Einführung von feuerfesten Ziegeln für elektrischen Bogenofenboden
Elektrolichtbogenofen (EAF) is an important equipment used for steelmaking in the metallurgical industry. It produces steel by heating metal scraps or raw materials with electric arcs. During the operation of the electric arc furnace, the furnace bottom needs to withstand high temperature, high pressure,e, and chemical corrosion. Deshalb, the refractory bricks of the furnace bottom must have extremely high fire resistance, Schlagfestigkeit, Wärmeschockbeständigkeit, and good chemical stability. These requirements determine the importance of refractory bricks in the selection and use of electric arc furnace bottoms.
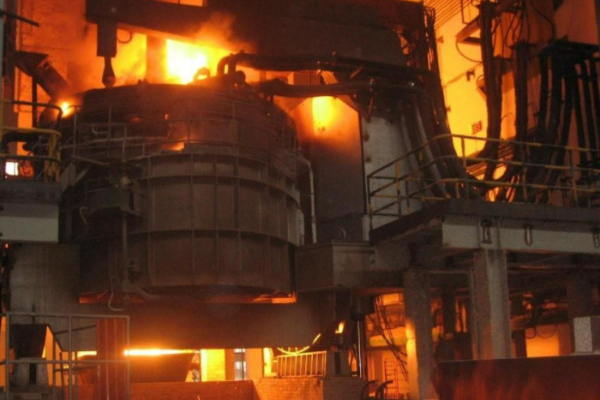
What conditions should the refractory bricks of an electric arc furnace meet?
① Low resistivity;
② Low thermal conductivity;
③ Small change in resistance with temperature;
④ Good thermal shock resistance and slag resistance;
⑤ Long service life and low consumption.
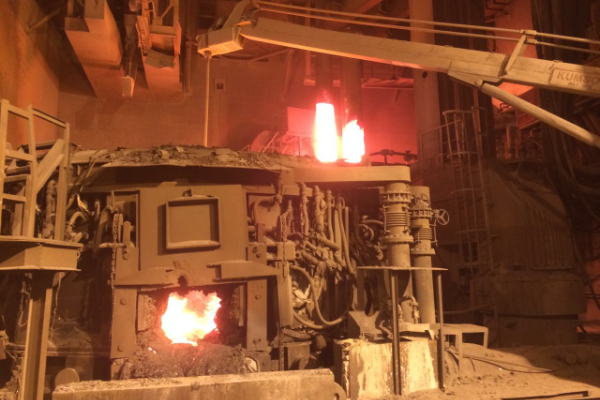
Introduction to refractory materials for EAF bottom
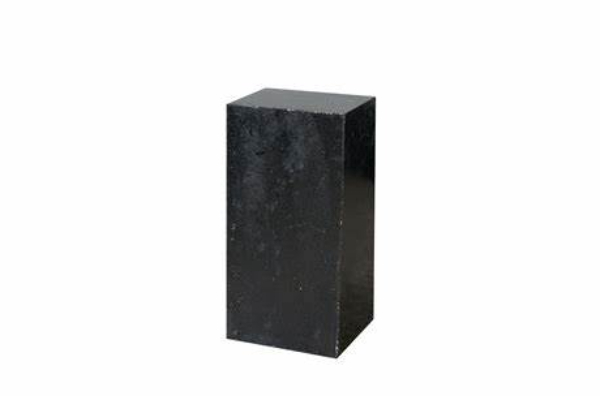
To meet the above conditions, conductive Magnesia-Kohlenstoff-Steine are directly laid on the copper plate of the conductive furnace bottom, and a layer of Rammenmaterial with good conductivity is covered on the built furnace bottom, with a thickness of about 150mm. Während des Produktionsprozesses, carbon-containing magnesium materials can be used for repair. This refractory furnace bottom can be repaired hot and cold and has a longer service life than other furnace types.
For magnesia carbon bricks that meet the above requirements for the conductive furnace bottom of the DC arc furnace, only when the key material (Graphit) in the magnesia carbon brick reaches a certain amount of residual carbon, can the carbon-containing bonding matrix be used to obtain higher conductivity.
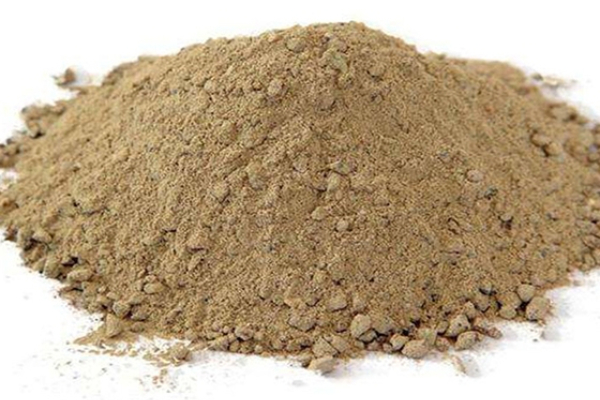
WeChat
Scannen Sie den QR-Code mit wechat