Einführung in den Herstellungsprozess von Schamottesteinen
Clay fire brick is a commonly used refractory material, widely used in high-temperature industrial furnaces such as steel, Glas, Zement, and ceramics. It has excellent thermal shock resistance, Hochtemperaturstärke, und chemische Stabilität. This article will introduce the production process of refractory clay bricks in detail to help everyone better understand this important refractory material.
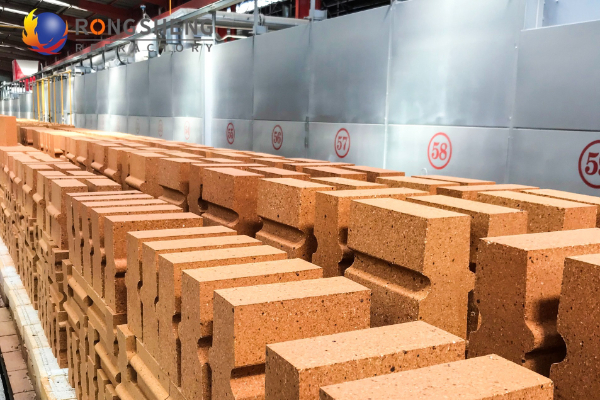
Clay fire brick production process
① Raw material preparation
Mainly the preparation of clinker and the preparation of bonding clay. The preparation of clinker is to calcine the refractory clay raw material at a high temperature into clinker, and then crush, Bildschirm, and pulverize it into various levels of granular materials and fine powder. The preparation of bonding clay is to crush, dry, finely pulverize, and slurry the clay. The clay clinker is roughly crushed into blocks less than 50mm and then crushed into various levels of aggregates of 5-2mm. The sieved material enters the machine to be ground into fine powder less than 0.5mm. The bonding clay is generally dried, and then roughly crushed, pulverized, and finely pulverized into fine powder less than 0.5mm, or mixed with clinker to make fine powder.
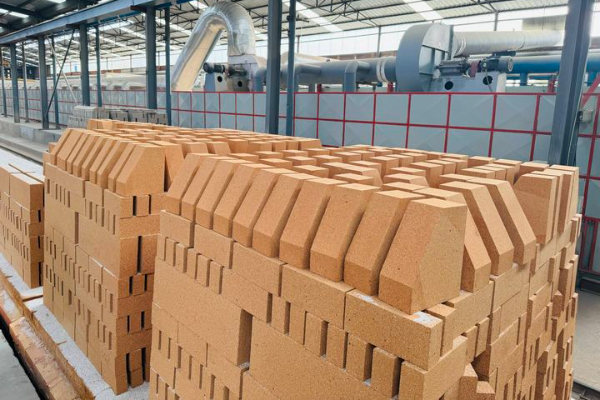
② Batching and mixing
Batching, mischen, and molding: The calcined refractory clay clinker is used as the lean material, and a certain proportion of binding clay is added to make a mixture. The clinker accounts for a high proportion of the mixture, which is called a multi-clinker product. This kind of product has high volume stability and other good properties, but it needs to be strongly molded. Derzeit, multi-clinker bricks are the most widely produced and used products. The mixture is molded after mixing or after being trapped and then mixed. There are many molding methods, but the semi-dry pressing molding method is currently used for multi-clinker products. The molding pressure has an impact on the density, structural strength, and slag resistance of the bricks.
The proportion of mud includes the mass ratio and particle ratio between clinker, binder clay, Wasser, and additives. The amount of binder clay and water added varies according to the molding method. The ratio of plastic molding is: clinker: clay is (7-5): (3-5), and the water content is 16%-20%; the ratio of semi-dry molding is: clinker: clay is (9-7): (1-3), and the water content is 3.5%-8.0%. Various granular materials are added to the mixing equipment in sequence, and various binders are added to make a uniform mud.
③ Drying clay fire brick bricks
The moisture content of dried clay brick blanks varies depending on the molding method. Semi-dry pressing molding has a low moisture content in the blanks. When the moisture evaporates, there is almost no shrinkage. It can be dried quickly or directly loaded into the kiln. Brick blanks with high moisture content can be dried by appropriate natural air drying or hot air heating in advance and then sent to the tunnel kiln. The key factor in controlling the drying process is the drying speed. The principle should be to ensure that the blanks do not deform, crack, and have a certain strength. The moisture content of the blanks that finally enter the firing kiln is controlled to be below 2%.
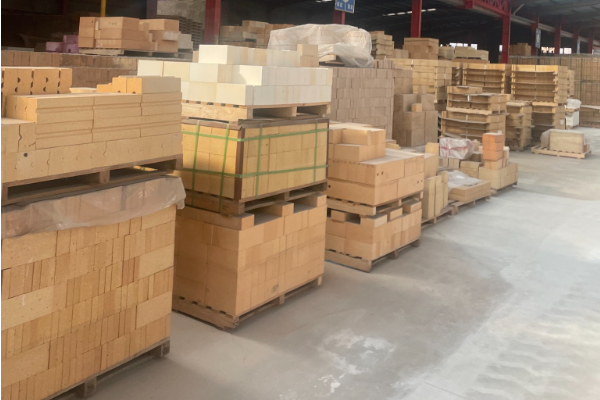
④ Clay brick firing
The purpose of firing is to sinter the bricks to give them certain dimensions, porosity and density, hohe mechanische Festigkeit, gute Lautstärkestabilität, and good fire resistance. Während des Brennvorgangs, the matrix of the bricks undergoes a series of physical and chemical changes, and various reactions are carried out in the downdraft or tunnel. The firing process is roughly divided into four stages.
- When the temperature reaches 200℃, the temperature should not be raised too fast to prevent the green body from cracking. When firing in a tunnel kiln, the temperature of the first 4 parking spaces should not exceed 200°C.
b.200-900℃ The temperature rise should be accelerated at this stage to facilitate the chemical reaction of organic matter and impurities in the billet. During the period of 600-900℃, a strong oxidizing atmosphere should be maintained in the kiln to avoid the appearance of “black core” waste bricks. - 900-1380℃: (The temperature rise should be stable during the high-temperature stage, and the oxidation atmosphere should be maintained to ensure that the brick body is heated evenly and to prevent cracking of the brick body. Because at high temperatures above 1100℃, the sintering shrinkage is very strong, and the shrinkage rate reaches 5%, so it is very important to keep the temperature gradient gentle and eliminate internal stress.
- The fire-stopping temperature of clay bricks is generally 100-150℃ higher than the sintering temperature. If the sintering temperature range of the sintered clay used is narrow, the fire-stopping temperature should be lower, around 50-100℃ is more suitable. The firing temperature of clay products It should be ensured that the binding clay is fully softened so that it can fully react with the clinker fine powder and coarse particle surface layer to achieve the purpose of bonding the clinker particles and making the product obtain appropriate strength and volume stability. The firing temperature is generally 1250-1350℃. If the A1203 content is high, the firing temperature of the product should be appropriately increased, about 1350-1380°C, and the firing heat preservation time is generally 2-10 hours to ensure that the reaction in the product is sufficient and that the surface and inner qualities of the product are consistent.
- During the cooling stage, according to the lattice changes of the product in the cooling section, the temperature should be increased rapidly at high temperatures above 1000°C, and the cooling rate should be slowed down at 1000-800°C. Tatsächlich, in actual production, the cooling rate actually adopted will not cause the risk of cold cracking of the product.
WeChat
Scannen Sie den QR-Code mit wechat