Drehrohrofenstruktur und feuerfeste Produkte der Zementindustrie Einführung
Der Drehrohrofen ist ein kreisförmiger Zylinder, der in einem bestimmten Winkel geneigt ist (3~5°) und mit feuerfesten Materialien ausgekleidet. Der Durchmesser und die Länge des Drehrohrofens hängen mit der täglichen Lebensdauer des Drehrohrofens zusammen. Das Produktionsvolumen steht in direktem Zusammenhang.
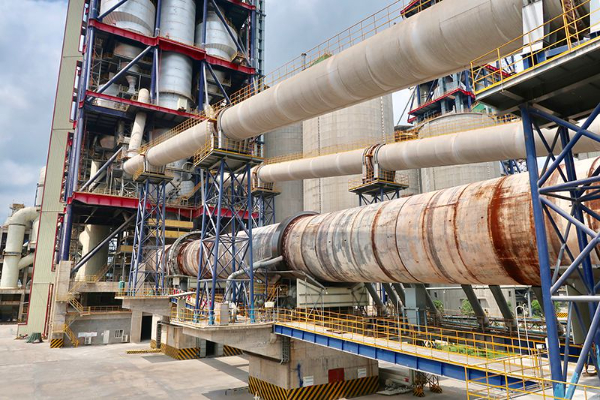
Betriebsstruktur eines Drehrohrofens
Der Drehrohrofen ist ein kreisförmiger Zylinder, der in einem bestimmten Winkel geneigt ist (3~5°) und mit feuerfesten Materialien ausgekleidet. Der Durchmesser und die Länge des Drehrohrofens hängen mit der täglichen Lebensdauer des Drehrohrofens zusammen.
Das Produktionsvolumen steht in direktem Zusammenhang.
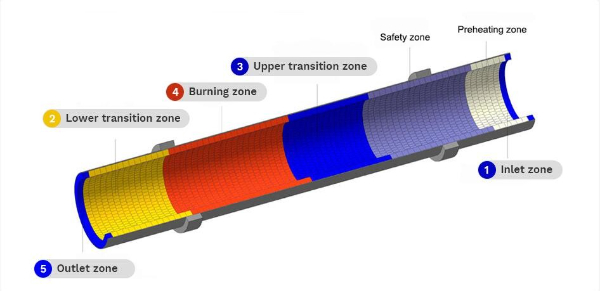
Zersetzungszone
Im neuen Trockenprozess-Zementofen, 90% des Rohmaterials wird in der Vorzersetzungsanlage außerhalb des Ofens zersetzt, und der Rest 10% wird in der Zersetzungszone im Drehrohrofen vervollständigt, hauptsächlich die Zersetzung von Calciumcarbonat.
Die Materialtemperatur in der Zersetzungszone beträgt 800–1000 °C, und die Gastemperatur beträgt 1000~1400°C. Die Hauptumgebungen, denen die feuerfesten Materialien im Ofen ausgesetzt sind, sind hohe Temperaturen, chemische Erosion wie Alkali, Schwefel, und Chlor, und mechanischer Stress, der durch die Rotation des Ofenkörpers verursacht wird. Feuerfeste Materialien für die Zersetzungszone müssen eine gute mechanische Festigkeit und Beständigkeit gegen chemische Angriffe wie Alkali aufweisen.
Zu den verwendbaren Materialien zählen vor allem Spinellsteine, Abplatzungssichere Ziegel mit hohem Aluminiumoxidgehalt, Silizium-Molybdän-Steine, und Ziegel mit hohem Aluminiumoxidgehalt.
Obere Übergangszone
Befindet sich hinter der Zersetzungszone, Die Rauchgastemperatur im Ofen beträgt ca. 1700°C. Beeinflusst durch die Kraftstoffverbrennung, die Rauchgastemperatur ändert sich häufig. Die Ofenhaut in diesem Bereich hängt und fällt von Zeit zu Zeit. Die Auskleidung steht in direktem Kontakt mit Rauchgas und Klinker und ist einer starken thermischen Belastung ausgesetzt. Ändert sich häufig und ist anfällig für Klinkerabrieb, Hochtemperatur-Rauchgas, und Klinker
Die Erosion von Kohle-Alkali-Schwefelverbindungen und die Rundheitsbeanspruchung des Zylinders im Radriemenbereich.
Die obere Übergangszone muss hohen Temperaturen und der Erosion durch einen Teil der flüssigen Phase des Zementklinkers standhalten, und es muss auch eine gute thermische Festigkeit haben.
Zu den feuerfesten Steinen gehören üblicherweise Silica-Molybdän-Steine, Magnesia-Aluminiumoxid-Spinellsteine, und spezielle, abplatzungssichere Ziegel mit hohem Aluminiumoxidgehalt.
Schießzone
Im Teil des Ofens mit der höchsten Temperatur, Die Flammentemperatur kann bis zu 1800~2000℃ erreichen, und die Temperatur des Ofenmaterials kann 1350 bis 1400 °C erreichen. Es entsteht eine große Menge Zementklinker. Zum Schutz der Auskleidungssteine muss in diesem Teil eine stabile Ofenhaut gebildet werden. Zusätzlich, eine große Menge an Alkali- und Schwefelverbindungen im Ofenmaterial verflüchtigt sich, Daher müssen die Auskleidungssteine hängende Ofenhäute haben.
Leistung, Es widersteht der thermochemischen Erosion von Schmelzbestandteilen sowie Alkali- und Schwefelverbindungen in der Ofenhaut, Außerdem muss es der thermischen Schockbelastung und den Schäden am Ofen standhalten, die durch den Zusammenbruch der Ofenhaut entstehen.
Die mechanische Belastung durch die Körperrotation in der Schusszone ist hoch und die chemische Reaktion heftig. Das feuerfeste Material muss eine gute Hochtemperaturbeständigkeit aufweisen, Alkalibeständigkeit, und Zementklinkererosion. Gleichzeitig muss das feuerfeste Material hier ofenfest sein, um eine Schutzschicht auf der Auskleidungsoberfläche zu bilden. Allgemein, Zum Einsatz kommen Silica-Molybdän-Steine und Periklas-Spinell-Steine.
untere Übergangszone
Die Ofenauskleidungssteine in der unteren Übergangszone halten der thermischen Belastung durch Hochtemperaturluft und Klinker über 1400 °C stand und sind besser in der Lage, der Belastung durch staubige Hochtemperaturluftströmung und erstarrten Klinker standzuhalten.
Abrieb, Erosion durch die Schmelze im Klinker, Schmelze und Gas von Schwefel- und Alkaliverbindungen, Verformung des Hochtemperaturzylinders, und Ovalitätsspannung im Radriemen.
Die Temperatur in der unteren Übergangszone ist niedriger als die der Brennzone, und es gibt keinen stabilen Ofenhautschutz. Der Zementklinker ist stark erodiert und erodiert, und der Temperaturschwankungsbereich ist groß. Deshalb, Die feuerfesten Materialien in dieser Zone weisen nicht nur die hohe Feuerfestigkeit und hohe Belastung der feuerfesten Materialien in der Brennzone auf. Neben Erweichungstemperatur und hoher Festigkeit, Es sollte außerdem eine gute Temperaturwechselbeständigkeit und eine gute Haltbarkeit beim Aufhängen im Ofen aufweisen. Allgemein, Es werden rote Silizium-Molybdän-Steine und Periklas-Spinell-Steine verwendet.
Kühlzone
Die Kühlzone des neuen Trockenprozess-Zementdrehrohrofens ist ein ähnlicher Bereich wie die untere Übergangszone. In diesem Bereich kühlt und verfestigt sich der Zementklinker und bewegt sich weiter vorwärts. Es verlässt den Ofen durch die Ofenöffnung und gelangt in das Kühlsystem. In diesem Bereich, Die Gastemperatur beträgt bis zu 1400 °C und die Temperatur schwankt stark. Sehr gravierend sind auch das Zermahlen des Klinkers und die Erosion des Luftstroms. Das feuerfeste Material der Kühlzone muss verschleißfest sein, Alkali-Korrosionsbeständigkeit, und gute Thermoschockbeständigkeit. Üblicherweise werden Siliciumdioxid-Molybdän-Steine oder Anti-Abplatz-Steine mit hohem Aluminiumoxidgehalt verwendet.
Vordere und hintere Ofenöffnung
Die hintere Ofenmündung befindet sich an der Verbindung zwischen dem Vorklinkerofen und der Drehrohrofenanlage. Die Temperatur in der Subregion ist relativ niedrig, Es unterliegt jedoch einer chemischen Erosion durch das Mahlen von Zementrohstoffen und den im Ofen zirkulierenden und angereicherten Alkali- und Schwefelverbindungen; Die vordere Ofenmündung befindet sich im Drehrohrofen. An der Entladeposition, Die Temperatur schwankt stark und die Klinker- und Luftströmungserosion ist relativ schwerwiegend, was eine hohe Verschleißfestigkeit erfordert, Thermoschockstabilität, und Abplatzfestigkeit des Materials.
Die feuerfesten Materialien am vorderen und hinteren Ofeneingang müssen eine gute Verschleißfestigkeit aufweisen, Alkalibeständigkeit, und Abplatzfestigkeit. Korund, korundweich, Gussstücke aus Mullit-Siliziumkarbid, Feuerfeste Gussteile mit hohem Aluminiumgehalt, usw. werden häufig verwendet.
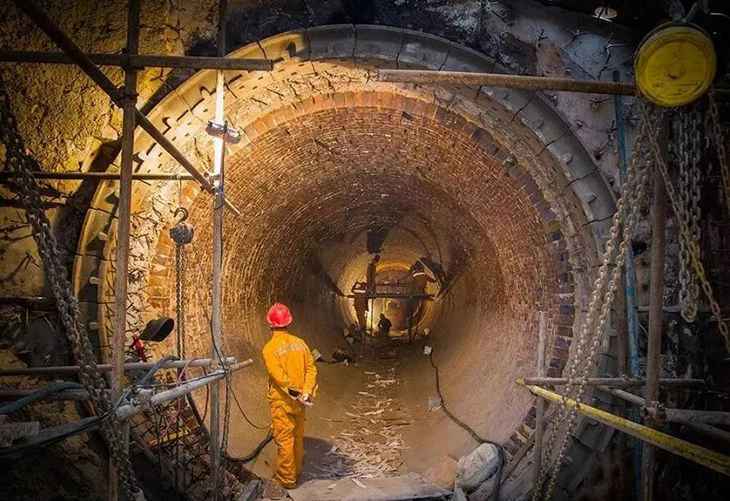
Kohleinjektionsrohr
Das Kohleinjektionsrohr ist ein Rohr, das Brennstoff und Luft direkt transportiert, um Wärme bereitzustellen. Das vordere Ende des Kohleinjektionsrohrs wird direkt von der Wärmestrahlung der Hochtemperaturflamme sowie dem Mahlen und der Erosion von Zementklinker und Luftstrom beeinflusst. Denn moderne Drehrohröfen verarbeiten auch feste Abfälle und Hausmüll gemeinsam, Gefährliche Verbindungen wie Alkali, Schwefel, und Chlor greifen die Materialien der Kohleinjektionsrohre stark an. Verbunden mit den durch Temperaturschwankungen verursachten Thermoschockeffekten, Feuerfeste Materialien müssen eine gute Beständigkeit gegen chemische Erosion und Temperaturschockabplatzungen aufweisen.
Abhängig von der Materialnutzungsumgebung, Kohleinjektionsrohre verwenden meist Korund-Mullit-Gussmassen, Stahlfaserverstärkte Gussteile, Gussteile mit niedrigem Zementgehalt und hohem Aluminiumgehalt, usw.
Tertiärer Luftkanal
Der Tertiärluftkanal ist ein Heißluftkanal, der den Kühler und den Vorklinkerofen verbindet. Es dient dazu, die Abwärme des Zementklinkers zur Wiederverwendung in den Vorkalzinatorofen zu transportieren. Die Arbeitsumgebung in Tertiärluftkanälen ist rau, insbesondere an Kniestücken und Verschlussventilen. Der Luftstrom mit hoher Temperatur transportiert eine große Menge Staub und Alkali, Schwefel, und Chlorverbindungen, die das Material verschleißen und erodieren, Dadurch lockert sich das Material und blättert ab.
Bei den tertiären Luftkanalmaterialien wird vor allem die Verschleißfestigkeit berücksichtigt, Beständigkeit gegen Alkalierosion, und Abplatzfestigkeit. Hochfeste, alkalibeständige Ziegel, hochfeste, alkalibeständige Gussmassen, bruchsichere Gießmassen, usw. verwendet werden kann.
Welche feuerfesten Materialien werden in Zementdrehrohröfen verwendet??
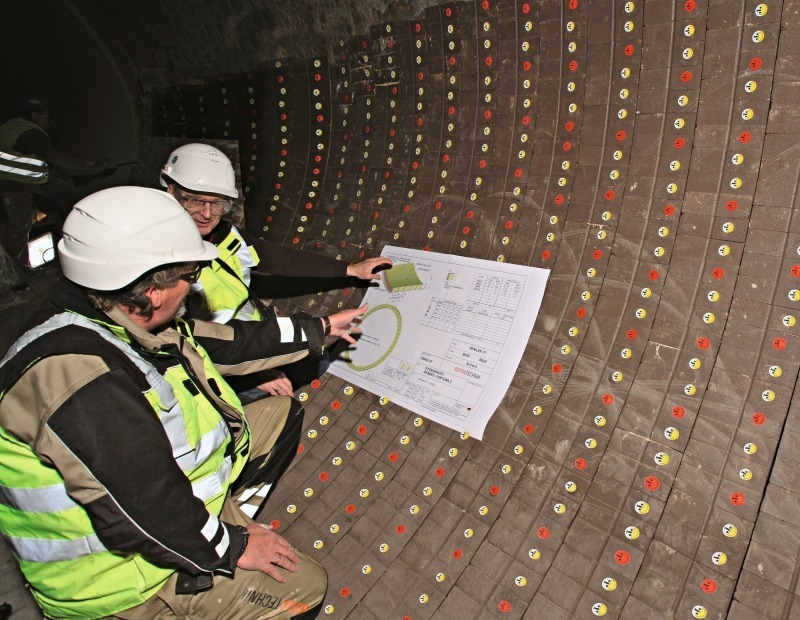
Teile für Drehrohröfen | Feuerfeste Materialien |
Zersetzungszone | Spinellsteine, Abplatzungssichere Ziegel mit hohem Aluminiumoxidgehalt, Silizium-Molybdän-Steine und Steine mit hohem Aluminiumoxidgehalt, usw. |
Obere Übergangszone | Silizium-Molybdän-Steine, Magnesia-Aluminiumoxid-Spinellsteine, und spezielle, abplatzungssichere Ziegel mit hohem Aluminiumoxidgehalt, usw. |
Schießzone | Spinellsteine, Abplatzungssichere Ziegel mit hohem Aluminiumoxidgehalt, Silizium-Molybdän-Ziegelsteine mit hohem Aluminiumoxidgehalt, usw. |
Untere Übergangszone | Rote Silica-Molybdän-Ziegel und Periklas-Spinell-Ziegel, usw. |
Kühlzone | Silizium-Molybdän-Steine oder Abplatzungssichere Ziegel mit hohem Aluminiumoxidgehalt, usw. |
Vordere und hintere Ofenöffnung | Korund, Mullit-SiC-Gussstücke, usw. |
Kohleinjektionsrohr | Korund-Mullit-Gussstücke, Stahlfaserverstärkte Gussteile, Gussteile mit niedrigem Zementgehalt, usw. |
Tertiärer Luftkanal | Hochfeste, alkalibeständige Ziegel, hochfeste, alkalibeständige Gussmassen, bruchsichere Gießmassen, usw. |
WeChat
Scannen Sie den QR-Code mit wechat