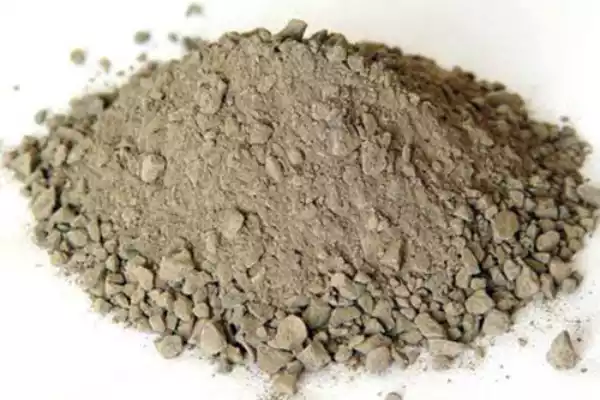
The ramming materials are classified by material: high alumina, clay, magnesia, dolomite, zirconium, and silicon carbide-carbon refractory ramming materials.
Characteristics of ramming material
Compared with other unshaped refractory materials of the same material, the ramming mix is dry or semi-dry and loose, and the dense structure can be obtained by strong ramming. Only when it is heated to the sintering temperature, the combination will have strength.
After the ramming mass is formed, different heating methods can be adopted to promote its hardening or sintering according to the hardening characteristics of the mixture. If it contains an inorganic chemical binder, it can be removed from the mold after hardening to a certain strength and baked; if it contains a thermoplastic carbon mixture, it must be cooled to a certain strength before demolding, and it should be heated quickly to make it coke before use; A binder that hardens at room temperature is often sintered with a mold after tamping.
How to use ramming mass?
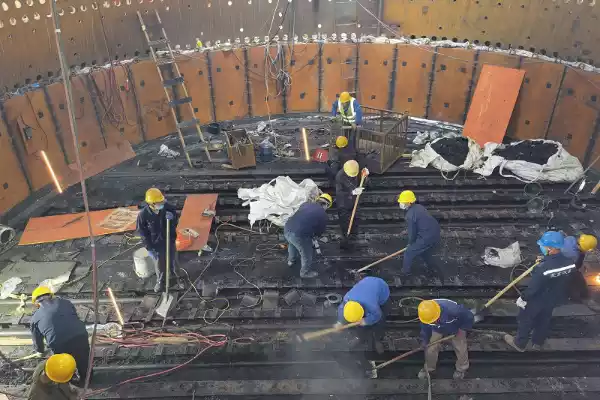
Preparation
- Clean up and inspect the construction area to ensure that the surface is flat, clean, and free of debris and old materials.
- Prepare the required construction tools and equipment, such as ramming machines, ramming sticks, καλούπια, και τα λοιπά.
Preparation of ramming material
- Accurately weigh and mix the required raw materials according to the formulation requirements of the ramming material.
- In the mixing equipment, mix the powdered raw materials, βιβλιοδέτης, and appropriate amount of water or wetting agent evenly until a uniform paste is obtained.
Construction Process
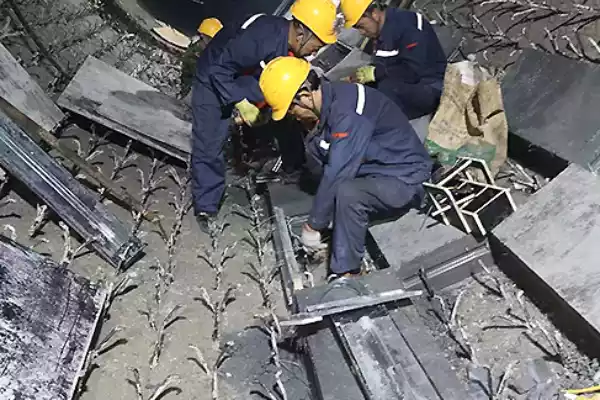
- Using a spatula or shovel, spread the ramming compound evenly on the surface of the construction area.
- Use a tamping stick or a tamping machine to tamp and compact the ramming mass. The purpose of ramming is to remove voids, increase compactness, and ensure that the ramming material is firmly bonded to the substrate.
- According to the needs, molds can be used during the construction process to shape parts of specific shapes or curves.
- Check the construction area to ensure that the thickness and uniformity of the ramming mass meet the requirements.
Curing and hardening
- After the construction is completed, the ramming mix should be cured and hardened to maintain suitable humidity and temperature conditions.
- According to the requirements of ramming mass, carry out proper drying or sintering treatment to improve its physical and chemical properties.
WeChat
Σαρώστε τον κωδικό QR με το wechat