Reduktionsofen für Magnesiummetall
The production of magnesium metal is mainly smelted through a “magnesium metal reduction furnace”. As a high-temperature smelting equipment, a magnesium metal reduction furnace plays a vital role in the extraction of magnesium. This article will introduce the working principle, structural characteristics, production process of magnesium metal reduction furnace, and its important role in magnesium smelting.
Introduction of magnesium metal reduction furnace
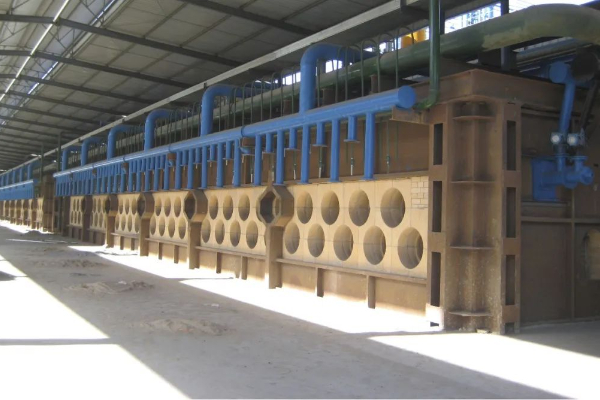
The magnesium reduction furnace is the core equipment of magnesium production. The externally heated horizontal reduction tank reduction furnace is generally used. The traditional magnesium reduction furnace generally adopts the structure of the heat return heating reduction tank. The flame and flue gas in this traditional structure of the reduction furnace go over the fire baffle wall into the furnace, pass through the reduction tank from top to bottom, and quickly discharge from the furnace through the fire hole. The exhaust temperature can be as high as about 1200℃, which cannot be well recycled and reused, and energy waste is serious.
Zusätzlich, the traditional magnesium reduction furnace uses raw coal as fuel, with low combustion efficiency and serious pollution. Darüber hinaus, this combustion method leads to uneven temperature inside the furnace of magnesium reduction furnace, and inflexible combustion temperature control, resulting in a generally short life of the reduction tank and low quality of the finished magnesium metal produced.
According to the different fuels used, it can be roughly divided into two categories: reduction furnaces heated by gas or heavy oil and reduction furnaces fueled by coal. Reduction furnaces fueled by gas or heavy oil are usually reduction furnaces with 16 horizontal tanks, with specifications of 10.54×3.59×2.94 (M). This reduction furnace is a rectangular furnace, with a center distance between reduction tanks of about 600mm. The tanks are arranged in a single row on one side, and there are generally multiple low-pressure burners on the back of the furnace. The flame enters the furnace space from the combustion chamber, bypasses the periphery of the reduction tank, and relies on the chimney suction to draw the flue gas after combustion into the branch flue at the bottom of the furnace, and enters the chimney after passing through the flue and the flue gate. The secondary air is sent into the furnace by the secondary air duct through the second layer of the secondary air duct at the bottom of the furnace. A combustion chamber or smoke chamber is set between the two reduction tanks at the bottom of the reduction furnace. The reduction furnace is both a downdraft furnace and a heat storage furnace. There are generally 16 reduction tanks made of nickel-chromium alloy steel in the furnace. Der 16 reduction tanks are divided into four groups, das ist, 4 reduction tanks form a group, which are connected to a vacuum unit (the vacuum unit consists of a slide valve pump and a Roots pump). Each reduction furnace is also equipped with a spare vacuum unit. Deshalb, a reduction furnace generally has 5 vacuum units. Each reduction furnace is equipped with a water ring pump as a pre-pump.
Magnesium metal reduction furnaces are mainly coal-fired. With the continuous development and progress of magnesium smelting technology, a variety of coal-fired reduction furnaces have emerged, typical of which are the following.
1. Single-chamber single-side single-row tank reduction furnace This furnace type is similar to the coal gas and heavy oil reduction furnace type, with single-side single-row reduction tanks. The combustion chamber is set at the back, Und 14 Zu 16 reduction tanks are installed in the furnace, and a fire hole is set between the two reduction tanks. Since this furnace type has only a single row of tanks and is arranged on one side, it is very convenient to operate, and the workshop layout is easy to mechanize, but its output and thermal efficiency are low. This furnace type belongs to a rectangular downdraft kiln. The flame is reflected from the combustion chamber to the top of the furnace through the fire baffle. The flame is drawn downward by the chimney, causing the reduction tank to be heated, and then passes through the fire hole and the branch flue to the main flue for discharge.
2. Double-chamber, double-sided, double-row reduction tanks This type of furnace is also a rectangular downdraft kiln, equipped with 10 reduction tanks, 5 of which are arranged in upper and lower positions at both ends in the length direction. The furnace is equipped with four combustion chambers (two on each side) symmetrically distributed on both sides, and there is a beam-type grate inclined at 15° in the combustion chamber. The flames flow from the combustion chambers on both sides of the kiln over the fire-blocking wall to the top of the kiln in the center of the furnace, and then the flames flow back to the fire-absorbing holes and branch flues at the bottom of the furnace and are discharged into the chimney from the main flue at one end. The advantages of this furnace are simple furnace structure, compact arrangement of tanks, and high utilization rate of furnace space. Its disadvantages are that the four sides of the furnace are operating surfaces, adding coal to burn fire and reducing magnesium, slagging, and loading interfere with each other, the operating conditions are poor, and the workshop layout is difficult. This type of furnace also has an expanded furnace space and 14 Zu 22 tanks.
3. Single-chamber double-sided double-row tank reduction furnace This furnace type is a reduction furnace with double rows of tanks on both ends and a single-chamber fire. Six tanks are installed in the upper and lower rows on each end, with a total of 12 tanks. Multiple combustion chambers are set on one side. This makes coal-burning operations more convenient and space utilization is higher, but the number of reduction tanks is limited and the output is small.
4. The most widely used single-fire chamber single-sided double-row tank reduction furnace in China. This type of furnace also belongs to the externally heated flame reflection furnace (commonly known as downdraft furnace). The reduction tanks in the furnace are staggered and arranged up and down, and the space utilization rate is high; there is no restriction on the length of the furnace, so more reduction tanks can be arranged, generally 30 Zu 40; the reduction tank is open on one side, which is convenient for connection with the vacuum unit; the combustion chamber is set behind the furnace and separated by a fire baffle wall. The flame is reflected from the combustion chamber through the fire baffle wall to the top of the furnace. Under the chimney suction, the flame goes downward, heating the reduction tank, and then discharged through the fire hole at the bottom of the furnace and the branch flue to the main flue. Compared with the other furnace types mentioned above, this furnace type has a large output, high space utilization, low energy consumption, and a good economy, so it has been widely used in China.
Large regenerative magnesium reduction furnace
The regenerative high-temperature combustion technology is the most advanced combustion technology in the world today. It is to arrange nozzles evenly distributed on the furnace walls on both sides of the furnace. When the nozzles on one side are burning as burners, the nozzles on the other side are used as flues for smoke exhaust. After a reversing cycle, through the switching of the reversing valve, the nozzles on the side burning as burners become flues for smoke exhaust, while the nozzles on the other side that were originally used for smoke exhaust are used as burners. In this way, the heating, efficient recovery of flue gas heat, and high-temperature preheating of air are completed at the same time. The exhaust side nozzle enters the regenerative chamber through the high-temperature gas channel, and its temperature has dropped to below 150°C through heat exchange with the heat storage body in the regenerative chamber. Then it leaves the regenerative chamber, passes through the reversing valve and the smoke exhauster, and is finally discharged into the atmosphere through the chimney. Gleichzeitig, the air enters the high-temperature regenerator on the other side, which has been preheated by high-temperature flue gas in the previous reversing cycle and is preheated to 900-1050°C. After leaving the regenerator, it is ejected through the high-temperature gas channel through the nozzle on the side wall of the furnace. The high-temperature air and fuel ejected from the nozzle are mixed and burned in the furnace.
The new regenerative magnesium reduction furnace has the following main features:
① The regenerative combustion form of diffuse combustion can form a flame type completely different from the traditional flame, forming a particularly uniform temperature field in the furnace, and improving the heating uniformity of the reduction tank.
② The low-oxygen combustion technology not only enhances the radiation and convection exchange of high-temperature flue gas to the reduction tank but also reduces the scouring and oxidation of the flame to the reduction tank, extending the service life of the reduction tank.
③ Save energy and reduce fuel consumption. The use of regenerative combustion technology can utilize the waste heat of flue gas to almost the limit, maximize the recovery of flue gas latent heat, and preheat the air and coal gas to close to the furnace gas temperature at the same time. The exhaust temperature can be lower than 150℃, the waste heat recovery rate is greatly improved, and energy saving and consumption reduction are very obvious.
④ Improve the heating environment of the reduction tank, form a reducing atmosphere around the reduction tank, reduce the oxidation of the reduction tank, and increase the service life of the reduction tank.
⑤ Reduce pollution to the environment. The regenerative combustion technology not only saves energy and reduces flue gas emissions, but also greatly reduces the content of harmful gases such as NOx in the flue gas, reducing environmental pollution.
⑥ High-temperature anti-corrosion (Anti-Oxidation) and wear-resistant materials are applied to the reduction tank, effectively improving the service life of the reduction tank.
⑦ Centralized management and decentralized control are adopted to form a safe, advanced, practical, and reliable remote automatic adjustment control system. Reduce a large number of equipment operators.
Continuous regenerative magnesium refining furnace
Continuous regenerative magnesium refining furnace refers to the use of waste heat in magnesium refining furnaces, which has changed from intermittent heat storage to continuous heat storage. This device is called a heat recovery pump. When it works, smoke exhaust and air blowing are carried out simultaneously. The high-temperature flue gas transfers heat to the heat storage body in the flue gas channel by convection and radiation. Gleichzeitig, the heated heat storage body quickly transfers heat to the combustion air on the low-temperature side, and the air can be heated very quickly. The continuous regenerative magnesium refining furnace has the following main features:
①High heat exchange rate. Hohe Wärmeleitfähigkeit, and high blackness material, with large heat exchange area, can achieve high wind temperature and low smoke temperature.
②Continuous operation. Continuous air supply and smoke exhaust, no need for reversing, stable furnace pressure, no frequent disturbance of flow field and temperature field, laying the foundation for low oxygen combustion.
③Long life. Good anti-oxidation performance.
④Super strong heat exchange element structure, extremely low operating cost, no maintenance required.
⑤Use heat exchange elements with large specific surface areas as heat exchangers, which is easy to install and arrange.
⑥High temperature anti-corrosion (Anti-Oxidation) and wear-resistant materials are used in refining crucibles to effectively improve the service life of crucibles.
What are the refractory materials used in magnesium reduction furnaces?
The refractory materials used in magnesium reduction furnaces generally include Ziegel mit hohem Aluminiumoxidgehalt, magnesium-alumina refractory castables, usw. These materials have good high-temperature resistance, Thermoschockstabilität, and chemical corrosion resistance.
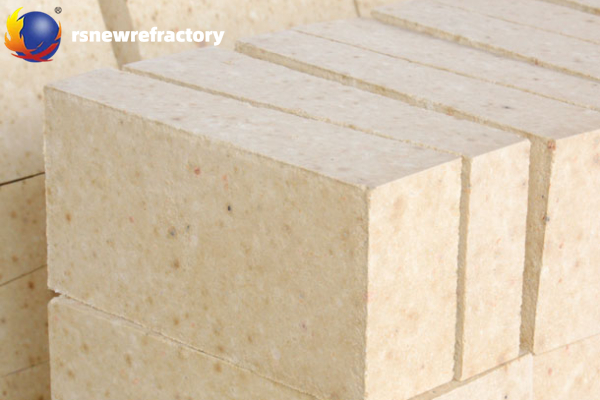
WeChat
Scannen Sie den QR-Code mit wechat