The process of producing fused magnesia sand in electric arc furnace
Fused magnesia sand is a high-purity refractory raw material made from magnesite or light-burned magnesium powder, which is melted at high temperature in an electric arc furnace and then cooled. Široce se používá v metalurgii, stavební materiál, electrical engineering, the chemical industry, a další průmyslová odvětví. This article will introduce in detail the complete process of producing fused magnesia by electric arc furnace.
The process flow of producing fused magnesia sand in an electric arc furnace mainly includes: raw material batching, arc melting, crushing, sorting, pulverizing, screening, magnetic separation, classification and packaging, atd.
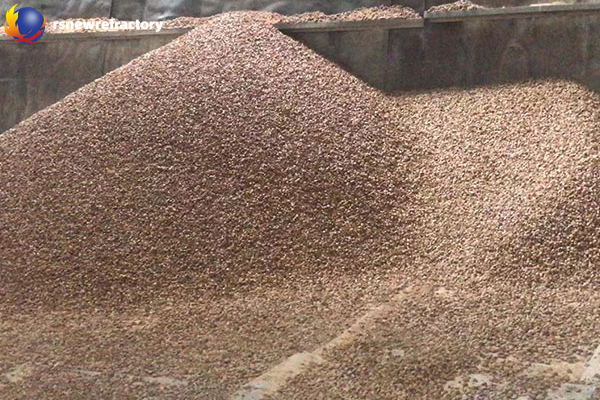
The process of producing fused magnesia sand
Raw material ratio
China has abundant high-quality magnesite ore with high magnesium oxide content and easy mining, so it is widely used as the raw material for fused magnesium oxide. Using magnesite as raw material, magnesium carbonate decomposes to produce CO2 gas. Since a large amount of gas is discharged from the furnace, it affects the fusion process:
MgCO3→MgO+CO2↑
It has an adverse effect on the formation of the crystal band of fused magnesium oxide. Due to the large amount of dust flying, material loss and energy consumption increase, and the workshop production environment worsens. Však, since high-quality magnesite ore is easy to obtain and the price is very low, fused magnesium oxide is still the most widely used raw material.
Ingredients of fused magnesia sand
① Magnesite. The content of magnesium oxide and chemical composition in magnesite ore directly affect the quality of electrofused magnesium oxide, and also directly affect the grade ratio of electrofused magnesium oxide during the electrofusion process. Proto, in order to ensure the quality and grade ratio of electrofused magnesium oxide, various ores must be properly proportioned and smelted.
② Brucite. The ore source of brucite in Liaoning Province is very rich, and the magnesium oxide content in brucite is higher than that of magnesite ore. It is also a raw material for making electrofused magnesium oxide
③ Lightly burned magnesium oxide. Using lightly burned magnesium oxide as the raw material for electrofused magnesium oxide can improve the production environment and reduce transportation costs. Since less gas is discharged during electrofusion and the composition is more uniform, it is beneficial to improve the quality of electrofused magnesium oxide.
Some electrofused magnesium oxide in China is made into balls with lightly burned magnesium oxide and put into the furnace for electrofusion. The magnesium oxide content of lightly burned magnesium oxide reaches 98%, and this material can produce white, large-crystalline electrofused magnesium oxide. Však, the high cost of ball formation affects production costs. V současnosti, some manufacturers use reverberatory furnaces to lightly burn magnesium oxide and add it to the melting furnace for electric melting with a certain particle size. The quality of electric-melted magnesium oxide is better than that of magnesite ore, and the cost is cheaper than that of using ball material as raw material, so it has been promoted to a certain extent.
④ Sintered magnesia. In order to meet the special requirements of some electrofused magnesia, sintered magnesia must sometimes be used as the electrofused raw material in the electrofused process. Například, seawater magnesia is used as the electrofused raw material. Obvykle, magnesium hydroxide is produced by treating seawater and lime milk, and magnesium hydroxide is calcined into light-burned magnesia. Light-burned magnesia can also be produced by other methods (see the preparation method of industrial magnesia for details), and light-burned magnesia is used as the raw material to produce electrofused magnesia. AusT and Rutter et al. believe that a very small amount of impurity gas (phase) is also an impurity of the crystal, which can significantly affect the growth of grains. The role of the impurity phase is to increase the energy required for grain boundary movement. When the grain boundary meets the second phase, the crystal energy decreases, and the amount of decrease is proportional to the cross-sectional area of the second phase, so the grain boundary energy must be increased so that the grain boundary can leave the second phase and continue to move. And when the grain boundary meets the second phase, the grain boundary with the same cross-sectional area as the second phase must be deformed. The more the second phase, the smaller the limit size of grain growth.
On the other hand, in order to reduce the apparent porosity of electrofused magnesia, the gas discharge of raw magnesia should also be reduced as much as possible. Proto, the use of sintered magnesia electrofusion has significant advantages.
Arc furnace melting
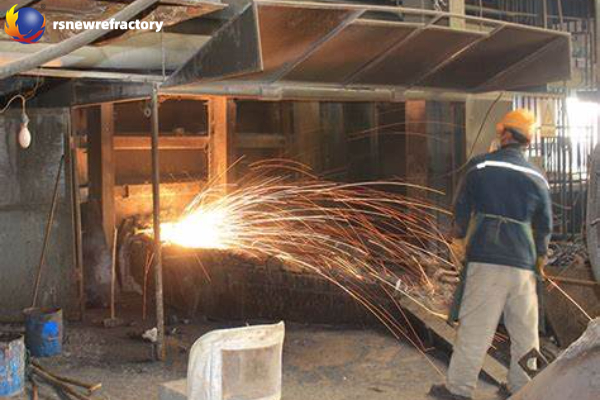
These characteristics are related to the quantum mechanical nature of atoms and molecules, such as the size of the ion radius, the potential value of the ion, and the outer structure of the ion’s electrons. The ion size, mass, and charge of magnesium oxide, the binding characteristics and strength between cations and anions, the polarization of ions, and the crystal structure determine that it is a high melting point compound.
Melting point and structural parameters of magnesium oxide: cation radius 0.074mm; anion radius 0.53 mm; structure type NaCl; coordination number 6; effective coordination number 8.5; density 3.65g/cm3; bod tání 2800 ℃.
The most important process of electro-fused magnesium oxide manufacturing is to use various magnesium raw materials to generate high temperatures through various forms of heating methods to melt magnesium materials (MgO) and turn them into magnesium oxide melt. To melt magnesium oxide, a large amount of heat energy must be consumed to overcome the attraction between ions. The method of melting magnesium oxide by generating high temperatures through a strong electric arc is called arc melting. This melting process generally includes a series of physical and chemical changes such as heat conduction, dehydration, decarburization, tání, crystallization, and crystal growth.
① Dehydration process. There is a dehydration process when using brucite as raw material. The main component of brucite is magnesium hydroxide Mg(OH)2. Its dehydration process is:
Mg(OH)2→MgO+H2O
② Decarburization process. There is a decarburization process when using magnesite as raw material. The decarburization process includes two aspects. On the one hand, it is the thermal decomposition of magnesite ore. The main component of magnesite ore is magnesium carbonate (MgCO3):
MgCO3→MgO+CO2
On the other hand, since graphite powder additives (auxiliaries) are often added to the raw material magnesium oxide during the electric melting process, graphite powder needs to be laid at the lower end of the three electrodes (grafitové elektrody) to form a triangle or star-shaped conductor during the start-up process of the electric melting furnace. During the power-on process, the graphite is burned or completely burned to remove the graphite.
C+O2→CO2↑
③ Melting process. The melting process is the process in which the magnesium ions and oxygen ions in magnesium oxide overcome the constraints of the lattice energy in the single crystal and become able to move freely under the action of the heat energy generated by the strong electric arc. In other words, when magnesium oxide is heated to a certain temperature (melting point), it will change from solid to liquid, which is called melting. A large amount of electrical energy is consumed in this process. According to the thermal balance calculation of the electric fused magnesium oxide producer using brucite as raw material to produce electric fused magnesium oxide, the heat consumption ratio is as follows: the heat consumption value of magnesium oxide crystal formation is 34.9%, the heat consumption value of slag skin is 15.3%, the heat consumption value of loose sand is 3.0%, the heat consumption value of cooling water is 8.4%, the heat consumption value of water for cooling the furnace shell is 7.9%, the heat dissipation value of the furnace surface is 6.4%, and the heat value carried away by the flue gas is 28.8%. The power loss value is 3.2%.
Cooling and crystallization
After melting is completed, stop the power supply and enter the cooling stage.
Natural cooling: The molten pool cools down naturally, and the crystals gradually crystallize.
Crystal structure: a dense magnesia block with large grains is formed.
Cooling time: Usually, more than 24 hours is required to ensure the formation of a complete crystal structure.
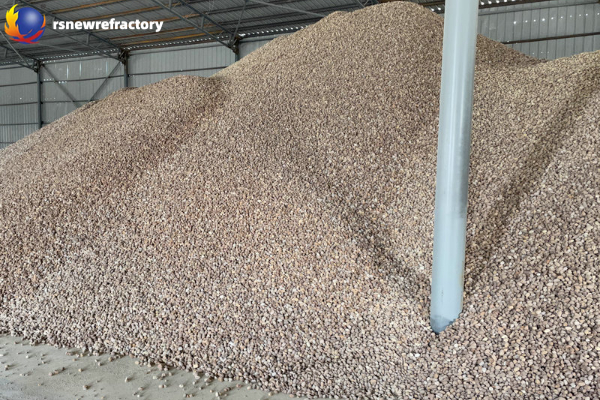
Crushing and screening
Coarse crushing: Use a jaw crusher to crush large pieces.
Medium and fine crushing: Further crush into the particle size required by customers.
Screening and grading: Screening according to different particle sizes, such as 0-1mm, 1-3mm, 3-5mm.
Iron and impurity removal: Use a magnetic separator to remove mechanical impurities.
WeChat
Naskenujte QR kód pomocí wechat