Introduction of Magnesia Carbon Bricks Production Process
Magnesium carbon bricks are a high-temperature resistant refractory material, mainly used for the lining of high-temperature kilns. Mgo-c bricks can be used in converters, electric arc furnaces, naběračky, a další části, and is an important refractory material of kilns.
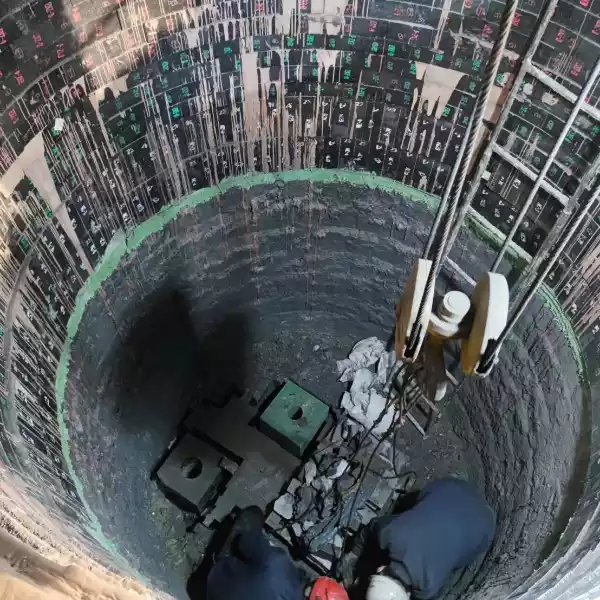
Magnesia carbon bricks have the characteristics of high-temperature resistance, silná odolnost proti struskám, dobrá odolnost proti tepelným šokům, and low high-temperature creep. The main components of magnesia carbon bricks include magnesia and carbon. The following is the specific production process of magnesia carbon bricks:
Two methods of making magnesium carbon bricks
There are two ways to make magnesia carbon bricks: fired oil-impregnated magnesia carbon bricks and unfired magnesia carbon bricks. The former brick-making process is more complicated and is rarely used. The following is the production method of unburned magnesia carbon bricks.
How are magnesia carbon bricks produced?
Mud preparation
The choice of particle critical size is important when breeding. Fine aggregate particles can reduce open porosity and enhance anti-oxidation ability. Však, the small aggregate particles will increase the closed pores and reduce the bulk density. Navíc, fine-grained MgO aggregates are easy to react with graphite, and it is generally considered that the particle size is 1mm. Under the condition of high-pressure forming equipment, the particles of magnesia tend to be miniaturized.
Graphite is added to the ingredients
The quality and quantity of graphite added to the ingredients is critical. Generally speaking, increasing the graphite content in refractory bricks will increase the slag resistance and thermal shock stability of refractory bricks, but the strength and oxidation resistance will decrease. If the carbon content in magnesia carbon bricks is too small (<10%), If the network skeleton cannot be formed in the refractory brick, the advantages of carbon cannot be effectively exerted. Proto, the carbon content is more appropriate in the range of 10-20%.
Raw material mixing for magnesium carbon bricks production
During the mixing process, to make the graphite evenly surround the magnesia particles, the feeding sequence should be: magnesia particles → binder → graphite → magnesia fine powder, and additive powder. Due to the large content of graphite, low density, and very small amount of additives, it takes a long time to mix evenly, but if the mixing time is too long, the graphite and fine powder around the magnesia particles will easily fall off, so the mixing time should be appropriate.
Forming of magnesia carbon brick
The forming of MgO-C bricks is an important factor to make the structure of refractory brick compact: the quality and quantity of graphite added to the ingredients are very important. Due to the large amount of graphite in the mud and the small critical particles of the aggregate, it is advisable to use high-pressure molding and press it strictly by the operating procedures of light weight first, heavy pressure, and multiple pressures to avoid forming cracks. It is better to adopt the operating procedures of vacuuming, exhausting and pressurizing. Navíc, the surface of the high-pressure-formed adobe is very smooth, and it is easy to slide during handling and building. Proto, the formed adobe should be impregnated or coated with 0.1-2mm thick thermosetting resin to form a resin film to prevent sliding. This treatment is generally referred to as anti-skid treatment.
MgO-C bricks heat treatment
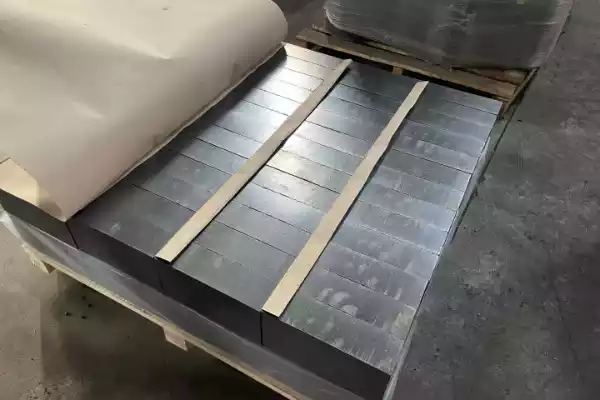
The molded magnesia carbon adobe must be hardened before it can be used, and the temperature epidemic of hardening has a great influence on the performance of refractory bricks. It has been proved by research that the hardening treatment at 200-250°C is more suitable, which is good for ensuring the bulk density of the brick and reducing the porosity. When it is higher than 250°C or lower than 200°C, the hardening treatment will bring adverse effects. It is necessary to strictly control the air. Usually at 50-60°C, due to the softening of the resin, it should be properly kept warm; at 100-110°C, because a large amount of solvent is discharged, it should be kept warm; at 200-250°C, to complete the reaction, it should also be properly kept warm.
WeChat
Naskenujte QR kód pomocí wechat